Roll Forming Tolerance: The Fine Line of Achieving Precision
In the world of roll forming, managing tolerance is a delicate balance between precision and adaptability. It's both an art and a science, much like fine-tuning a machine to achieve peak performance on the production line.
The ability to maintain tight tolerances depends on various shifting factors. For example, stricter control is possible when a tool makes complete contact with all surfaces of the formed metal. In contrast, tolerance can vary widely with box channels where tools don't fully engage.
Navigating roll forming tolerance requires understanding the range on which it operates. In this blog, we will be uncovering the key aspects of roll forming tolerance, including:
- The factors that influence it
- Strategies for maintaining control
- The practical effects of tolerance variations in real-world applications.
Finding the Strike Zone in Roll Forming Tolerance
In roll forming, achieving the perfect balance of tolerance is like fine-tuning a machine to deliver flawless results. Each roll forming process has its specific tolerance range, much like a machine’s performance range, which determines the limits within which it can operate optimally.
Tolerance = A defined range of measurements that enable a manufactured part to function properly |
This isn't just about minor adjustments; it's a complex interaction of accuracy and adaptability that requires constant attention and fine-tuning.
Just as an engineer adjusts a machine to avoid variations that could lead to production errors, a roll forming specialist must confirm that the process remains within the established tolerance range. This involves carefully monitoring every step to maintain consistency and avoid exceeding the acceptable limits.
Like an expert machinist, a seasoned roll forming engineer understands how to operate at the edges of these tolerances, pushing the boundaries while always being mindful of the risks involved. This expertise allows for optimal performance without compromising the quality of the final product.
The Cost of Precision | Pay to Play
When willing to pay more, you can aim for a tighter tolerance. This directly reflects the principle that "you get what you pay for."
So, what exactly are you paying for? Let’s look at:
- Tooling
- Bends
- Time
- Material
Tooling
The number of passes—say, ten passes vs. 25—directly impacts tolerance. The more passes you configure for your part, the more roll form tooling is required.
More forming stations relax the material, allowing more focus on each bend rather than performing multiple bends simultaneously.
Tighter tolerance = higher cost due to more tooling requirements.
However, there comes a point at which no amount of additional passes will increase the part’s tolerance.
Bends
The number of bends, in part, also plays a crucial role in roll forming tolerance.
A part with five or six bends may not hold the overall width as well as you’d like.
Dimensioning a part can be challenging. It's generally advisable to keep to the outside dimension rather than attempting to go to the inside.
The internal variations are larger due to contact with the part. It's always a good practice to send your drawing and negotiate if all tolerance requirements can be met.
Time
Time is money.
Costs mount in terms of staff time spent checking the part for range.
If the number of passes has increased, setting up the roll forming machine’s stands to accommodate additional tooling takes more time.
Material
The higher the yield strength of your material, the more difficult it will be to form.
Roll forming creates stress to counteract a material’s original shape, so choosing the right material for your needs is key to your part’s tolerance range. Some metals are easily formed, while others take more coaxing.
Factoring in the Quirks
This isn’t “Field of Dreams.” The roll forming process isn’t magic.
Despite how accurate your CAD drawing is (“If you build it…”), roll forming has built-in variability.
Engineers often desire a perfect part. But when the process and your budget limit you, you must spend more or cede some tolerance.
Understanding and managing these key factors are important in the roll forming process.
- End flare
- Springback
- Bow, camber, twist & webbing
End Flare
End flare, or distortion at the cut points, occurs as a material is progressively shaped. Residual stresses introduced during the process are most apparent at the ends of your components, sometimes leading to significant distortion.
Modifying end flare includes roll design procedures and stretch forming, which involves overforming, underforming, and finishing the section. However, there’s a point where adding more passes doesn’t reduce your end flare.
Sometimes, this leads to tough conversations that end about so:
‘This is the shape, and these are the tolerances up to 3” from each end.’
Another approach is annealing, a process of heat treatment followed by cooling that improves flexibility, reduces brittleness, and, importantly, relieves stresses absorbed during roll forming.
Springback
Springback is the distortion of a part when forming pressure is removed. This happens because the metal attempts to return to its original shape as the inner bend is compressed and the outer bend is stretched.
The degree of springback varies depending on the metal in use.
The main predictors of springback include the yield point (the stress at which material deformation begins) and the metal's elastic modulus (resistance to deformation).
Handling spring back is more about preparation than prevention. There's no perfect solution to reducing spring back in bending, but overforming can usually compensate for the inevitable.
Remember, the higher the yield strength, the more challenging it will be to form because more stress is required to counteract the material’s original shape.
Addressing Common Roll Forming Issues: The Role of Bow, Camber, Twist, and Webbing
Four specific types of deviations are essential factors that can significantly impact the precision and functionality of roll-formed components. To better control the roll forming process and achieve the desired outcomes, it's important to recognize and address these four potential issues:
- Bow
- Camber
- Twist
- Webbing
Bow: refers to a lateral curvature or deviation from a straight line in the horizontal plane. It can occur due to uneven stress across the width of the part during forming, causing the part to curve like a bow. This deviation from the ideal straight form can impact the precise alignment and fit of the roll-formed component in its end application.
Camber: is a curvature or deviation from a straight line in the vertical plane. This can happen due to uneven bending at different points along the part's length. Like a bow, a camber can also impact the component's usability in its final application due to deviations from the desired shape.
Twist: is the rotation of a part's cross-sectional shape around its longitudinal axis, often caused by uneven cooling or improper alignment of forming rolls. This can also significantly affect part tolerance, as a twisted part may not fit or function properly in its intended application.
