Sheet Metal Roll Forming: Assessing Cost, Ability, & Quality
Sheet metal roll forming is one of the most affordable metal fabrication processes.
The ability to manufacture large quantities of simple and complex quality parts makes roll forming a favorite in several industries, including power distribution, commercial refrigeration, warehouse and data storage, and more.
Here’s why cold roll forming is worth your investment:
SHEET METAL ROLL FORMING EXPLAINED
Roll forming is a metalworking process that uses contoured tools to bend flat sheets from coiled steel into a finished and uniform profile.
Engineers and architects request roll forming when they require a bend — sometimes multiple bends — of a metal channel, angle, or complex shape.
Manufacturers can roll form before, during, or after other fabricating steps. The process is repeatable over long runs.
Watch the Roll Forming Process in Action
Watch Rob White, president and CEO of Dahlstrom Roll Forming, explain the process from coil to crate in the video below:
While a few metal forming processes can create a slender, linear metal part in medium to high volume, we’re partial to sheet metal roll forming.
For us, it comes down to:
- Cost: In-line fabrication and high-volume ordering make roll forming cost-effective
- Capabilities: Roll forming can turn various metals into complex shapes
- Quality: Roll forming produces consistent shapes with an attractive finish
Let’s explore these in more detail:
1. Cost
Tooling for roll forming can get expensive, but long-term use will eventually net cheaper labor costs per piece. Furthermore, strategic metal purchasing eliminates the argument that "roll forming tools are too expensive." Whether a part has 1 simple bend or 12 complicated bends, future processing labor cost per part is the same.
Overcoming tooling costs opens opportunities for:
- Higher-volume orders (better cost efficiency)
- Larger runs (see above!)
- Expanded in-line fabrication (lowering labor costs)
A roll forming crew feeds material via large coils of metal, reducing material handling and scrap costs. Line feeding is reduced to once per large coil and since the slit width of the coil is precisely the width of the formed part, scrap is basically eliminated.
The upfront cost of roll forming can vary significantly based on the factors mentioned. Generally, using simpler shapes, thinner materials, and higher production volumes will result in lower costs. Your roll forming partner can provide a more accurate estimate.
Meanwhile, certain other manufacturing processes (say, press braking) require separate processes for raw material feeding, punching, and bending, adding labor, and other indirect costs.
Streamline Your Roll Forming Costs
Working with an experienced supplier, you’ll learn how to cut costs without sacrificing quality. To learn more about metal roll forming costs, grab our free book:
2. Capabilities
The flexible roll forming process allows you to create any shape, no matter how complex the desired cross-section profile is. (The ideal use is for long, slender shapes.)
Roll forming might not be ideal for shapes with razor-sharp 90-degree bends, as these could prematurely wear the tools and may even sever the material. Additionally, metals thicker than ¼” might not be feasible because of the forming pressure required. Your roll forming partner can help you understand specific limitations.
Designing Parts for Sheet Metal Roll Forming
Need help designing metal components for your project? Our design guide can get you started on making quality roll formed parts. Click the button below to learn more:
Because the material is fed by a continuous coil, there are no limits on length. Roll forming also allows the shaping of already painted, plated, or coated metal due to the smooth bending transitions.
Material-based limits to roll forming are also nearly nonexistent, unlike extrusion. The process works with:
- Aluminum
- Carbon steel
- Copper
- Bronze
- Brass
- Perforated metal
- Prepainted coil steel
- Even some non-metal materials!
That wide variety of materials can turn into specially shaped roll formed parts, including:
- Graceful curves and bends
- Closed shapes (tubing)
- Multiple angles and radii
Custom roll forming also allows for the in-line secondary operations such as:
- Holes
- Notches
- Embossments
- Slots
- Stamp or ink-jet marking
Roll forming is typically faster and offers quicker turnaround times when compared to other metalworking processes like extrusion or press braking, especially for high-volume orders. This efficiency stems from the continuous nature of the roll forming process and its capability for in-line fabrication, which integrates multiple manufacturing steps into one continuous operation.
3. Quality
One of the more striking advantages of roll forming services is they produce more consistently uniform parts across runs.
Roll forming machines adeptly and accurately shape high-strength steels, while managing springback effectively. Even extremely tight tolerances are no match for roll forming.
Whereas other metal forming processes are rough on metal surfaces, roll forming creates an attractive finish. This is great for aesthetic projects where tool marks from other metal-forming processes are not an option.
