Sheet Metal Parts: What Can & Can't Be Roll Formed?
Navigating the world of sheet metal parts while sticking to a budget can feel like a puzzle.
But here’s where roll forming steps in as a cost-efficient game changer.
Primarily for parts with intricate bends and sharp angles.
While roll forming works wonders for many materials, not all are a perfect fit for the process. As you explore alternatives to standard sheet metal parts, it’s important to remember the various production steps, like rolling, coating, and slitting, that shape your final product.
Before making material choices, your roll-forming partner can offer expert advice, helping you choose the right material or a different forming method to make your project successful.
Good & Bad Materials For Roll Forming Sheet Metal Parts
You may wonder, “Is my specified material OK for roll forming?”
If your project needs roll-forming metal sheet parts, many options exist.
While mild steel may be the most common raw material for roll forming, any ductile metal can be used for this process. Traditional materials include:
- Galvanized and galvannealed steel
- Stainless steel
- Aluminum
- Copper
- Brass
- Bronze
If you're looking to lower your spending, prepainted sheet metal is also a material choice.
Reduce Costs With Prepainted Sheet Metal
Many sheet metal fabrication parts are painted or powder coated after they are shaped to protect the part or for aesthetics. However, you could save some money using prepainted or pre-coated metal. Having the metal painted or coated in advance means you won’t need a particular painting or coating session for your parts. The roll forming is gentle enough not to damage the paint or coating.
Factors to consider before choosing your sheet metal parts material
To judge a metal or other material for roll forming, it is important to understand the roll forming process and the material's properties. Metal roll forming companies consider various factors before making a final decision, including the following:
- Thickness
- Mechanical properties
- Surface quality
- Uniform flatness tolerances
- End-use requirements
Your Roll Forming Questions Rolled OutWhich materials are ideal for roll forming? Ductile metals such as mild steel, galvanized steel, stainless steel, aluminum, copper, brass, and bronze are commonly used for roll forming due to their flexibility and malleability. Materials that are brittle or lack ductility, such as cast or heat-treated metals like aluminum 6061-T6, should be avoided because they are prone to cracking during the process. Is it cost-effective to use prepainted or pre-coated sheet metal? Yes, prepainted or pre-coated metal can save time and costs by eliminating the need for post-forming finishing processes. However, remember that unpainted edges or holes will reveal the material's original color. |
Why metal is the best choice for roll forming
Since metal is a durable material that can hold up to the roll forming process, it's a good fit. However, some materials aren't such a great choice when roll forming, such as:
Foam Rubber
Foam rubber, known for its flexibility, is often explored due to its lightweight nature.
However, foam rubber struggles to maintain its dimensional stability despite its flexibility after the roll-forming process. Its tendency to rebound to its original shape makes it impractical for applications requiring precision and durability.
Plastic (Polymer)
Plastics, or polymers, present a different scenario. Although they possess a malleability that makes them suitable for roll forming, the inherent risk of fracture or deformation limits their use in this process.
Specifically, polymers are more prone to strain and stress-induced damage during rolling, leading to higher rejection rates.
Consequently, these materials are more efficiently handled through extrusion techniques that accommodate their structural characteristics.
Cardboard
Cardboard offers a unique challenge in non-metal roll forming. Its fibrous composition allows for certain degrees of bending, making it occasionally viable for roll forming when applied in specific contexts.
However, urgent attention must be given to the specification of material thickness.
Your Path to Roll Forming Success
Successfully navigating the roll-forming process for sheet metal fabrication parts comes down to understanding material limitations and process intricacies.
Many factors influence the final product, from selecting the right metals to exploring pre-painted options.
Ready to Move On? Let’s Roll into the Next Step!
By partnering with a roll-forming expert, you can ensure the best material choice, avoid potential pitfalls, and deliver high-quality results while staying within your budget.
Let us know if you are currently facing challenges in choosing the right material or making design decisions related to converting to roll forming. We are here to help you fully use roll forming's cost-effectiveness and repeatability advantages.
(Editor's note: This article was originally published in August 2018 and was recently updated.)
You May Also Like
These Related Stories
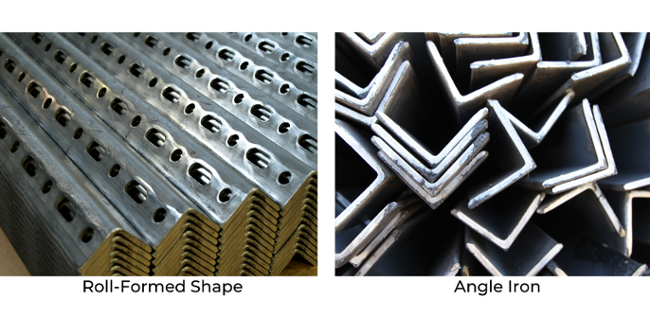
Need a metallic L-angle? Roll Forming vs. Angle Iron
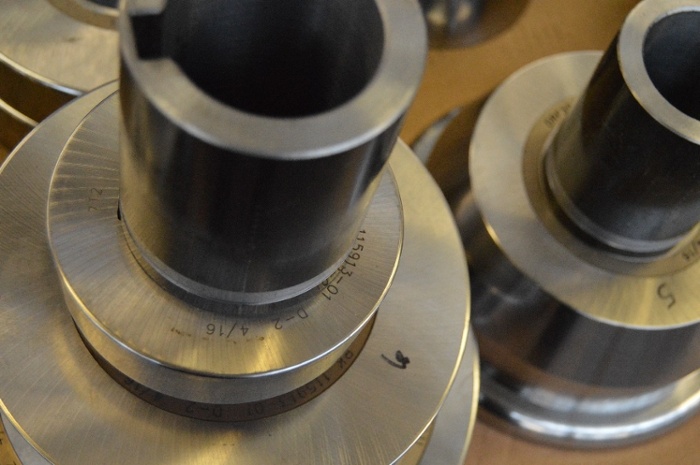
Roll Forming Tooling Design: Build In-House or Outsource?
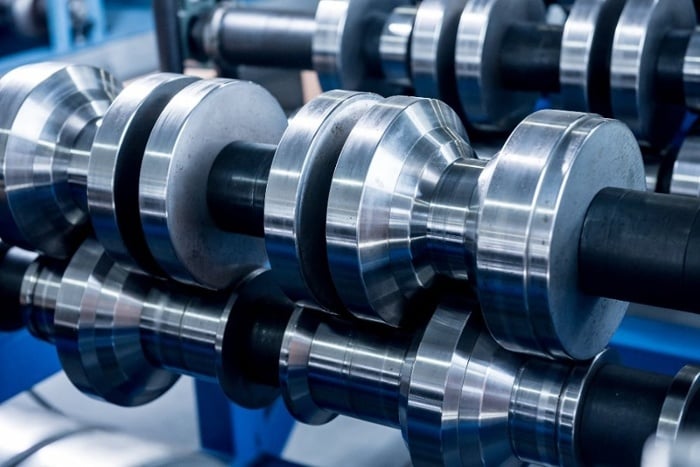