Commercial HVAC-R Parts: Is Roll Forming a Fit?
The commercial HVAC-R (heating, ventilation, cooling, and refrigeration) industry is rapidly growing. Experts predict the global market will increase from $552 billion to $742 billion by 2028.
Heightened consumer and governmental emphasis on energy efficiency largely drives this surge.
For commercial HVAC components, new constructions and developments are accelerating growth, fueled by a focus on environmental sustainability and green energy solutions.
The commercial refrigeration parts sector is growing because organized retail demands more parts. Consumer interest in packaged foods is also increasing. Additionally, a surge in the international food trade contributed to this growth.
As the industry expands, businesses must partner with a manufacturer that prioritizes quality, efficiency, and innovation to stay competitive and optimize their supply chains.
The global market is expanding and supply chains are under pressure. This will lead to intense competition for parts used in refrigeration, heating, and cooling. Getting ahead of your rivals and finding a roll forming partner will be good for your business. Let’s explore why:
Metal Roll Forming HVAC-R Components
You'll need a lot of long, slender, metal parts to create HVAC-R systems.
Companies frequently use roll forming in the HVAC and refrigeration sectors to make items like ducts, frames, and panels. This technology allows for precise control of dimensions. It can also incorporate complex profiles and hole patterns. These features are crucial for the components in these systems.
Roll forming is for large projects that need high standards and precise measurements. This is because the parts produced are consistently high quality and maintain tight tolerances.
What is Roll Forming?
Roll forming is a process that uses large machines to bend flat sheet metal into a uniform shape as the metal passes through a series of roll dies. The machinery moves slowly to ensure precision in shaping the metal.
A highly repeatable process, roll forming allows engineers and designers to create customized HVAC and refrigeration components. Roll forming is more effective than other metal shaping methods once the tooling is set up. It consistently produces components efficiently, even during extended production runs.
Whether the parts you need are decorative or structural, a manufacturer can make them. Roll forming is the most economical process for creating:
- Angles
- Channels (U, C, J, box, hat)
- Parts with complex, cross-sectional shapes
- Parts with intricate hole patterns
- Parts with continuous lengths of 20+ ft.
Hole punching, bending, and cutting to length can easily fit into one uninterrupted process rather than separate steps, making roll forming cost-effective and productive.
Learn More: Commercial HVAC and Refrigeration Roll Forming Services & Capabilities
Need to know more about the roll forming process and how it can benefit the commercial HVAC and refrigeration industries? Download our free guide, “Why Roll Forming?”
Roll Forming Commercial HVAC and Refrigeration Parts
Exactly which heating and cooling parts and refrigeration components benefit from roll forming?
Commercial HVAC Parts
Several interior and exterior structural parts of HVAC systems are roll formed including:
- Air conditioner cases
- Cooling tower louvers
- Dampers
- Ducts
- Electric heater housings
- Filter frame units
- Structural components and handrails for industrial chiller units
Even the tubing that’s part of the refrigerant exchanger in an HVAC system is made of roll formed copper.
Commercial Refrigeration Parts
Roll forming is a significant component of the commercial refrigeration industry. It produces frames for refrigeration units that store meat, dairy, and produce, as well as:
- Insulated shelving structures
- Kick plates
- Protective sills
- Stainless steel handrails
- Textured decorative paneling
Whether you’re using stainless steel parts for framing or pre-painted aluminum sheets for decoration, roll forming produces a clean and attractive finish.
Bonus: Expanding adhesive foam needs to stick to the roll formed walls that encase the insulated frames of refrigeration units. If your roll former offers powder coating, it can send your parts through the cleaning system of its powder coat line. The parts are then tested using the dyne system. This is a special series of inks applied to surfaces to determine cleanliness. As they increase in level, their adhesion abilities increase. The higher the dyne level, the cleaner the part is. |
Learn How To Design the Perfect Roll Formed Parts
Download our Comprehensive Guide to Great Roll Formed Parts:
Advantages of Roll Forming Commercial HVAC-R Parts
Roll forming has many advantages over other metal shaping methods. Original equipment manufacturers (OEMs) often turn to custom roll forming corporations for their ability to both form high-strength metals and work with:
- In-line features
- Complex profiles with intricate bending
- Tight, repeatable tolerances
- Large material size
Less Is More
When working with a roll former, less is more, as in:
- Less tool maintenance – Because they produce parts and features in a continuous motion, there’s less strain on tooling.
- Less human error – Automation handles almost everything, needing less human labor and decreasing the likelihood of mistakes.
- Less scrap – In roll forming, scrap is typically 1-3% of your overall cost. That’s especially significant when you’re working with expensive materials.
Quality Is Key
Roll forming is beneficial for commercial HVAC and refrigeration parts because it ensures consistent uniformity in each production run. This consistency is important for ensuring that the parts fit together properly and function correctly. It also helps to streamline the manufacturing process and reduce waste.
Roll forming machines also easily and precisely form high-strength steels while accommodating for springback distortion.
Roll forming is perfect for aesthetic projects where tool marks from other types of forming aren’t acceptable.
Learn more about the anatomy of a roll forming line and the complete roll forming process:
Find a Reliable Roll Forming Partner
Many of the perks of roll forming are more about the processes certain roll formers adhere to, and not just the parts they produce. Look for a reliable partner with these capabilities:
- Product inventory – A “trigger-response” system is a highly-efficient way to control inventory.
- Raw material inventory – The right roll former won’t hoard materials inventory, keeping your costs as close to market as possible.
