Using Total Quality Management in Manufacturing for Long-Term Success
Today, customers expect high-quality products and services more than ever. But how can businesses ensure consistent quality across all aspects of their operations?
Enter total quality management (TQM).
TQM, or total quality management, exists alongside lean manufacturing concepts to improve the long-term success of businesses.
What Is Total Quality Management?
Total Quality Management is a comprehensive management approach focused on improving the quality of a company’s outputs – whether ideas, products, services, or assemblies – to enhance overall performance and customer satisfaction. TQM principles can vary across industries and organizations, but they all emphasize the importance of creating a culture of continuous improvement.
This philosophy ensures that quality is embedded in every process, leading to better efficiency, innovation, and long-term success.
What are the Four Pillars of Total Quality Management?
The foundation of TQM is built upon four core principles that guide organizations to create a culture where quality is prioritized. The four pillars of total quality management include:
- Customer focus – understanding and prioritizing customer needs and satisfaction.
- Continuous improvement – committing to ongoing improvement and adapting to change.
- Employee involvement – recognizing that every employee – no matter their position – plays a role in maintaining and improving quality.
- Process-centered approach – emphasizing the importance of effective processes in achieving consistent quality.
How Does TQM Work?
In the case of Dahlstrom Roll Form, total quality management means continuous improvement through constant data analysis.
How does it work?
To start, we gather every bit of performance data we can find, comb through it to identify the quality pieces of information and analyze it for opportunities to improve. Once we lock in improvement opportunities, we build a plan to implement changes and track those changes to make sure they’re benefitting us and our customers.
The question we ask throughout this process is “Did we obtain the results we wanted to achieve?” If not, we head back to the drawing board. As this process moves along, we continue to gather data and analyze areas for improvement.
The Benefits of Total Quality Management
Total quality management offers several advantages that can transform a company’s performance and culture.
By creating a culture of continuous improvement and emphasizing customer satisfaction, TQM delivers both tangible and intangible benefits that contribute to long-term success.
Here are 8 benefits of implementing TQM in an organization:
- Enhanced product quality
- Increased customer satisfaction
- Better employee engagement
- Improved overall efficiency
- Stronger team collaboration
- Higher profitability
- Greater flexibility and innovation
- Sustainability and waste reduction
Setting Your Business Up for Long-Term Success with TQM
At Dahlstrom specifically, we’ve noticed all of these benefits. Continuous Improvement is part of our daily work presence. 93% of our employees directly contribute to continuous improvement initiatives on which we take action every year. We expect to see even more benefits as we continue to implement positive changes based on hard data analysis and customer feedback.
Editor's note: This article was originally published in January 2016, and has recently been updated.
You May Also Like
These Related Stories
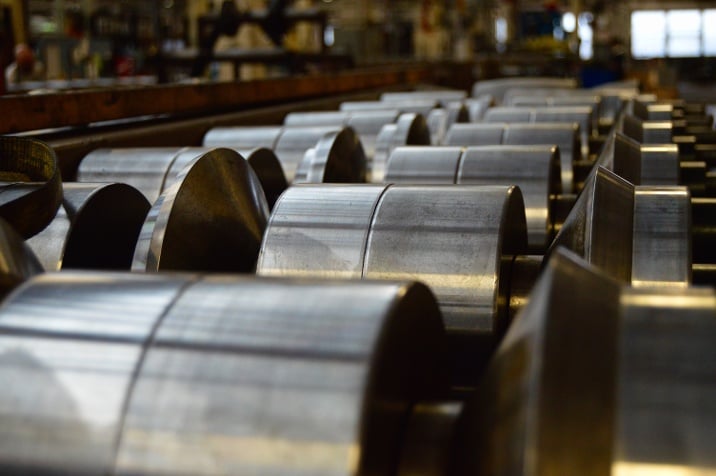
Why ISO Manufacturing Standards Matter in Roll Forming
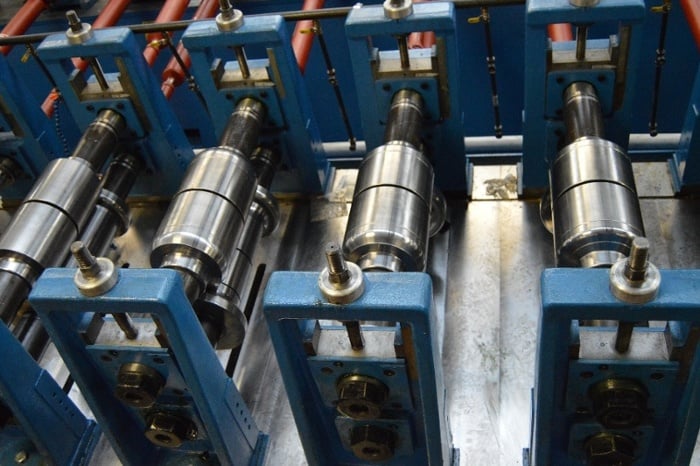
How Roll Forming Limits Your Total Manufacturing Cost of Ownership
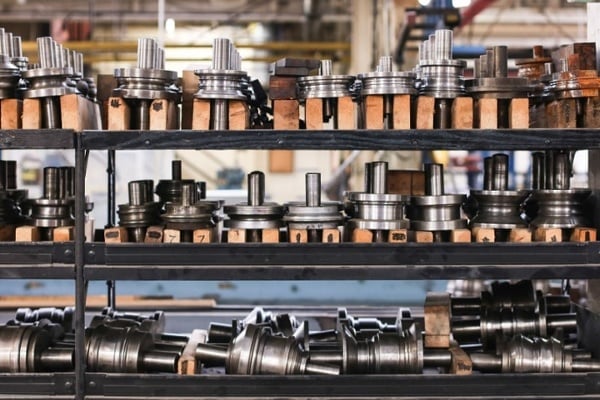