4 Steps to Controlling Roll Forming Costs
Control your roll forming costs without sacrificing parts’ quality with these four steps to efficiency:
|
Roll forming can be the most affordable metal forming means available. But, as with any industry, shoddy processes can end in high roll forming costs -- which get passed on to you.
Fortunately, there are ways to create efficiencies without sacrificing quality. Let’s take a look at the most effective means to improve your processes with your roll forming manufacturer and get your costs under control.
Steps to Controlling Roll Forming Costs
While there are design factors that affect roll forming costs, such as setup time, run speed, and materials, other aspects to take into account include:
1. Roll Former Speed and Efficiency
A productive and cheaper-to-operate roll forming system will result in a lower conversion cost than other metal forming methods.
Facility organization is a major factor in setup and run speeds -- for example, if you’re working with a supplier with consistent methods and an organized working space, retrieving roll dies is simple and repeatable for time consistency.
However, if the plant is cluttered and the workers regularly have trouble finding things they need, time will certainly be wasted. This is especially crucial if you’re ordering complex parts for which setup takes several hours and which use special fixturing.
Another obstacle? Loading the roll dies into the machine. The speed of this process varies based on the number of people used, the mechanical lifting and placing equipment, and the method of tagging each roll die for proper sequence of insertion.
Choosing an experienced partner that eliminates downtime will result in less costly parts and allows you to get your product shipped sooner.
2. Tooling and Materials
You’re probably aware that raw material makes up the bulk of roll formed part cost.
The share of part cost that raw material contributes depends on:
- The amount of metal in the part vs. the process cost
- Type/thickness
- Scrap produced in the process
- Metal market conditions
An average roll formed part is comprised of 50% to 70% raw material cost. If the material is heavy and expensive (thicker bronze and stainless steel, for example), material costs can rise to as much as 85% of the total price.
Ask yourself this: “How expensive or elegant does my metal need to be to achieve the outcome I desire?” For example, it’s pointless to pay for a beautiful stainless steel surface finish that’ll be stuffed underground for public utility infrastructure.
As for the tooling you’ll use to shape that metal, it may cost less if your manufacturer participates in part design and optimizes it for roll forming processes. Even better: Your provider may already have tooling that will work for your project, keeping you from incurring any tooling costs.
3. Keeping It Simple
“Everything should be made as simple as possible, but not simpler.” – Albert Einstein
Keeping things simple helps save time, reduce waste, and mitigate mistakes.
A complex custom roll formed part will require additional setup time. That’s because the complexity of the shapes you’re producing relates directly to the number of roll tools that need to be loaded on the machine. Average designs require 12 to 16 forming passes through roll formers, but the most complex shapes can require 50-plus passes.
Correctly specified tolerances (those that match the true function of the part) can also make an order cheaper to produce. Sometimes tight tolerances are overrated, and not necessary.
Through proper part design and an appropriately matched number of forming passes, a quality roll form supplier will make sure things don’t get overly complicated with excessive dimensional checking and end flare.
Getting it right the first time will keep you from needing costly tooling modifications or seeing rejected parts down the line.
In summary: The simpler the design and the better tolerances are “co-defined” with your supplier, the better you’ll feel about your bank account.
4. Inventory Management
The most cost-effective and dependable style of inventory management is Kanban-based trigger-response. You give the trigger information directly from the point of use, and your provider responds via a robust replenishment system.
This supply planning management style works for both raw materials on the manufacturer’s production floor and your own finished products. Because once a replenishment signal triggers, you automatically get refilled to a pre-agreed level and you avoid wasting money managing orders and delivery dates, and stocking up needlessly.
An efficient manufacturer will also refrain from hoarding inventory when buying raw materials for clients. The pipeline of supply here should be managed the same as above, yet also able to quickly change gears if a client no longer requires a certain product. (Constant communication is key.)
While you may be worrying about order size, volumes as low as 10,000 linear feet per year can still be cost-effective with roll forming, depending on your part design. Your provider might offer a discount on your smaller orders in exchange for a longer contract that includes Kanban replenishment where both sides are protected with a supply agreement.