- Quarterly reviews
- Customer feedback
- Inventory levels
- Raw materials prices
- On-time delivery
- Low defect rate
- Safety
- Clean and organized facility
- Regular safety training & inspections
- Respected workforce
- Paid by skill – A good roll former knows they’re only as strong as their skilled labor force. The more skills a worker has, the more they get paid – meaning they’re highly invested in the quality of their work.
- Cross-trained – Having multiple skilled machinists means work doesn’t stop because one person gets sick. The whole team works together to produce your parts.
When you partner with a roll former providing all these services, you know they’re working to optimize the entire sourcing process.
Roll Forming Frequently Asked Questions:
How does the cost of roll forming compare to other metal forming processes when producing HVAC-R components?
Roll forming is highly efficient and generates low waste, making it usually more cost-effective for large-volume production. This process is continuous, which helps lower labor costs and tool wear. This ultimately leads to lower production costs compared to stamping or extrusion methods.
Roll forming excels in producing high-volume, complex shapes because of its efficiency and minimal scrap. It can be cheaper than both bending and extrusion.
Learn more about what goes into roll form costs here:
What specific environmental benefits does roll forming offer, especially in terms of energy consumption and waste reduction?
Roll forming is beneficial environmentally because it generates less scrap metal compared to other methods, which helps in reducing waste. The process is also energy-efficient as it typically requires less power, given that the metal is formed at room temperature without the need for heating.
Are there any limitations or challenges associated with using roll forming for HVAC and refrigeration parts, especially for complex or highly customized designs?
While roll forming is advantageous for producing long, uniform sections, it has limitations when it comes to producing parts with abrupt or intricate geometric changes. The initial setup and tooling costs can be high, making it less suitable for short runs or highly customized designs unless there is a significant demand to offset these initial expenses.
(Editor's note: This article was originally published in March 2023 and was recently updated.)
You May Also Like
These Related Stories
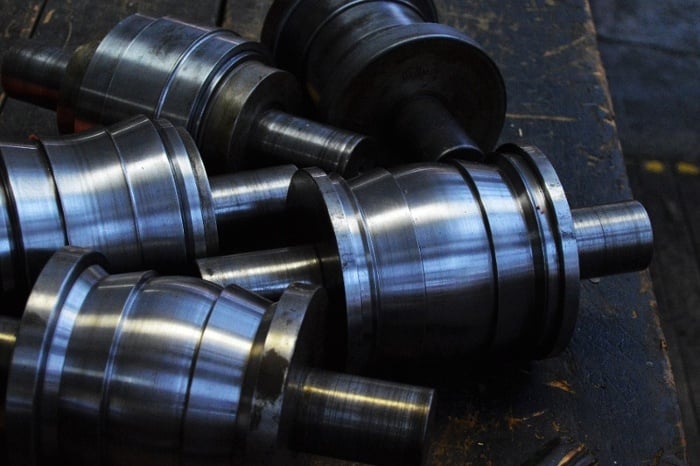
Why Get Custom Roll Forming From a Single Source?
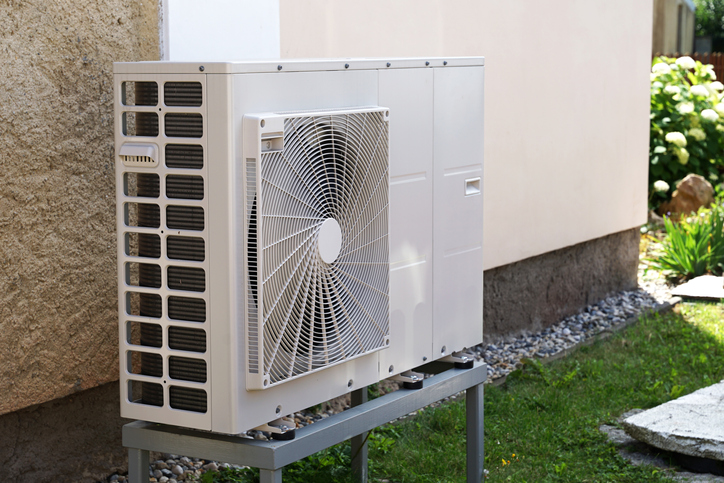
High-Quality Heat Pump Parts: Try Metal Roll Forming
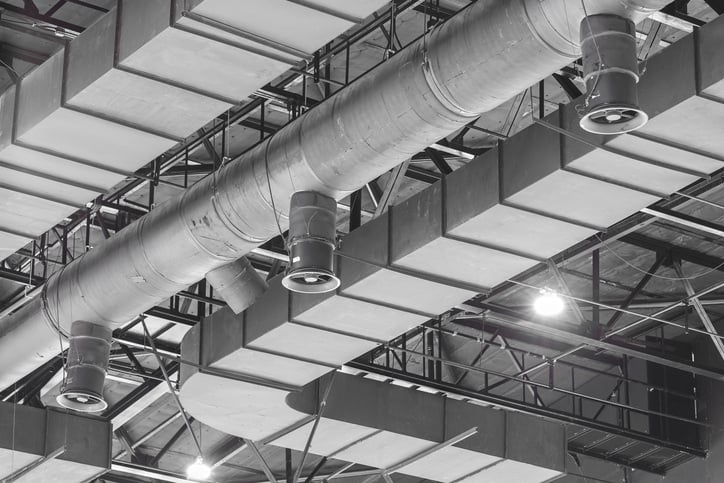