Roll Forming Sheet Metal: Precision Roll Forming Machines & Dies
Ever wonder how the sleek, sturdy metal parts that power everything from cars to skyscrapers come to life? It all starts with something as simple as a flat sheet of metal. But turning that into a complex, precise component?
That’s where the magic of roll forming sheet metal comes in.
Curious how it happens?
Let’s examine the six key pieces that make up a roll-forming line. By understanding how these components work together, you'll appreciate the craftsmanship behind your parts and gain the insights needed to design with confidence and precision.
From Sheets to Shapes: Roll Forming Sheet Metal Simplified
Roll forming is a continuous shaping process where a long sheet metal strip passes through a series of rollers, each gradually bending the metal closer to its final form. It's the go-to method for producing high volumes of uniform, precision-engineered metal parts.
Roll forming stands out because it can handle even the most intricate profiles, creating shapes that would be nearly impossible to achieve with traditional techniques.
This process is efficient and incredibly precise due to the seamless flow of material that reduces waste and boosts production speed. The roller dies are finely tuned to ensure every piece meets strict tolerances, making it perfect for applications where accuracy can't be compromised.
Whether you're crafting structural components, sleek trim, or detailed assemblies, roll forming offers reliable, high-quality results that consistently meet the highest industry standards.
The 6 Stages of Roll Forming Sheet Metal
Understanding the components of a roll forming line is essential for grasping how roll forming sheet metal works in the metal fabrication process. Each part plays a huge role, from preparing the metal coils to the final cut and optional secondary operations.
These six stages involve:
- Front-end equipment
- Strip accumulators and slack loops
- Pre-punch presses
- The roll die mill
- Cutoff and discharge
- Secondary operations
1. Front-End Equipment
The roll forming process begins with front-end equipment designed to prepare the metal coils for bending. As the coils have been tightly wound for some time, minor correction is needed to remove the coil set. Coil set is the tendency of the metal to stay coiled, plus a bit of material distortion.
Coil Loading
A floor or pit-mounted coil car loads metal coils onto the uncoiling device. This equipment safely positions the heavy coils for processing.
Coil Flattening
The coil is fed through a flattener to remove the coil set. A coil set refers to the tendency of the metal to retain its coiled shape, causing material distortion.
Lead End Trimming
The lead end is trimmed and joined to the trailing end of the previous coil, ensuring a continuous feed for uninterrupted production.
2. Strip Accumulators and Slack Loops
Strip accumulators and slack loops are vital for maintaining efficiency in the roll forming process.
They temporarily store sections of metal strips, allowing the roll form mill to run continuously even if the line stops for pre-punch presses or other operations.
Timing is crucial. The accumulators feed the next metal segment at precisely the right moment to maintain a smooth operation.
These components are especially useful in high-speed operations, where frequent stopping and starting could otherwise lead to significant efficiency losses.
3. Pre-Punch Presses
Before the metal is fed through the roll forming line, it may pass through one or more in-line punch presses. Digital controls and accurate coil feed systems enable punching holes, notches, and slots in consistent patterns.
This step can eliminate the need for secondary fabrication operations, streamlining the production cycle. Depending on the project specifications, this may add minimal time to the production cycle but can significantly increase overall efficiency.
4. The Roll Die Mill
The magic happens in the roll die mill, transforming flat metal into intricate shapes.
A typical roll die mill comprises 10-24 pairs of roller die stands, each progressively shaping the metal strip.
The mill is either individually or gang-driven, pulling the metal ribbon through the rollers to form the final shape.
The flower pattern below illustrates the forming process of one particular series of rollers:
Once formed, the metal part runs through straightening dies and side rollers to eliminate any remaining distortions, such as twists or bows. This step is necessary, as these distortions can quickly ruin a good part.
5. Cutoff & Discharge
Once the metal has been shaped, it must be cut to the desired length and discharged from the roll forming line.
A flying cutoff press cuts the part to length without stopping the roll forming process, ensuring precision and efficiency.
Accelerating the cut-off die to match the roll forming mill's speed achieves very accurate cuts. The finished part is discharged onto a run-out table and typically placed in protective crating for storage or shipment.
6. Secondary Operations
Even after the primary roll forming process, additional steps may be required to complete the part. In the case of certain roll form suppliers, certain secondary operations could be free, if the cycle time to perform them is equal to or less than the time it takes for the next formed part to exit the line.
Additional Punching
Secondary operations can include further punching or notching to meet specific design requirements.
Tight-Tolerance Forming
Some parts may require tight-tolerance forming or end straightening to ensure they meet exact specifications.
Assembly and Kitting
Minor assembly of mating parts or kitting shipments with other components may also be made directly on the roll forming line.
Minor Assembly of Mating Parts
These additional steps help create a finished product that meets all required specifications and standards.
Benefits of Roll Forming Sheet Metal
Roll forming sheet metal provides many advantages over other standard manufacturing sheet metal processes. These six benefits include:
Consistency
One of the standout benefits of roll forming sheet metal is its ability to maintain uniform dimensions and quality across large runs. Each piece produced is highly consistent, ensuring that the final product meets exact specifications without variation.
