HSLA Steel Won't Break Your Back (Or Bank)
While conventional steel is renowned for its strength, it often carries the burden of significant weight. This association stems from the inherent link between density and strength in materials. However, advancements in steel technology have introduced High-Strength Low-Alloy (HSLA) steel, a revolutionary material that defies this expectation.
HSLA steel is meticulously engineered to deliver exceptional strength while maintaining a surprisingly lightweight profile. This translates to a material that offers the robust performance of traditional steel but with a significant reduction in weight. This attribute makes HSLA steel particularly relevant in roll forming applications, where weight optimization is a key consideration.
The following sections will explore the distinctive features and advantages of HSLA steel compared to conventional carbon steel, highlighting its benefits within the realm of roll forming.
What Is HSLA Steel?
High strength low alloy steel is popular among manufacturers for its enhanced mechanical properties and increased ability to resist corrosion compared to standard carbon steel (aka mild steel).
Its properties and unique capabilities make HSLA steel different from other steel. Many standard steels are made to meet a specific chemical composition. HSLA steel is made to achieve specific mechanical properties.
The term “low alloy” means that the metal has between 1.5% and 5% total alloy content, giving this steel advantages over standard carbon steel and other metals.
What Are the Advantages of High Strength Low Alloy Steel?
There are many advantages to using HSLA steel, and suppliers can highlight certain properties based on what other metals are added to the mix. Notable benefits include:
- High yield strength
- Improved formability and weldability
- Cost-effectiveness
- Better corrosion resistance
High Yield Strength
HSLA steel provides a high yield strength – the amount of force you can put on the steel before it starts to bend (aka, plastic deformation) and doesn’t rebound back into place (aka, elastic deformation).
Most high strength low alloy steel can take on high-stress loads and easily spring back into place. Many engineers call this the ability to bend “elastically.” This high yield strength allows the steel to resist bending or breaking. You can imagine the benefits this provides in structural applications. (More on them shortly.)
It’s important not to confuse strength with hardness. A steel can have a high level of strength and still withstand applied loads without cracking or bending. A metal with increased hardness doesn’t absorb impact as well and often will crack when enough force is applied.
To put it simply, when we talk about applied loading, "strength" refers to the amount of force a material can withstand before it starts to deform. On the other hand, "hardness" is about how well a material can resist being deformed in the first place. However, if a material is subjected to excessive force, it's more prone to cracking or breaking. While strength and hardness are closely related, they are distinct properties that make materials suitable for different kinds of tasks.
Resource: Material choice is one of many roll forming design considerations. Our free e-book below goes into depth on all the other factors that impact the quality of your finished component. Download below:
Improved Formability and Weldability
One component that makes HSLA steel valuable in the manufacturing industry is that its increased strength still allows for formability and weldability. Many believe that the alloying process would cause these properties to suffer, but HSLA steel is equal to, if not better than, standard carbon steel when it comes to forming and welding.
The formability of high strength low alloy steel is improved due to its ability to bend without breaking. This makes it easy for manufacturers to bend it at any angle up to 180 degrees (meaning formed back on itself) without any cracking or “crazing.”
When talking about welding HSLA steel, many manufacturers will alloy the metal with ingredients that possess high weldability. It’s not uncommon for the engineer designing a project to request specific HSLA steel properties that match the needs of their specific application.
Cost-Effectiveness
Increasing the carbon content of steel is the most cost-effective way to increase its strength.
Generally, the costs associated with creating HSLA steel are typically higher than with other metals. However, due to the strength-to-weight ratio, you gain by using HSLA, you’ll use less material and decrease your costs.
This reduction in cost makes the steel suitable for any budget. Larger companies can buy HSLA steel in bulk to accommodate large orders, and it provides smaller companies access to high-quality metal fit for several industries, highlighting the diverse HSLA steel uses across sectors.
Better Corrosion Resistance
HSLA material properties won’t match red metals such as copper, brass, and bronze; or the high chromium stainless steels in corrosion resistance. However, HSLA steel has a slightly higher resistance to corrosion than standard carbon steel.
This is because of the microstructure that comprises high strength low alloy steel. And by adding chromium, you can make HSLA steel even more corrosion resistant.
In Which Industries Will You Find HSLA Steel?