Webbing: refers to the integrity of your material, as holes and stretching can affect your part’s tolerance, too. If they’re spaced every couple of inches and consume a significant part of your web, your forming will be affected – lots of waviness may occur.
Non-symmetrical parts are more likely to bow, camber, and twist due to uneven stress.
Careful control of the roll forming process, including using the correct tooling, ensuring proper alignment of the forming rolls, and maintaining consistent material properties throughout the process, can minimize these issues.
FAQs: Mastering Roll Forming TolerancesWhat factors influence the tolerance range in roll forming? The tolerance range is influenced by material yield strength, the complexity of the part's design, the number of bends, and the tooling used. High-strength materials and complex shapes generally require tighter control to maintain tolerances. How does the choice of material affect roll forming tolerances? Materials with higher yield strength are more challenging to form and can lead to more significant variability in tolerance. Selecting a suitable material that balances formability and strength is key to achieving precise tolerances. Why are frequent checks and increased passes recommended in roll forming? Frequent checks and additional passes help ensure that the part stays within the established tolerances. These steps allow for early detection of deviations and provide opportunities for adjustments, leading to better control over the final product. |
Mastering Roll Forming Tolerances
Roll forming is one of the most cost-effective methods for producing complex shapes with multiple bends. However, it comes with its own set of challenges. Understanding and managing these challenges effectively is essential to consistently delivering components that meet the required tolerances.
Control is the key to staying within the specified tolerances. Improving control can be achieved by increasing the number of passes and conducting frequent checks. Pay close attention to factors such as dimensional profiles, end flare widths, and the symmetry of your part.
Remember that higher yield strength materials can present more challenges during forming.
Collaboration Leads to Success
Effective communication is essential in tackling the complexities of roll forming. If you're considering roll forming for your part, we're here to help. Share your design with us, and we can begin a conversation to determine the best approach for your needs.
You May Also Like
These Related Stories
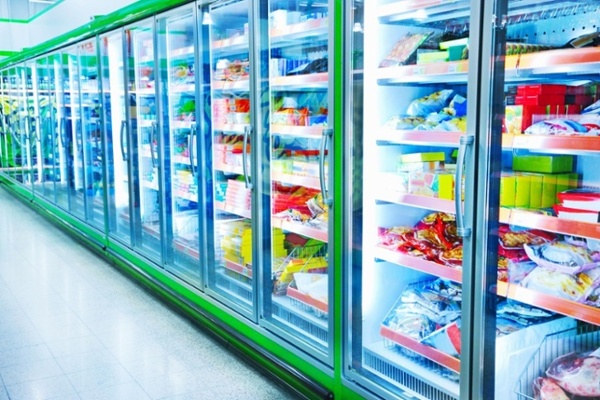
Commercial HVAC-R Parts: Is Roll Forming a Fit?
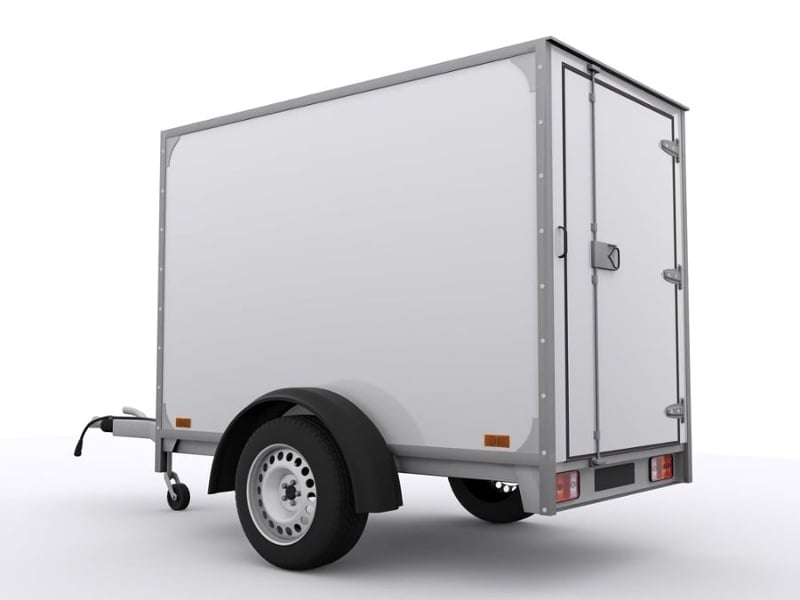
A Roll Forming Design Guide for Enclosed Trailer Parts
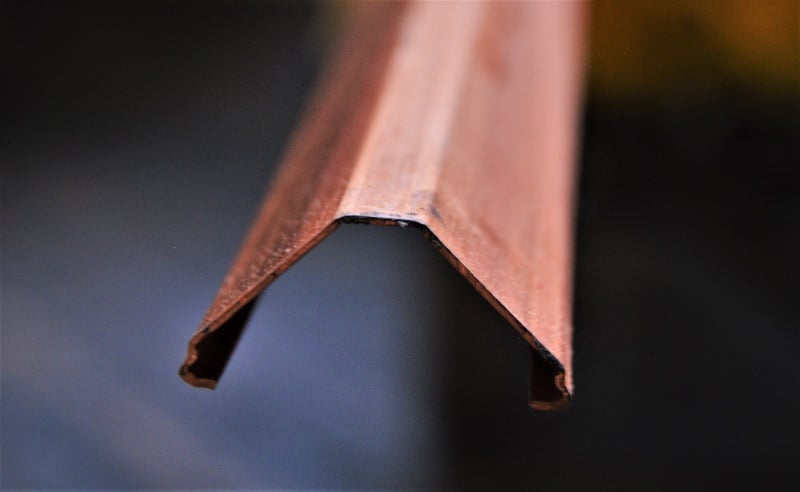