Cold Roll Forming Vs. Hot Rolled: Which is Right for Your Project?
The Cold, Hot Facts Between Cold Roll Forming and Hot Rolling
When selecting roll forming for your projects, durability, flexibility, and cost-effectiveness are essential to describe the process. From industrial to commercial applications, roll forming offers remarkable adaptability.
But how do you know when to use cold roll forming vs. hot?
Although hot rolled steel shapes comprise the highest volume of rolled items in the United States, did you know that contract roll forming only uses cold rolling? So, to us, cold roll forming is just roll forming. Hot rolling is almost nonexistent in the contracted OEM roll forming world. This process is left up to the steel mills that make standard, commodity-type shapes.
So what differences make the cold process applicable for roll forming and sometimes a better choice than hot forming?
What Is Hot vs. Cold Roll Forming?
While both hot and cold roll forming processes shape metal into desired forms, they are worlds apart regarding temperatures, techniques, and applications.
Hot Forming
Hot forming combines extruding and rolling using molten steel under extremely high temperatures. Some structural shapes, such as those used in holding up and reinforcing buildings, cannot be made any other way.
A classic example is a large “plunger” filled with hot steel, which extrudes a shape used for an I-beam in structural applications. A series of rollers then fine-tune the shape to the tolerances required for that particular shape.
It doesn't make sense to take a steel bar and cold form it into something like an “I” shape. Hot forming can also produce coiled steel sheets as thin as 0.60”.
The challenge is that this is a very specialized mill process. Using high temperatures and molten material requires huge furnaces, which aren’t abundant. Buying the machinery needed to safely manage molten steel and finding experienced workers to operate the equipment is a huge investment.
Cold Forming
True-ish to its name, cold forming involves making shapes at room temperature or slightly above room temperature.
It only takes a little high-temperature, specialized equipment to produce cold-rolled shapes. Flat and coiled sheets are the two forms of raw material typically fed through roll-forming machines.
It is possible to use hot-rolled steel in sheet form as the raw material in cold roll forming. However, you wouldn’t form it “hot off the presses,” so to speak—it would have been room temperature for days by the time your roll former worked with it.
(Resource: Want to know more about cold roll forming? Click below to read our guide!)
What Is the Difference Between Hot Rolled and Cold Rolled Steel?
Both hot and cold forming have uses. The properties of specific metal grades sometimes dictate whether they should be hot or cold formed.
Differences include:
- Run speed & quality
- Structural uses
- Strength
- Size limits
Run Speed & Quality
It might take 50 rolls to thin out a hot steel workpiece with hot roll forming, but that piece may require 100 passes of cold roll forming. Why? It takes more force to manipulate the metal.
However, with more rolls, you can get tighter tolerances on the piece and a higher-quality end product. This process can increase costs because of the additional machinery and labor time required, but it may be worth it to your customer.
Structural Uses
Structural shapes like I-beams are usually hot rolled. The steel used for I beams differs from that used in cold forming. It’s hard and less ductile, which makes it more challenging to bend when cold. Hence, it's used for structural shapes that carry much weight!
Cold roll forming has many commercial and industrial uses. They include:
- Signposts & guard rails
- Solar
- Refrigeration
- Escalators & elevators
Click here for more information on some of the many uses of roll forming.
Strength
For similar grades, cold rolled metal can be stronger than hot rolled metal because of work hardening. When you put a piece through 100 vs. 50 passes, the strain you put on the material hardens it and makes it stronger.
If the roll-formed part requires hot-rolled sheets, you'll still get some added strength. But it would be stronger if you started with standard cold-rolled material.
Size Limits
As we mentioned, steel sheets are only hot rolled up to a certain thickness. You can’t buy 20 gauge hot rolled sheets. At that point, you’ll have to use cold rolled.
Since roll-formed parts are usually produced from coiled material, product length is limited only by the amount of material in the coil and the handling of the finished component. Hot-rolled shapes are also limited by equipment capability.