Efficiency
The roll forming is designed for high-speed production, making it ideal for mass manufacturing. It allows for continuous operation, significantly reducing downtime and minimizing material waste, translating into faster output.
Versatility
Roll forming is not a one-size-fits-all approach. It can handle various metal types, from steel to aluminum, and accommodates different thicknesses, making it adaptable to various industries and project needs.
Cost-effective Production
Roll forming reduces production costs by optimizing material use and reducing waste. The continuous process minimizes scrap, making it a more economical choice for large-scale production.
Precision and Accuracy
The process ensures tight tolerances and exceptional accuracy thanks to the carefully designed roller dies. This precision is especially crucial for industries that rely on highly consistent parts for performance and safety.
Customization
Roll forming isn’t limited to standard shapes. It allows for creating complex and customized profiles, offering flexibility in shapes, sizes, and cross-sectional designs to meet specific project requirements.
Shaping Your Understanding: FAQs About Roll Forming Sheet MetalWhy is roll forming more efficient than other metal fabrication methods? The continuous process of roll forming minimizes downtime, reduces waste, and allows for high-speed production, making it ideal for mass manufacturing. Additionally, features like strip accumulators and in-line punching streamline operations further. What are the secondary operations that can follow roll forming? Secondary operations can include additional punching, tight-tolerance forming, assembly, and kitting. These steps ensure the finished product meets all specifications and can reduce the need for separate post-production processes. What materials can be used in roll forming? Roll forming is compatible with various metals, including steel, aluminum, and more. It also accommodates different thicknesses, making it adaptable for various industries and applications. |
Elevating Your Expertise in Roll Forming Sheet Metal Production
From prepping metal coils to managing slack and executing the cutoff process, you've now gained a clearer view of the intricate steps of roll forming sheet metal.
What may seem like magic is, in fact, a precise and well-coordinated series of actions that transform raw material into consistent, high-quality components.
This process showcases the blend of engineering expertise and efficiency that powers modern manufacturing, delivering the reliable parts that industries depend on.
Roll Into Action: Where to Go from Here
(Editor's note: This article was originally published in January 2016 and was recently updated.)
You May Also Like
These Related Stories
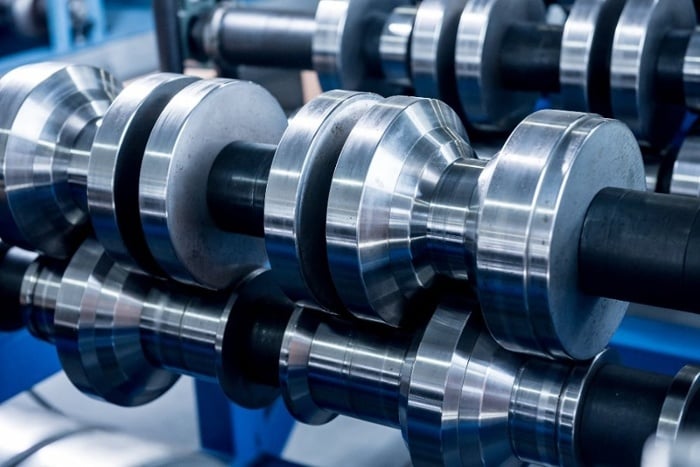
Custom Roll Forming Processes: Cold Roll Forming Steel
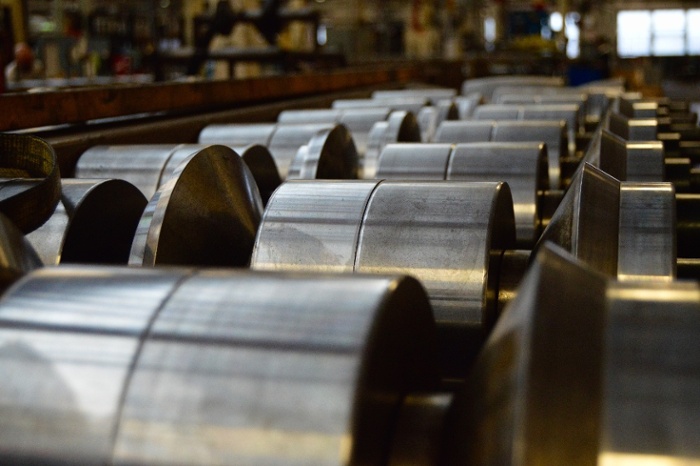
The 4 Most Common Myths of Roll Forming Metal
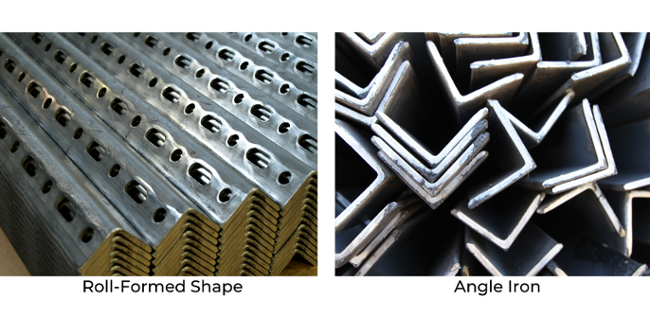