Metal Forming Processes: Industries & Applications
Metal forming processes play a crucial role in powering our society, driving innovation across industries. They enable the creation of a wide range of products and components, from heavy machinery and infrastructure to cutting-edge technologies like microprocessors and artificial intelligence.
But have you ever wondered how metal is shaped? In metal manufacturing, there are multiple processes to choose from. Each process holds its own set of advantages and disadvantages, making them suitable for specific applications and different types of metal.
Some of the most common types of metal forming techniques are:
- Roll forming
- Extrusion
- Press braking
- Stamping
- Forging
- Casting
Explore the diverse world of metal manufacturing processes and discover the optimal techniques for shaping metal to meet your unique needs.
1. Roll Forming
In short, roll forming involves continually feeding a long strip of metal through drum rollers to attain the desired cross-section. This process is highly efficient and cost-effective, making it the preferred choice for producing long lengths of sheet metal with consistent profiles. Additionally, roll forming can handle various metals such as steel, aluminum, copper, and more.
Roll forming services:
- Allow for advanced inline addition of punched features and embossing
- Are best suited for large volumes
- Yield complex profiles with intricate bending
- Have tight, repeatable tolerances
- Have flexible dimensions
- Create pieces that can be cut to any length
- Require little tool maintenance
- Are capable of forming high-strength metals
- Permit ownership of tooling hardware
- Reduce room for error
- Create less scrap
Common Industries & Applications of Roll Forming
Industries
|
Common Applications
|
2. Extrusion
Extrusion is a metal manufacturing process that forces metal through the die of the desired cross-section. It creates complex cross-sections and hollow parts with uniform wall thicknesses. Extrusion is a favored process for producing long lengths of metal with intricate cross-sectional profiles, and it's also highly efficient.
If you're thinking of pursuing extrusion metal forming, you should keep in mind that:
- Aluminum is primarily the extrusion of choice, though most other metals can be used
- Dies (aluminum) are relatively affordable
- Punching or embossing is done as a secondary operation
- It can produce hollow shapes without seam welding
- It can produce complex cross-sections
Common Industries & Applications of Extrusion
Industries
|
Common Applications
|
3. Press Braking
Press braking involves common sheet metal forming (usually), bending the metal workpiece to a predetermined angle by pinching it between a punch and a die. Press brakes are commonly used to bend metal sheets into V or U shapes for architectural, automotive, and other purposes.
If you're interested in press braking, be aware that it:
- Works best for shorter, smaller runs
- Produces shorter parts
- Is best suited for compatible shapes with more simple bend patterns
- Has a high associated labor cost
- Produces less residual stress than roll forming
Common Industries & Applications of Press Breaking
Industries
|
Common Applications
|
4. Stamping
Stamping involves placing a flat metal sheet (or coil) into a stamping press, where a tool and die apply pressure to form the metal into a new shape or cut out a piece of the metal. Stamping is ideal for producing high volumes of parts with consistent, intricate designs.
Stamping is associated with:
- Single-press stroke forming
- Consistent pieces with fixed dimensions
- Shorter parts
- Higher volumes
- Creating complex parts in a short amount of time
- Requiring high-tonnage presses
Common Industries & Applications of Stamping
Industries
|
Common Applications
|
5. Forging
Forging involves shaping metals using localized, compressive forces after heating the metal to a point where it's malleable. This process yields strong, durable parts that are resistant to wear and tear.
If you're considering forging, keep in mind that:
- Precision forging combines production and manufacturing by forming the raw material into the desired shape, with the lowest possible amount of secondary operations needed
- It requires little to no subsequent fabrications
- It requires high tonnage presses
- It yields a stronger end product
- It results in a product with high strength and hardness
Common Industries & Applications of Forging
Industries
|
Applications
|
6. Casting
Casting is a process that involves pouring liquid metal into a mold containing a hollow cavity of the desired shape. As the liquid cools and solidifies, it takes on the shape of the mold. Casting is ideal for complex shapes and designs with intricate details that would be difficult or expensive to produce through other metal forming processes.