Often, using the pre-finished metal coils during roll forming can be more cost-effective due to reduced handling and processing steps. However, it's important to compare the protective properties of pre-forming finishes vs. post-forming options (powder coating, e-coating, plating, etc.). For example, a pre-painted coil that has been slit to width has the slit edges uncoated. However, even though the edges are uncoated, a galvanized base metal may provide the anodic protection necessary.
INDUSTRIES THAT BENEFIT FROM SHEET METAL ROLL FORMING
Roll forming serves several industries by producing large volumes of consistent, complex shapes. From simple shapes to intricate designs, metal roll forming delivers exceptional value. Roll forming can be a budget-friendly solution for a wide range of component needs.
Some of the industries Dahlstrom Roll Form serves include:
- HVAC/ Commercial Refrigeration
- Power Distribution
- Warehouse Storage and Conveyer Systems
- Data Storage
- Commercial Trailer
- Elevator/Escalator
- Solar Panel Racking
Roll with the Right Manufacturer
Roll forming is almost always the answer for medium-to-high-volume projects. A great sheet metal roll forming company will also aid in part design and may be able to cut tooling costs by optimizing the part for roll forming.
A comprehensive partnership with a good roll forming company can offer you value throughout your project. From design consultation to finished goods inventory management for immediate shipment, your roll forming partner should look for ways to cut your costs and lead times.
Contact us today to see how sheet metal roll forming can benefit you today!
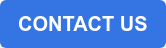
(Editor's note: This article was originally published in September 2017 and was recently updated.)
You May Also Like
These Related Stories
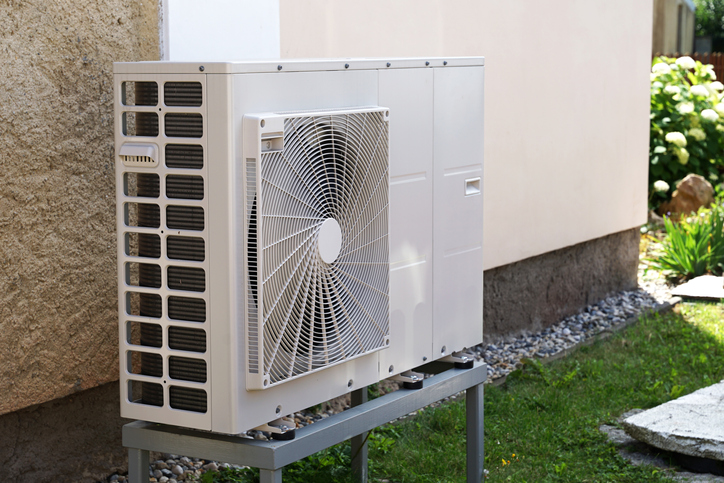
High-Quality Heat Pump Parts: Try Metal Roll Forming
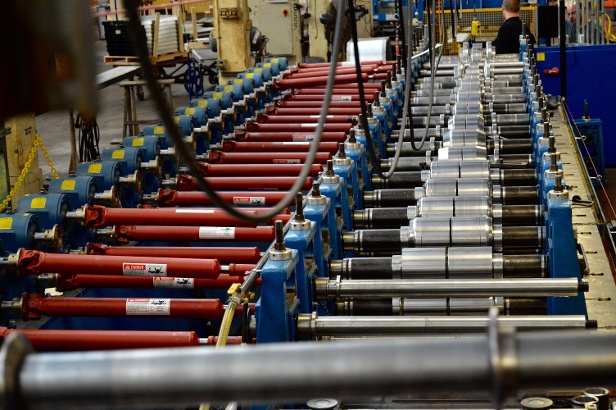
A Metal Roll Forming Partner Mustn't Be Big to Boost Your Business
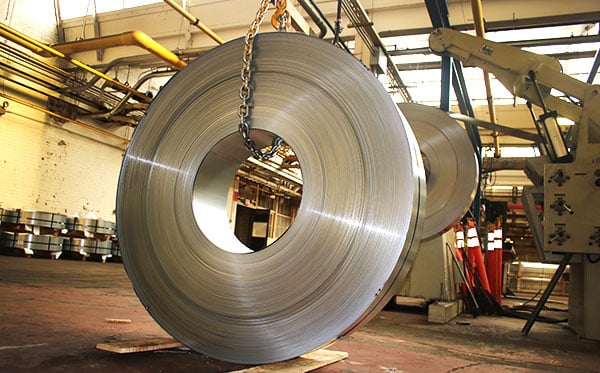