Beyond Steel: Mastering Metal Properties for Your Roll Forming Project
A deep understanding of metal properties is your secret weapon in roll forming. It gives you the confidence to make the right material choices, ensuring your projects meet quality standards, budget constraints, and production timelines. With the right knowledge, you can create high-quality, cost-effective products that truly shine.
While steel is the king of roll forming, it's far from the only option. This versatile process can transform various metals—from aluminum to brass and even pre-painted or perforated options. Each boasts unique qualities that influence its performance and suitability for different applications.
A great project starts with the right metals -- so it’s wise to educate yourself on the pros and cons of each.
While steel is the most common roll-formed metal, there are plenty of other metals used for roll-forming and other metal-forming processes, including:
Knowing the key qualities of each material—such as strength, malleability, ductility, and corrosion resistance—is essential to choosing the right one for your next project. Let’s discuss the most important metals and then break them down into easy-to-follow categories of characteristics.
More Than Steel: Roll Forming, Design & Fabrication
Here are the metals we’ll cover in this chart:
- 1018 cold rolled steel
- Hot dipped G60 galvanized steel
- Hot dipped G90 galvanized steel
- A40 galvannealed steel
- A60 galvannealed steel
- 304 stainless steel
- 316 stainless steel
- 430 stainless steel
- UR52N “duplex” stainless steel
- C360 (“free cutting”) brass
- C93200 tin bronze (aka SAE 660 or “bearing bronze”)
- UNS C11000 (electrolytic tough pitch, or ETP) copper
We’ll judge these roll-forming metals by:
- Surface finish: The exterior’s roughness, waviness, and lay.
- Hardness: How impervious is the metal to scratching and denting?
- Formability: The ability of a workpiece to be manipulated by the roll-forming machine without sustaining damage.
- Minimum bend radius: The minimum radius you can bend a channel without damaging it.
- Corrosion resistance: How well can the metal stand up to harsh environments without rusting or corroding?
- Cost
Beyond The Basics: The Main Properties of Metals
This handy chart shows the most important characteristics of material choices. Download the printer-friendly PDF version here:
GRADE |
FINISH |
STRENGTH & HARDNESS |
FORMABILITY |
TYPICAL MIN. INSIDE BEND RADIUS |
CORROSION RESISTANCE |
COST |
Hot Dipped G60 Galvanized Steel (CS-B) |
0.6 oz./sq. ft. zinc coating. Unique zinc spangling. |
Zinc coating soft. Base metal similar to cold rolled. |
Good |
1/2t (t=thickness) |
Good |
Low |
Hot Dipped G90 Galvanized Steel (CS-B) |
0.9 oz./sq. ft. zinc coating. Unique zinc spangling. |
Zinc coating soft. Base metal similar to cold rolled. |
Good |
1/2t |
Good. Thicker coating than G60 = better resistance. |
Low |
A40 Galvannealed Steel (CS-B) |
0.4 oz./sq. ft. zinc coating. Creates a uniform, matte finish. Usually painted. |
Surface slightly harder than galvanized steel. Base similar to/slightly softer than galvanized. |
Slightly better than galvanized due to annealing |
1/2t |
Good |
More than galvanized due to extra processing |
A60 Galvannealed Steel (CS-B) |
0.6 oz./sq. ft. zinc coating. Creates a uniform, matte finish. Usually painted. |
Surface slightly harder than galvanized steel. Base similar to/slightly softer than galvanized. |
Slightly better than galvanized due to annealing process. |
1/2t |
Thicker coating than A40 = better resistance. |
More than galvanized due to extra processing |
Aluminum (5052-H32) |
Can be anodized, painted, powder coated, etc. |
