Need a metallic L-angle? Roll Forming vs. Angle Iron
You need long, slender, L-shaped metal components for your project.
Several metal forming processes can achieve the desired result, such as stamping, press braking, or extrusion. A comparison that isn’t talked about enough? The differences between metal roll forming and angle iron.
Any metal component design needs the right manufacturing process to achieve its potential. Factors to consider include adaptability to the application, material flexibility, production time frames, product durability, and cost-effectiveness.
Let’s compare the two metal forming processes and look at any advantages one may have over the other.
MAKING AN L-ANGLE WITH ANGLE IRON & COLD ROLL FORMING
Both roll forming and angle iron can easily create long, slender, L-shaped metal parts.
Hot-rolled steel is ideal for projects that demand larger L-shaped sizes and where precision or surface finish is not a priority. On the other hand, cold-rolled steel is more appropriate for tasks where accurate dimensional tolerances and polished surface finishes are required.
The most significant difference between roll-formed shapes and angle iron is the way each is created.
Angle iron is created by a hot rolling process. It starts as a billet of red hot steel and gets pushed into rough rollers to get it close to the angle size. It works through the rolls until it reaches the desired thickness. These machines run 24/7 and cut off at random 20+/- ft. lengths.
No holes or notches can be made in-line during hot forming. Customers also pay to saw-cut the specific lengths they need and any scrap waste and are sometimes required to accept larger bundled deliveries. Additional time may be necessary to perform secondary drilling or milling operations, increasing cost and production time.
Roll-formed steel angles, in comparison, are cold rolled. A piece of flat sheet metal is gradually bent into the desired profile by passing through a series of mated roll tool dies. Complex shapes may require 20+ passes through the roll forming line; simple geometries may only need a few.
Roll forming is an efficient process and economical for producing metal angles, channels, and complex shapes with multiple bends. In-line punching features include:
- Holes
- Notches
- Slots
- Embossing
These are easily accomplished in line, eliminating the need for secondary operations. Scrap waste is rarely over 2%.
ADVANTAGES OF ROLL FORMING METAL ANGLES VS. ANGLE IRON
Angle iron material is typically that of highly rust-prone A36 galvanized steel. The outside corners are usually square, with the tapered legs.
One example you may recognize: An angle iron frame is a right triangle, or 90°. This shape provides strong support and can bear a surprising amount of weight from the top or side.
Many structural engineers use reference tables like the U.S. standard for structural shapes. Angle iron companies match those standards for steel composition and exact sizing so structural engineers can use those tables to design load-bearing items. So, if you’re designing structural construction, this method skips the need to determine your load-bearing properties through calculation.
Roll-formed angle iron, in contrast, has a large radius on the outside and a sharp radius on the inside. Roll-formed steel angles will be more precise with exact lengths of legs as needed to fit your assembly and can be pre-punched with features as they are being produced. Required lengths can be easily cut to length in the quantities required with no scrap. However, if you are designing for load, you need to calculate load-bearing qualities yourself.
The L shaped metal angle, however, can be made out of different materials such as:
- Cold or hot rolled steel (galvanized or plain)
- Stainless steel
- Aluminum
- Copper
- Brass
- Bronze
Any of these materials can be specified for thickness.
COST OF L-ANGLE PRODUCTION: ANGLE IRON VS. ROLL FORMING
Typically, smaller quantities are more readily available for angle iron, as it’s typically stocked at steel service centers. However, there will be a break-even point where specifying the exact sheet metal angle, thickness, leg sizes, and pre-cut lengths required will make roll forming more cost-effective.
Don't forget the extra cutoff labor and scrap-waste costs of using angle iron – that alone may make roll forming a much better financial route.
(Resource: Wondering about other metal forming cost-saving methods? Click below to check out our guide!)
APPLICATIONS FOR L ANGLES MADE BY ROLL FORMING AND ANGLE IRON
Industries where angle iron is appropriate include:
- Construction including:
- Bridges
- Stairways
- Roof support framing
- Workboat structures
You might see it in everything from elevated tank supports and street sign structures to building columns and cell phone towers.
Industries where roll formed metal angles see the most applications include
- Automotive
- Locomotive
- Solar panel
- Custom, proprietary assemblies
You’ll also find roll-formed steel shapes in warehouse and distribution storage systems. Some enhancements to roll-formed metallic angle parts include hems to provide smooth edges, bends other than 90 degrees, stiffening ribs in the legs for greater sectional properties, and precise length tolerances for a perfect fit to mating parts.
The best way to determine when to use roll-formed steel shapes vs. angle iron is to consult a roll-forming supplier with in-depth experience, state-of-the-art technology, and superior production capabilities.
DECIDING BETWEEN ROLL FORMING AND ANGLE IRON FOR YOUR L-ANGLE COMPONENT
Now that you understand the differences between the two metal-forming processes, you can make an educated decision about whether to choose roll forming or angle iron for your next project.
If roll forming sounds right for you, check out our free e-book on designing great roll-formed parts. This guide addresses your design considerations specific to roll forming:
(Editor's note: This article was originally published in February 2022 and was recently updated.)
You May Also Like
These Related Stories
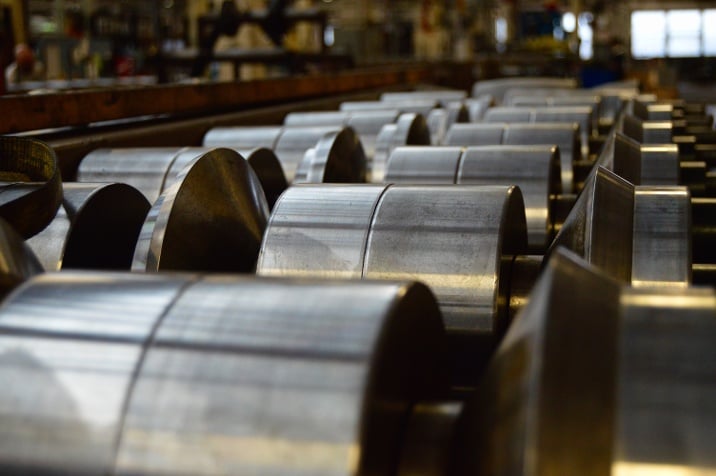
Metal Forming Processes: Industries & Applications
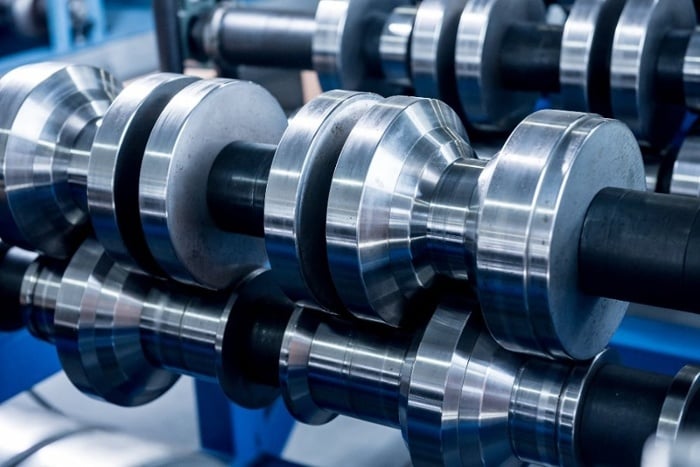
Custom Roll Forming Processes: Cold Roll Forming Steel
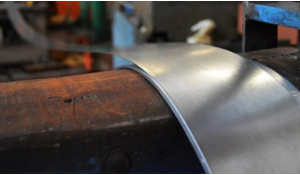