Always communicate your long term needs so the supply chain management program is clear. Repeating small orders are not small over time!
Benefit from a Streamlined Process
You’ve probably figured out that process improvement on the manufacturer’s part goes a long way toward controlling roll forming cost. In addition to common-sense organization and design simplicity, set high expectations on setup/run times and inventory management to ensure the most cost effective results possible.
Learn more about cutting your roll forming costs
Check out our Comprehensive Guide to Metal Roll Forming Costs below:
(Editor's note: This article was originally published in July 2017 and was recently updated.)
You May Also Like
These Related Stories
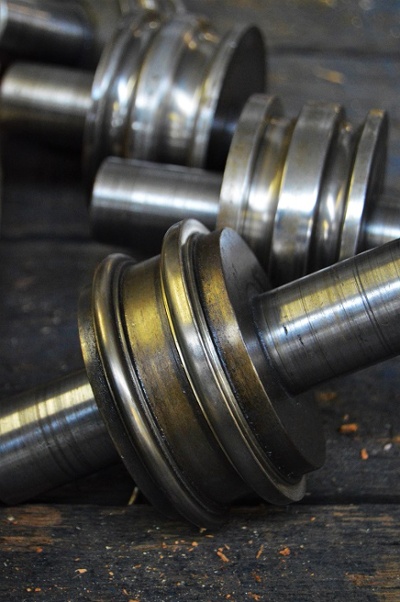
Sheet Metal Roll Forming: Assessing Cost, Ability, & Quality
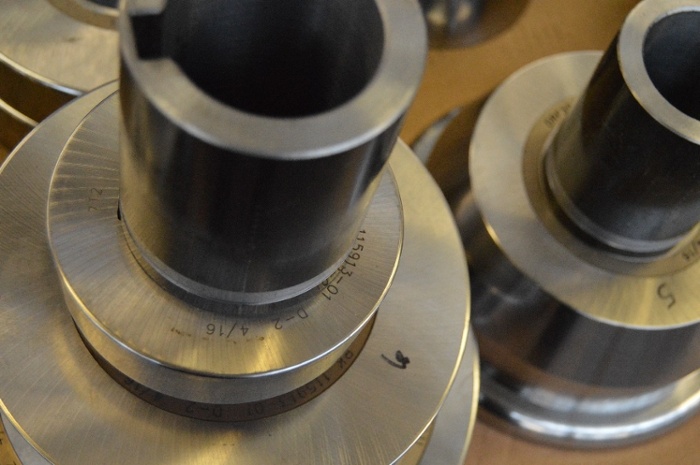
Roll Forming Tooling Design: Build In-House or Outsource?
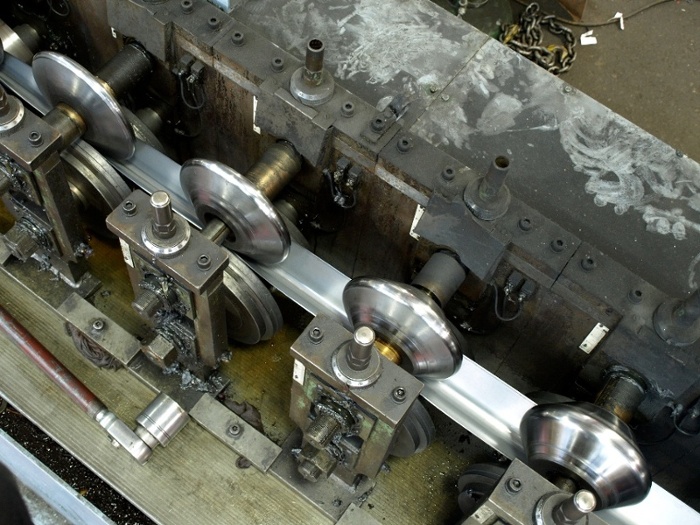