7 Roll Forming Products You (Probably) See Daily
Getting a comprehensive understanding of roll formed parts and the process can be challenging – especially if you’re new to the method.
The best way to gain knowledge on the topic is by diving into real-world examples. In this article, we’ll explore seven prime roll forming products that you may not realize are roll formed parts.
7 METAL ROLL FORMING PRODUCTS IN DISGUISE
Roll forming products are all around you. Just look at the buildings and infrastructure you pass by every day:
- Power distribution components
- Warehouse & data storage
- Commercial food storage
- Solar
- Trains
- Trailers & trucks
- Guard sign posts
1. Power Distribution Companies
For data centers, commercial retail, and higher-ed buildings, the power distribution system is vital infrastructure. These systems are highly proprietary and implemented by thousands of feet per project. Consequently, custom roll formed parts are critical in both current-carrying and non-current-carrying equipment.
- Copper busbars & conductors (current-carrying)
- Cable trays & wire raceways (non-current-carrying)
Why does roll forming play an important role?
Roll forming allows for huge volumes, tolerance control, complex profiles, and specialized materials like tin-plated copper, unlike other manufacturing methods.
Resource: Dual-source supply is a great way to lower your supply chain risk. A quality domestic second source supplier will help you make sure your work is done on time so you can keep moving forward with no major disruptions. Learn more here: |
2. Warehouse and Data Storage
Warehouses go hand in hand with power distribution. Yet they still deserve a separate mention, because they’re filled (to the max) with old-school roll formed shapes like angles and channels.
The large corporations of the world need these angle and channel components for:
- Shelving posts
- Shelving supports & crossmembers
- Automated pallet rails
Without roll formed parts, warehouse distribution wouldn’t be able to function at the incredible level and capacity it does today.
Sheet metal roll forming is great for these industries because it produces parts at high volumes, allows for in-line hole punching, and offers tight tolerance control.
3. Commercial Food Storage
Roll forming is used extensively in the commercial food storage industry. It creates the components that go into refrigerators and freezers including:
- Textured paneling for decorative purposes
- Kick plates by the floor that keep dust at bay
- Stainless steel hand rails and protective sills
- Insulated shelving structures that hold the goods
Why choose roll forming for commercial food storage?
Roll forming offers complex profiles, tricky hole patterns, and tight tolerances for final assembly.
4. Solar
Similar to the power and warehouse distribution industries, roll forming is a major reason why solar power reached its ever-present status in society and is now a viable source of energy. Manufacturers use roll formed parts to hold vast arrays of solar panels at specific angles for years into the future.
These components include:
- Robust hat channels, C-channels, & Z-purlins for utility-scale solar farms
- Lightweight ballast trays and mounting structures for commercial roofs
Roll forming allows for proprietary designs, large volumes, and the use of specialized materials. Roll forming also offers in-line punching to allow for easy field assembly.
5. Trains
Train cars consist of some of the longest, most uniformly shaped components known to man, reaching up to 80 feet long. While train manufacturing is a niche market, from exterior to interior, roll forming is the only way to produce these parts:
- Exterior roof and side panels
- Protective steel sill plates
- Wall and ceiling stiffening channels
- Decorative stainless steel rails
- Stainless steel transition pieces
6. Trailers & Trucks
Let’s start with cargo trailers and delivery trucks. Every type of roll formed channel can be used to build the interior framing/skeleton for the cabs on these things. Also, you’re likely to see some stainless steel trim on the exterior of high-end trailers. The same goes for 18-wheelers, but those also have giant wheel fenders, which are made with a very specific type of roll form machine.
Why is roll forming the preferred method?
Hat and box channels make sturdy, lightweight frames, some parts are finish-critical, and fenders are very wide.
7. Guard Rails & Sign Posts
Ever think about the millions of miles of guard rail that exist on this planet? Much like wheel fenders, roll form companies with dedicated machines produce guard rails at incredible speeds, making them extremely low cost and abundant.
