Best Metals for Exterior Architecture | Corrosion-Resistant Metals
The oceanfront is a beautiful but expensive place to live. And as it turns out, it’s also one of the most difficult places to use metal in outdoor architecture.
The salt and moisture of the seaside makes long-lasting construction a challenge. The majority of coastal buildings need maintenance every few decades or, depending on the metal used in their construction, they may need to be completely replaced.
And while most metals are resistant to corrosion, they are not immune. Those that are immune to corrosion are typically luxury metals that carry big price tags.
As you move further inland, all metals survive longer thanks to lower levels of salt in the environment. It won’t save them from the rain and weather, but they stand a better chance.
No matter where you build, your architecture will be exposed to wind, rain, and possibly salt and other elements.
Deciding on the best metals for exterior applications can be the difference between a long-lasting tribute to your skill and an ugly, costly failure. Here are some of the best metals for outdoor use.
The 4 Best, Most Corrosion-Resistant Metals for Exterior Architecture
So, which architectural metals are best for exterior architecture?
- Stainless steel -- steel with a chromium oxide layer that lets it shine
- Red metals (brass, copper, bronze) -- luxury metals for the fancy
- Aluminum -- common in outdoor fixtures and more
- Galvanized steel -- carbon steel coated in liquid zinc as added protection from corrosion
Now let’s compare these metals through the qualities that matter most to you: price, dependability, and beauty. Let’s start with the most common, yet least durable: galvanized steel.
4. Galvanized Steel
Galvanized steel is the least corrosion-resistant metal on this list. Galvanized steel is more about function than beauty, so it’s not your best choice if looks matter for your project. Despite that, it is most commonly used because it offers at least 50 years of strong, affordable performance (25 or more in saltwater environments).
Galvanized steel is carbon steel that is coated in liquid zinc. The zinc becomes the sacrificial anode and will corrode before the steel underneath, even if some of the steel is exposed (a phenomenon called preferential corrosion).
One benefit of galvanized steel is the ability to adjust the amount of protection by specifying the amount of zinc deposited on the surface of the steel during its production. The more zinc you put on, the better protection you will get!
Galvanized steel is by far the most affordable on this list, which is why it remains so widely used outdoors. Some of the most common galvanized items we produce are components used to mount solar panels to commercial building roofs.
So, galvanized steel is best for projects that only need short-term corrosion resistance, or architecture that requires planned, consistent renovations.
(Related post: Don't Get Salty About Coastal Construction - Use These Architectural Metals)
3. Aluminum
One step above galvanized steel is aluminum. Common outdoor aluminum products include light fixtures and door and window frames.
Does aluminum rust? Nope -- it creates its own protective coating through a process called self-passivation. As aluminum oxidizes, it creates a protective layer around itself like a snail drawing into its shell. Any paint on it will fade quite a bit.
Manufacturers can force this process via anodizing, which immediately strengthens the metal and leaves it with a polished finish.
Aluminum moulding trim for exterior use is most often shaped through extrusion, though we roll form plenty of it. It is often used on the exterior framing of storefront doors and windows.
Depending on who you talk to, aluminum will last anywhere from 10s to 100s of years before decomposing. (We lean toward the former.) Remember that aluminum outdoor products are designed to be sellable at an economical price -- in many cases they're simply not going to last a long time outdoors.
Aluminum is an effective option for exterior architectural components, but it's not the top choice on our list!
2. Copper, Brass, Bronze
These red metals are much more rare and luxurious than aluminum or stainless steel. They’re also incredibly durable; once they’ve oxidized, they’re completely immune to the elements. Brass and bronze are alloys of copper, so they all turn somewhat green with oxidation. Some designers are even adding patina to bronze, copper, and brass intentionally to get that stately look immediately!
Copper is a raw element, and the softest of these three metals. Zinc is added to copper to make brass, and tin with copper creates bronze. The addition of other metals makes brass and bronze harder, sturdier, and more resistant to oxidation. Some sources say copper trim can survive perfectly for over a thousand years.
These metals will be most desirable to architects who require a rich aesthetic.
Requests for red metals often come for luxury hotels, banks, historical buildings, and restorations. It is definitely a high-end material... pound for pound, it is easily double or triple the cost of stainless steel.
However, if you want your architecture to stand the test of time and make an impact, copper, brass, and bronze are all highly corrosion resistant, weather resistant, and durable. With these metals’ prices in mind, you’ll need to ask yourself: “Is my project worth the cost of the highest-quality materials?”
1. Stainless Steel
Most intents and purposes, copper, brass, and bronze are equivalent to stainless steel in durability. They're all incredibly resistant to the elements (how long has the Statue of Liberty been standing tall in the New York Harbor?), but they’re also very expensive. For that sole (and very important) reason, stainless steel comes in at the top of the list.
Does stainless steel rust? Yes, in extremely corrosive conditions, it can -- just at a far slower rate than carbon steel and aluminum. Still, stainless steel has the best balance of durability and cost-effectiveness for outdoor commercial and industrial purposes. Just make sure it's cleaned occasionally to keep it looking mirrorlike.
