Sheet Metal Design Guide: End Distortion & Springback
Roll forming is the most cost-effective way to continuously produce complex shapes with multiple bends. But it’s not a perfect system. Engineers must understand and accept two particular quirks of roll forming before committing to the process: end flare and springback.
End flare, or end distortion, is unique to roll forming manufacturing, while springback is a more universal sheet metal bending issue.
So, what are these two roll forming anomalies? How will they affect your components? And how do we minimize them?
The following roll forming design guide will address each question and describe how these defects can be prevented or corrected during fabrication:
Roll Forming Design Guide for End Flare
End flare is a distortion that occurs at the ends of a roll formed section, or at any point where the section is cut. This includes large knockouts or notches and tabs in the middle of the part.
The strain that roll forming puts on a metal workpiece is much more complex than with other bending methods. Residual stresses tend to be particularly apparent — they cause greater distortion at the ends of your components than at any other point.
Stop Roll Forming Defects Before They StartEnd flare and springback are pretty much always present in roll forming. It’s all about how your roll forming partner deals with them. Once you know the rules of both issues, you can have your design 100% correct before your roll former even sees it! |
How to Smooth out Your End Flare Issues
Flare can be minimized by roll design procedures. However, it can’t be completely eliminated except by subjecting the metal to stretch forming or to a stress-relieving anneal.
In most cases, this is done by stretch forming, which involves laterally moving the material to stretch and compress the metal. First, your roll former overforms the section, then underforms it, and finally finishes it.
Meanwhile, annealing is the treatment of a metal by heating it and then cooling it to room temperature. This process improves ductility and reduces brittleness. Most importantly, it relieves stresses absorbed by the metal during roll forming.
Your designer and manufacturing partner should always consider end flare when designing roll formed products and tooling!
Roll Forming Design Guide for Springback Compensation
(Graphic courtesy The Fabricator)
Springback is the general distortion of a part after its removal from the forming pressure. Your component literally springs back in its original direction.
Why does springback in roll forming happen? Just look at the roll form design process — when your metal is bent, the inner region of the bend is compressed while the outer region is stretched. That makes the density greater on the inside of the bend than on the outer surface. The compressive forces are less than the tensile forces on the outside of the bend, making your metal want to return to its old form.
The amount of springback varies based on the piece of coiled metal you use.
Springback Compensation Methods
Springback in sheet metal manufacturing is something you can predict to an extent. Making sound springback predictions will allow you to better select roll form tooling, especially for bends with intense radii.
Knowing how to overcome the springback effect is less about prevention and more about preparation. There's no true solution to the problem of how to reduce springback in bending. Instead, by overforming, a designer can usually compensate for the inevitable.
The main predictors of springback in metal forming are yield point (the point at which a metal will stop reverting to its original shape) and elastic modulus (the change in stress with an applied strain).
Use the following as a bending springback calculator of sorts. They assume there is a 1:1 relationship between the metal’s thickness and the inside radius:
- Cold-rolled steel: 0.75 to 1.0 degree
- Hot-rolled steel: 0.5 to 1.0 degree
- Mild aluminum: 1.5 to 2 degrees
- 304 stainless steel: 2 to 3 degrees
- Copper: 0.00 to 0.5 degrees
- Brass: 0.00 to 0.5 degrees
Check out more on bend radius and springback formulas here.
Communication is Key for Successful Roll Forming Design
While end flare and springback are inevitable in roll forming, understanding these quirks allow for proactive design consideration. Through careful roll design and strategic implementation of techniques like stretch forming and overforming, you can minimize end distortion and compensate for springback.
Remember, a successful roll forming project requires open communication between the designer, manufacturer, and customer to ensure everyone is on the same page about the part’s specifications and how to deal with inherent forming quirks.
Ready to Partner With a Roll Former?
Are you encountering challenges in sheet metal design and manufacturing, especially with springback and end flare issues? Dahlstrom Roll Form provides tailored solutions with expertise. Our team aims to enhance sheet metal production efficiency, ensuring precision and quality in your designs. Reach out to Dahlstrom today to optimize your sheet metal designs and overcome manufacturing obstacles together.
(Editor's note: This article was originally published in September 2018 and was recently updated.)
You May Also Like
These Related Stories
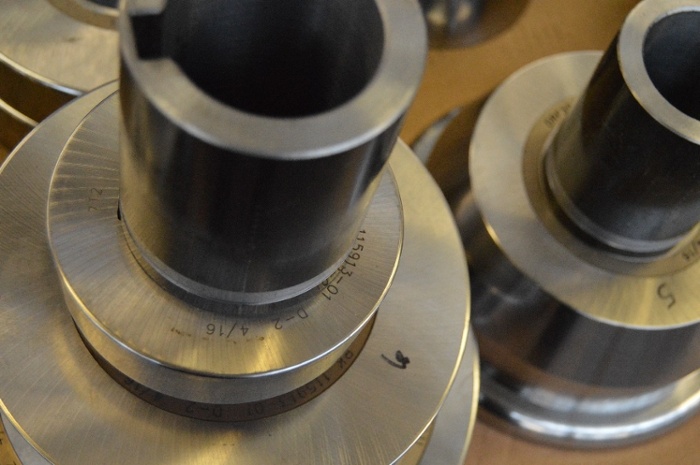
Roll Forming Tooling Design: Build In-House or Outsource?
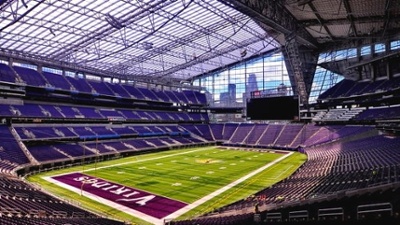
Famous Buildings With Dahlstrom’s Architectural Roll Forming: Part II
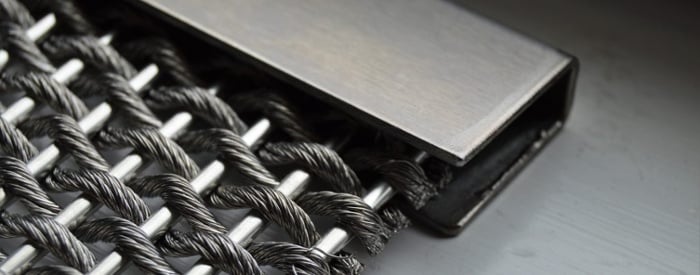