Due to its relatively low weight and high strength, certain industries favor HSLA steel over other roll formed metals. For example, the solar industry prefers to use it for solar racking systems on commercial buildings. Higher strength can be obtained with thinner gage steel reducing the additional static load these systems apply to roof structures. No loss in capability is realized with systems still being able to support the panels themselves as well as wind and snow loads. Here are a couple of other industries that favor high strength low alloy steel:
Automotive
One of the most common places to find high-strength low alloy steel is in the automotive industry. And it’s not hard to guess why.
HSLA’s material properties make it great for the automotive industry. Two of the main areas that benefit from HSLA steel are fuel efficiency and strength.
Fuel Efficiency
HSLA steel has significantly benefitted fuel efficiency in vehicles by allowing for the construction of lighter yet strong automotive components. Its lower weight reduces the overall mass of the vehicle, which in turn requires less energy (fuel) to move, leading to better fuel efficiency.
In short, the lighter the car is, the easier it is for the engine to move the car, resulting in better mileage.
Strength
Strength is also important in auto applications. Referred to as “toughness” in steel specifications, it’s common to find HSLA steel in vehicle doors and side panels. This serves two purposes:
- To provide the vehicle with enough strength to carry its passengers
Construction
Common construction projects like commercial, institutional, and residential buildings, travel infrastructure, and others use some form of HSLA steel.
As with sheet metal applications, HSLA steels can be hot rolled into bars, plates, and structural shapes used for construction. The same benefits of strength-to-weight ratio still apply, making these grades of steel popular with engineering firms designing these projects.
Fun fact: High strength low alloy steel is the material of choice for many roller coasters.
The Steel That’s a Steal
High strength low alloy steel is a valuable commodity for many industries. Its relatively low weight and high level of strength strike a perfect balance – one that’s suitable for numerous construction and architectural projects. (Not to mention it’s cheaper than many alternatives.)
Being able to cold roll high-strength materials such as high-strength, low-alloy steel gives you an advantage over standard-strength materials such as 1040 carbon steel. HSLA steel is great for structural components in many industries.
Note: This blog was originally published in October 2022 and was updated August 2024.
Learn how Dahlstrom can help you create strong parts for your industry:
You May Also Like
These Related Stories
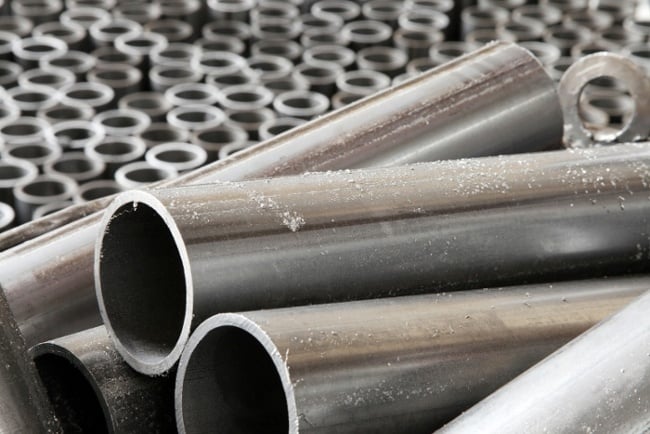
Beyond Steel: Mastering Metal Properties for Your Roll Forming Project
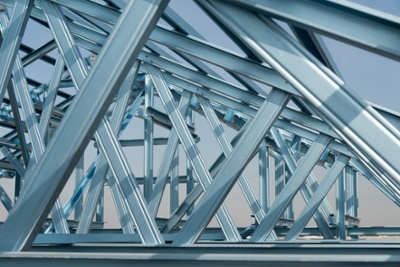
Galvanized Steel Vs. Stainless Steel in Architecture & Interior Design
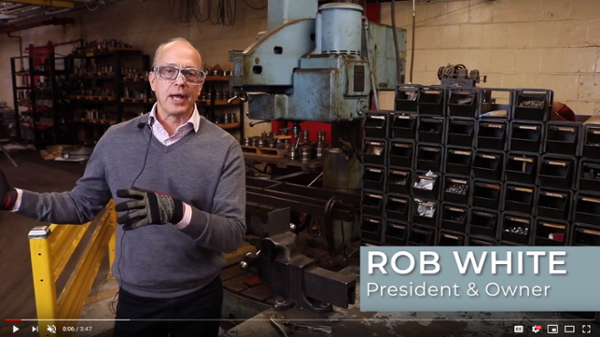