5 Must-Know Specification Tips from Metal Fabrication Experts
Bringing on a challenging production process can stump even the most skilled metal fabricators, preventing them from delivering their best work. However, you can take five proactive steps to make sure your vendor provides the optimal roll-forming process for your project.
Remember, your relationship with your vendor is a partnership. Success depends on open communication and a willingness to collaborate. A strong partnership produces high-quality products delivered on schedule, while a weak one can result in frustration and costly delays.
Let’s explore the five tips to improve both sides of the customer-vendor relationship.
Production Tips from Metal Fabricators
Being flexible and having good conversations between you and your vendor will help your project be successful. When working with a metal fabricator, keep these five tips in mind:
- Pick materials wisely
- Choose the coil-fed approach
- Make sure the tools are in good shape
- Assess your part’s complexity
- Loosen up tolerances
1. Pick Materials Wisely
As with any production method, choosing a suitable material is integral. The material you use needs to meet your project’s specifications for metal strength, dimensional tolerance, and appearance. Understanding the metal strength and other properties of different metals is straightforward with resources like ASM reference books.
Early collaboration with your roll forming or metal fabrication provider is essential to align the chosen material's metal strength and other characteristics with the desired processing technique. Material choice and understanding the needed metal strength affects the ease of production and can help you avoid costly design flaws.
If you value beauty in your project, you can have your manufacturer roll two metals simultaneously and side by side -- for example, some attractive stainless steel on the surface and less expensive carbon steel in the areas that won’t show.
2. Choose the Coil-Fed Approach
Manufacturers choose one of two approaches to processing a part -- pre-cut sheets or coiled strips.
While some parts require the cut-length approach, the coil-fed line is generally the most productive and consistent arrangement. This method requires only a simple setup. Your manufacturer may need a more complex arrangement depending on the need for:
- Punching
- Embossing
- Seam welding
- Curving
- Coiling
- Other considerations
Suppose these operations are part of the continuous forming process and there are few subsequent procedures. In that case, the vendor can create a custom arrangement so all work can happen directly on the roll forming or stamping line. If certain profile characteristics or size restrictions exist, separate, sequential punching and forming stations or specialized machines may be necessary. Again, early discussion with your provider will help you pick a direction.
Also, the only length limitation is the coil length your vendor feeds into the line.
Another bonus: Coil-fed line processes produce less waste than sequential forming steps using metal sheets!
3. Make Sure the Tools Are in Good Shape
Don’t be afraid to inspect your vendor’s equipment before agreeing to use its services. By using equipment in good condition, you can limit downtime and maximize part quality.
Ask to see preventative maintenance records and capability documentation on repeatability. Quality fabricating sources should have many examples as part of their daily routine.
Regarding tooling, your vendor should maintain its condition, sharpening, and part contact surfaces. Contrary to what you might think, you should pay for your tooling maintenance costs, especially if you want to take possession of your tools.
4. Assess Your Part’s Complexity
Grab a piece of paper and draw a continuous line of any shape -- as long as it doesn’t cross itself, roll forming can likely transform that line into a metal profile.
Even though roll forming can produce many shapes that stamping and other forming techniques cannot, complex metal profiles add to tooling costs and may slow down run speeds; profiles that get complete contact with the tool surfaces are the least expensive to produce. (The most basic example would be a flat sheet with a flat roller above and below.)
As metal profiles evolve into “tube-like,” rolls cannot contact the inner surfaces. While this type of “air-bending” of profile elements often happens in shapes, it does add to tooling costs.
If avoiding certain features is impossible, contact your provider early for a concurrent design consultation!
Taking this advice can further increase production speed -- a hallmark of roll forming.
5. Loosen Up
Roll forming allows for defined corners and angles with a bend radius. Just because other metalworking methods may offer sharper-defined radii doesn’t mean you need to push your luck.
Depending on the metal type and thickness, your bend radius should be at least 1x to 1.5x your material’s thickness. Tight corners can lead to increased tool wear, surface coating buildup on your tools, and maybe even a burnt-out roll-forming machine. Tight corners can also lead to stress cracking in harder metals.
Also, loosen your darn tolerances. The goal here isn’t to strangle your manufacturer’s process. In the end, nobody benefits from tolerances set too tight. Consider functional tolerance review instead of blanket title block tolerancing. A component off the mark by 0.001” isn’t going to kill anyone.