Roll Forming FAQ: Get the Hot (And Cold) FactsWhich process results in stronger steel products? Cold roll forming generally produces more robust steel products due to work hardening, in which the material becomes stronger as it is repeatedly deformed. Are there any advantages to hot forming? Yes, hot forming allows for the creation of more complex shapes and can sometimes require fewer forming passes. What are some common applications of cold roll forming? Cold roll forming is widely used in various industries, including construction, automotive, solar energy, etc. It's often used to create products like signposts, guard rails, solar panel components, and refrigeration parts. |
When Roll Forming Makes Perfect Sense
Cold roll forming usually results in better, more attractive finished surfaces with closer tolerances. During the forming process, the material can be quickly galvanized, painted, or powder coated into various shapes.
The point, of course, is to use the best process for the job. Do you need to know whether your application fits with roll forming or an alternative method? Ask a manufacturer before committing to either cold or hot roll forming.
Want to Learn More About Cold Roll Formed Parts?
Our Comprehensive Design Guide to Great Roll Formed Parts gives a good primer for optimizing your design for cold roll forming. Download the guide below:
(Editor's note: This article was originally published in January 2019 and was recently updated.)
You May Also Like
These Related Stories
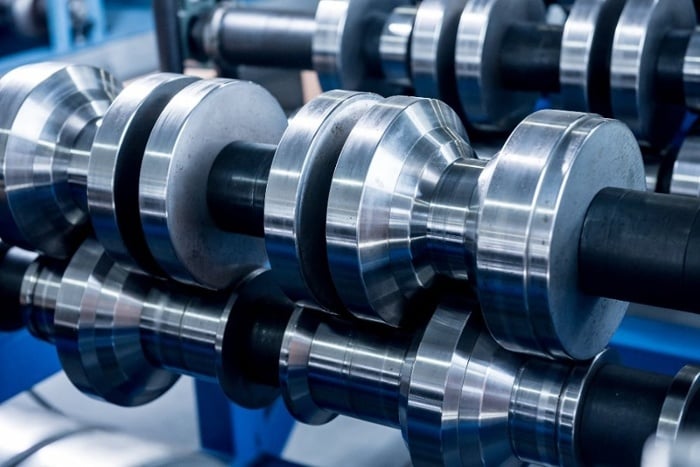
Custom Roll Forming Processes: Cold Roll Forming Steel
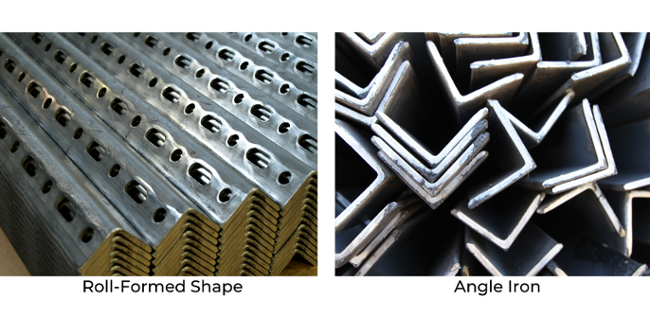
Need a metallic L-angle? Roll Forming vs. Angle Iron
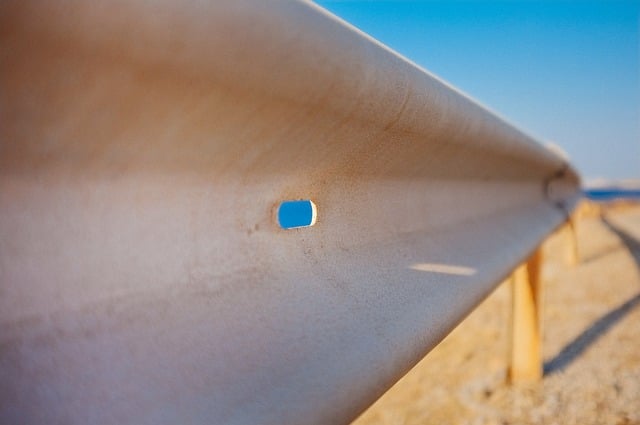