Soft. Not as strong as steel |
Good |
1t |
Moderate |
Low to Moderate |
304 Stainless Steel (annealed) |
Variety of brushed and polished mirror finishes | Excellent | Limited due to work hardening |
1/2t |
Excellent, but pitting corrosion possible in warm chloride areas |
Moderately high |
316 Stainless Steel (annealed) |
Variety of brushed and polished mirror finishes | Excellent | Limited due to work hardening | 1/2t |
Same as 304 stainless, but safer against pitting, especially in warm chloride areas |
Moderately high |
430 Stainless Steel | Variety of brushed and polished mirror finishes | Can’t be hardened by heat treatment | Low work hardening rate enables easy forming, but low ductility makes rigorous operations difficult |
1/2t |
Excellent; not as good as 304 or 316, a bit lower in 430F variety |
Moderately high, but less than 304 & 316 |
UR52N Stainless Steel (“Super Duplex”) |
Variety of brushed and polished mirror finishes |
High. Can’t be hardened by heat treatment |
Somewhat challenging. Low ductility. Avoid sharp bends. High springback. |
2t |
Better than all other stainless. Resistant to hot chlorides and sulfides. |
Moderately high, but less than stainless grades with high nickel |
Cold Rolled Carbon Commercial Steel Type B (CS-B) (similar to C1010) |
Not the most attractive. Can be blackened, oxidized, or painted. Process does create better finish than hot rolled steel. |
Typically HRB<70. Good, but can’t be increased by heat treatment. |
Good |
1/2t |
Low |
Low |
C260 ¼ hard brass (“cartridge brass 70/30”) |
Fixed finishes (clear-coat raw or antique it), or “live” finishes (change over time by forcing patina effect) |
Equivalent to stainless steel in resilience & form, but not as strong structurally. Lower than carbon steel. |
Good |
1/2t |
Excellent |
Very high (2x-3x cost of stainless) |
C220 ¼ hard bronze (“commercial bronze 90/10”) |
Fixed finishes (clear-coat raw or antique) or “live” finishes (Change over time by forcing patina effect.) |
Equivalent to stainless steel in resilience & form, but not as strong structurally. Higher than copper. |
Good |
1/2t |
Excellent |
Very high (2x-3x cost of stainless) |
UNS C11000 copper (annealed) (electrolytic tough pitch, or ETP) |
Fixed (clear-coat raw or antique it), or “live” finishes (change over time by initiating patina chemically) |
Equivalent to stainless steel in resilience & form, but not as strong structurally (available in various tempers) |
Great ductility means easy roll forming | 0t (At annealed temper. Higher tempers require larger radii.) | Excellent | Very high (2x-3x cost of stainless) |
Roll With It: Material Applications
Choosing the right metal is necessary for any roll forming or metal fabrication project. Whether you're working on infrastructure, solar panels, vehicles, or something else, your material choice will impact the success of your application.
Need help deciding which metal is best for your roll-forming needs?
This article has you covered
Roll Forming Questions? We Have Answers!What is the most common metal used in roll forming? Why are the properties of metals important for roll forming? What are some key properties of metals to consider for roll forming? |
Ready to take the next step?
Download our Comprehensive Design Guide to Great Roll Formed Parts to get started on your next roll form project.
(Editor's Note: This article was originally published in May 2018 and was recently updated.)
You May Also Like
These Related Stories
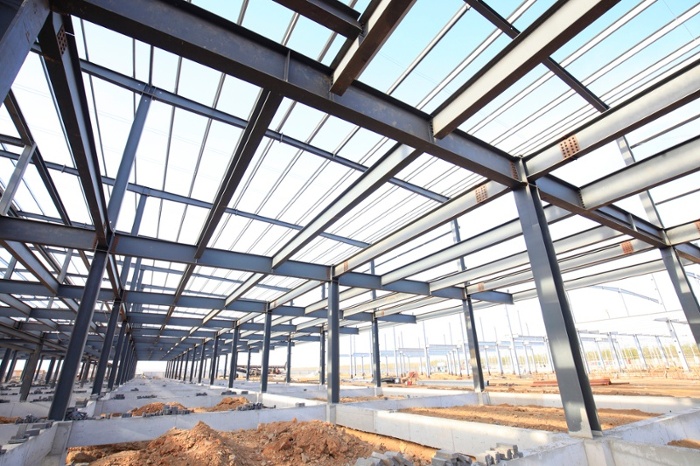
HSLA Steel Won't Break Your Back (Or Bank)
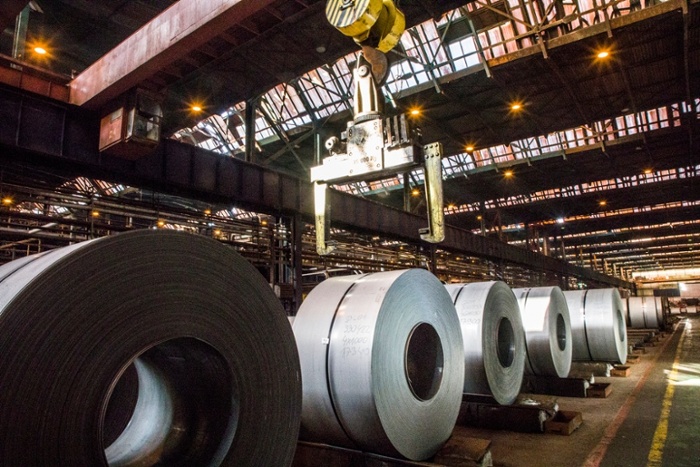
Commercial Roll Formed Products: A Guide to the Best Materials
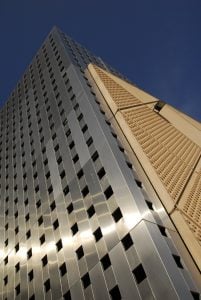