Tighter tolerances result in more significant tooling costs, longer development time, and a need for a higher-grade material—none of which help your company’s bottom line.
Roll Forming Insights: Your Must-Know FAQs
The suitable material and metal strength aides in your project’s specifications to avoid costly design flaws.
Coil-fed processing boosts productivity consistency and reduces waste compared to cut-length methods.
Well-maintained tools minimize downtime and enhance part quality, ensuring efficient production. |
Set Your Part Up for Success
Preparation and clear communication of your preferences to the vendor and their feedback can streamline any metal forming process. Most metal fabricators are eager to collaborate closely throughout the project to iron out any production issues before finalizing the agreement.
Need More Help Designing A Great Roll Formed Part?
We've crafted a detailed guide outlining the essential design principles for creating cost-effective, efficient parts. By following our guide and maintaining open lines of communication, you can improve your collaboration with vendors, leading to better outcomes and innovations in your roll-forming projects.
You May Also Like
These Related Stories
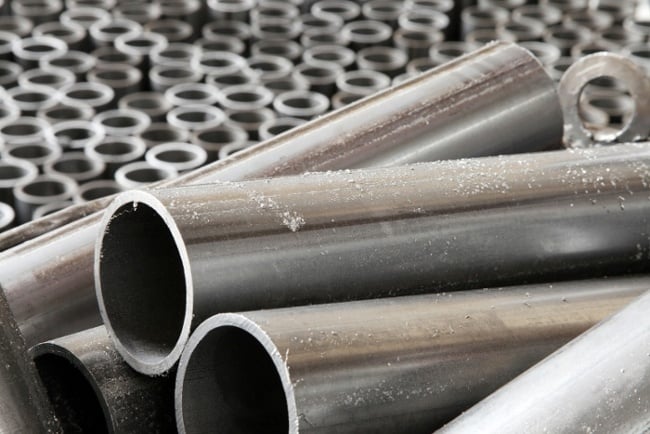
Beyond Steel: Mastering Metal Properties for Your Roll Forming Project
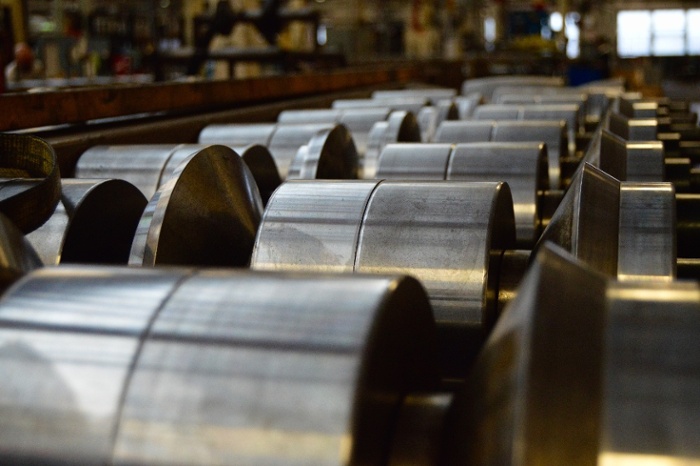
The 4 Most Common Myths of Roll Forming Metal
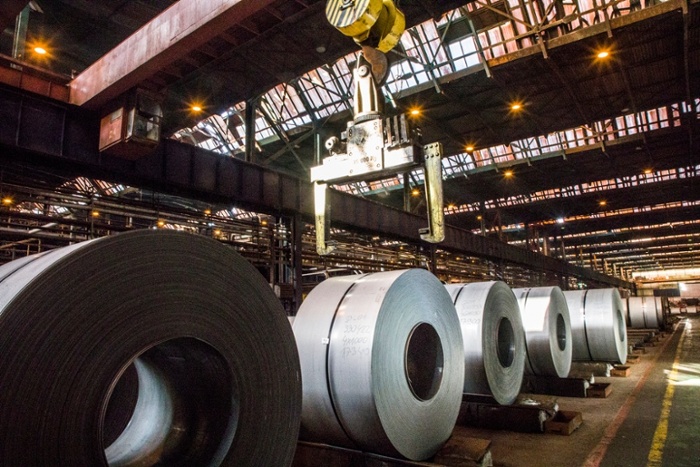