Lastly, the same existential question applies to road signposts. While they can be cold-formed, these posts are most commonly made via “hot” roll forming. In this metal forming process, steel rails are heated to 2300°F before passing through the roll dies.
WHAT MAKES THESE ROLL FORMING PRODUCTS WORK?
In the examples above, custom roll formed shapes are particularly useful due to their ability to be produced at a rapid pace while maintaining design accuracy. Yet it’s also ideal for parts with multi-bend profiles, or those that require high-end finishes.
Hole punching, bending, and cutting to length are all easy to fit into one continuous process, rather than separate steps. In all of these cases, it’s simply more cost-effective and productive to use this tried-and-true method of metal forming.
We hope this list helps you determine if that part you’re designing could ultimately be roll formed. But if you are still uncertain, send us a drawing for a quick compatibility review from our team.
Still doing research? Check out our 'Why Roll Forming?" page via the button below:
(This article was originally published in October 2018 and was recently updated.)
You May Also Like
These Related Stories
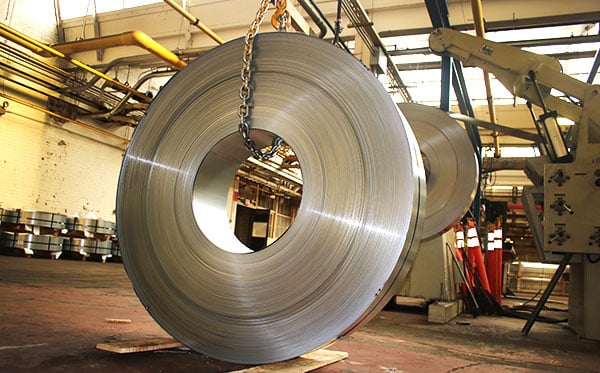
What Is a Roll Forming Machine? Roll Forming vs. In-House Forming
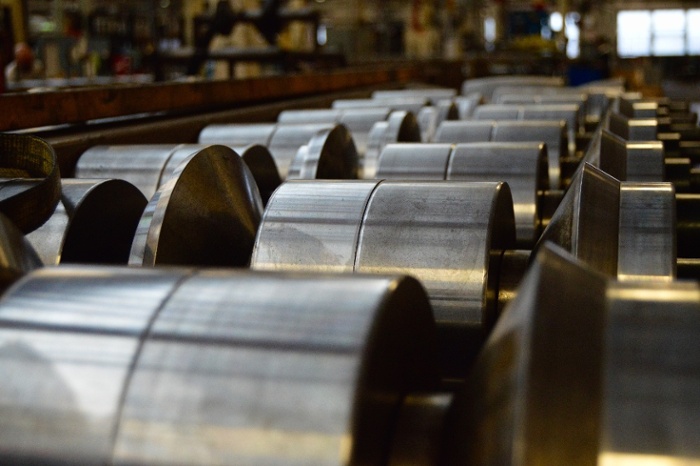
The 4 Most Common Myths of Roll Forming Metal
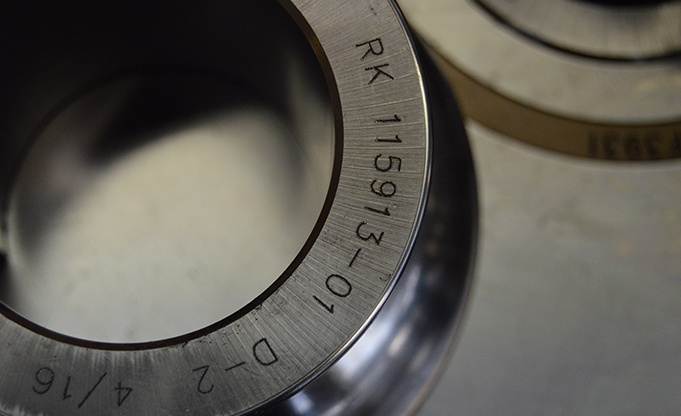