Those considering utilizing a casting metal forming process should keep in mind that it:
- Can use a wide range of alloys & custom alloys
- Results in affordable short-run tooling
- Can result in products with high porosity
- Is best suited for smaller runs
- Can create complex parts
Common Industries & Applications of Casting
Industries
|
Common Applications
|
Choosing A Metal Forming Method
Are you looking for a metal former for your project? The type of metal manufacturing method you choose will depend on many factors:
- What metal are you using?
- What's your budget?
- What do you need to create?
- How will it be used?
By understanding the different metal manufacturing processes available and their applications, you can make informed decisions when choosing the most suitable technique for your specific project requirements.
Is Roll Forming Right for You?
If your metal shaping needs demand high volume, intricate profiles, and exceptional durability, roll forming is a powerful solution worth exploring. Its efficiency, precision, and flexibility can significantly enhance your production processes and deliver superior-quality products. With its ability to both optimize existing designs and unlock innovative possibilities, roll forming is a valuable tool for any manufacturer looking to stay ahead in today's competitive landscape.
Find out why so many industries choose roll forming and if the process fits your needs. Check out our free guide:
(Editor's Note: This article was originally published in January 2017 and was recently updated.)
You May Also Like
These Related Stories
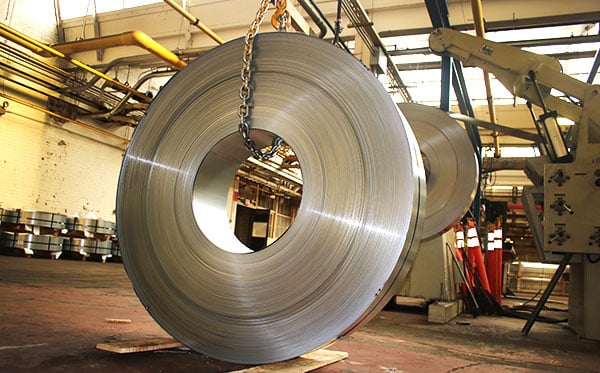
What Is a Roll Forming Machine? Roll Forming vs. In-House Forming
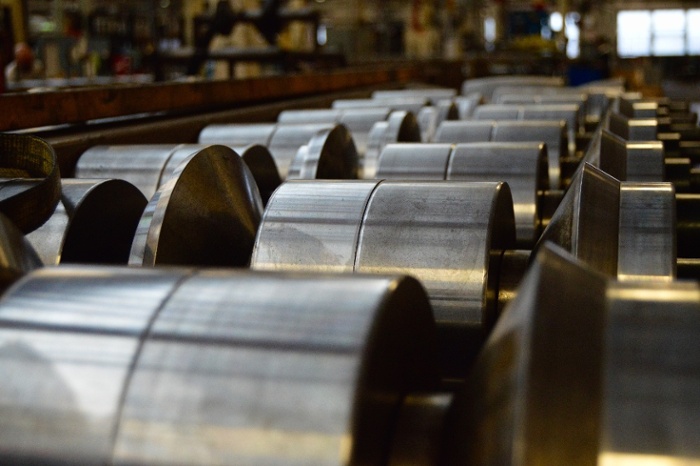
The 4 Most Common Myths of Roll Forming Metal
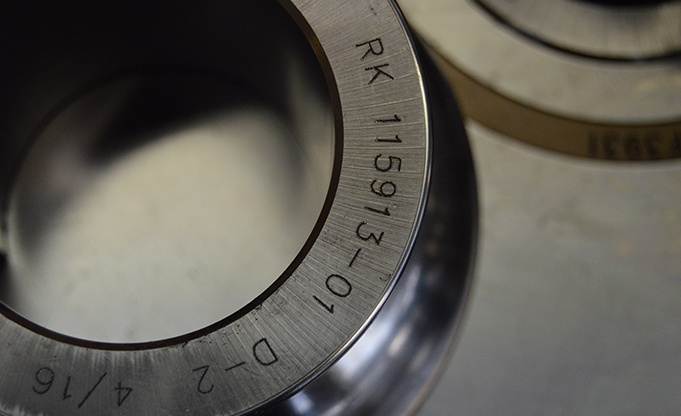