There are over 150 types of stainless steel, but there are only three that most common for exterior use: grades 304, 316, and 430. Each type of stainless steel has a different measure of alloy metals, affecting its durability and cost.
Grade 304 stainless steel is the most commonly used of the 300 series. Its alloy metals - 18% chromium and 8% nickel - give it extreme durability both physically and aesthetically.
However, it’s also one of the most expensive grades of stainless steel.
<Grade 316 stainless steel contains the same amount of chromium as 304, but with a higher percentage of nickel plus 2-3% molybdenum. Molybdenum increases the metal’s resistance to salt, making it perfect for the most corrosive environments. Typically, this is the metal used in marine applications.
430 stainless steel is typically used for mild exterior conditions, or indoors where the weather gets tracked in (in a metal door frame casing, for instance). Similarly, escalators in shopping malls use 430 stainless to protect against slush and salt carried in by shoppers. It has a lower percentage of chromium (17%) and a higher percentage of carbon (0.12%), which makes it the cheapest and most popular option.
However, it’s obviously not as effective as its 300-series counterparts for exterior use.
Stainless steel is much more affordable than copper, brass, or bronze. And, depending on how and where you use it, it can last well over a hundred years.
(Related post: Is Steel a Sustainable Material?)
Which is the best metal for your project?
As you can see, your choice of metal may largely hinge on how visible your project will be. A pipe buried underground doesn’t need to be pretty; a front door to a commercial building does. Your budget, desired appearance, and functional requirements will determine which material you need for your project.
If you need material for a rough-and-tumble application, you may need to spring for a high-end metal. Situations in which a highly durable metal is ideal include exposure to:
- Salt water or deicing salt
- Hot, humid areas with infrequent rainfall
- High pollution levels
Aluminum doesn’t hold up well around salt and will corrode over time, making it ill-equipped for coastal applications. On the other end of the spectrum, brass fixtures are great options for all environments.
If you are looking for more function than beauty, it may be appropriate to use one of the less expensive but highly durable galvanized steels.
If you need longer term protection or a brighter, more polished look, stainless steel may be your choice.
If your project is highly aesthetic or has a need for the rich red metal hue, one of the copper-based alloys may be the best material for you.
Depending on your project, there may be more factors in choosing your ideal metal.
For example, what about weight? Aluminum is lightweight and is easily transportable. Steel, meanwhile, is much heavier. If portability matters to you, then make sure you’re buying a lighter metal.
It’s easy to see why you must examine every angle before deciding on the best metals for exterior projects. Do your research, get the manufacturer involved, and make a well-informed decision that will have a long-lasting positive impact.
(Editor's Note: This article was originally published in January 2016 and was recently updated.)
You May Also Like
These Related Stories
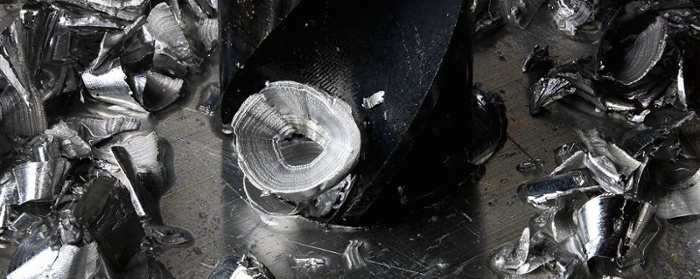
Choosing Your Aesthetic for Architectural Metal Mouldings
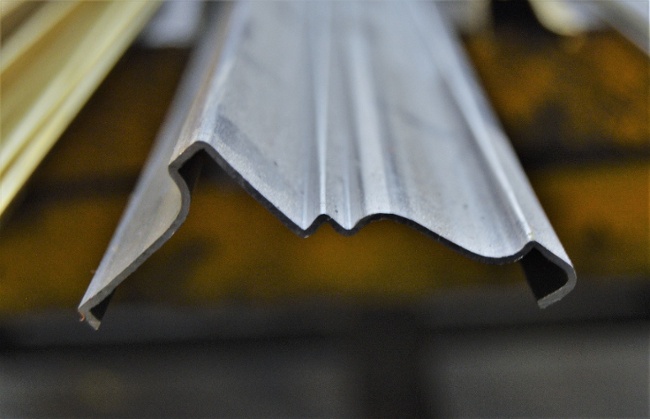
Metal Trim for Wood Adds Beauty to the Brawn
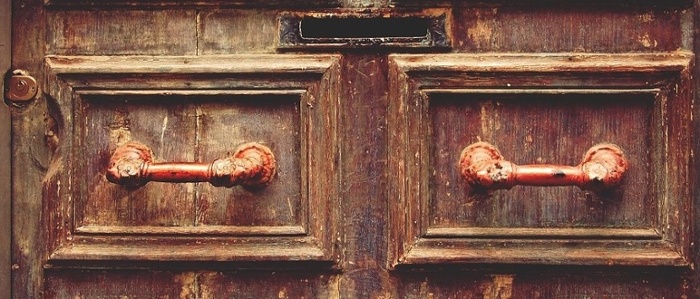