Roll Forming Commercial HVAC Material Selection Guide
Have you ever felt the comforting rush of cool air on a sweltering summer day or the warmth that chases away the winter chill?
It's easy to take for granted the intricate dance of components that bring these climate-controlled havens to life. But behind the scenes, a silent network plays a critical role in keeping a building comfortable: the HVAC ductwork.
This collection of metal channels snakes through buildings, delivering conditioned air exactly where needed. However, not all ducts are created equal, and selecting the right HVAC duct material is vital for optimal efficiency, sound control, and overall system performance.
Let’s explore the advantages of metal roll forming for HVAC duct material and the various sheet metal options available to meet your specific HVAC needs.
Why Choose Metal Roll Forming for Shaping Commercial HVAC Materials?
Metal roll forming stands at the forefront of HVAC duct manufacturing due to its precision, efficiency, and flexibility. This process involves gradually shaping a continuous sheet metal strip by passing it through a series of roller dies, each performing incremental changes until the desired cross-sectional profile is achieved.
Roll forming metal techniques are highly effective in producing strong, leak-proof ductwork that fits perfectly within building structures. Manufacturers look to roll forming because it:
- Yields consistent, high-quality products
- Minimizes material waste
- Allows for the creation of complex shapes with tight tolerances
- Provides a cost-effective, customized solution for each unique HVAC system
New to roll forming? Grab our Why Roll Forming guide to get an overview:
Evaluate Your Project Needs
It’s simple math: By assessing your HVAC system's needs, you can choose materials that are durable, efficient, and cost-effective. Moreover, the choice of sheet metal can significantly impact the overall performance and longevity of the HVAC system.
Here are some factors to consider when making your selection:
- Cost: Different metals come at different price points. Consider the project budget and weigh it against the benefits of each material.
- Durability: HVAC ducts need to withstand constant airflow and potential environmental factors. Choose a material with the strength to handle the job.
- Formability: Complex duct systems require bends and curves. Ensure the chosen metal roll forming material is flexible enough for your design needs.
- Weight: Lighter materials can be easier to install, particularly for overhead ducts.
- Reduce noise: HVAC sound dampening materials can be incorporated during the roll forming process to minimize noise transmission, a crucial factor in commercial HVAC systems.
Want to learn more about designing the perfect roll formed part? Download our guide today:
An HVAC Material List: A Look at Popular Sheet Metal Options
Choosing the right HVAC duct materials helps ensure efficient airflow and minimal energy loss.
While several materials are available for constructing HVAC parts, non-metal alternatives often fall short in durability, structural integrity, and resistance to extreme temperatures and pressures.
Using metal for your project instead of alternative HVAC material offers:
- Durability: Metal provides superior strength and longevity than alternative materials like fiberglass. This ensures your ducts can withstand constant use and temperature fluctuations.
- Airtightness: Seamless roll-formed metal minimizes air leakage, which improves system efficiency and reduces energy costs.
- Versatility: Metal roll forming allows for creating ducts in various shapes and sizes, perfect for accommodating complex layouts and tight spaces.
- Fire Safety: Certain metals have excellent fire resistance properties, contributing to overall building safety.
Selecting the correct type of sheet metal for HVAC ductwork is essential to achieve durability, efficiency, and safety. Here are some of the most commonly used HVAC duct material types:
Galvanized Steel
Galvanized steel is a widely preferred material due to its excellent corrosion resistance. This steel is coated with a layer of zinc, protecting it from rust and other environmental damage. Galvanized steel ducts are robust, long-lasting, and ideal for various HVAC applications.
Advantages:
- High corrosion resistance
- Long service life
- Easy to fabricate and install
- Suitable for both indoor and outdoor applications
Galvalume Steel
Galvalume steel is an alloy consisting of aluminum, zinc, and silicon. It offers the combined benefits of both aluminum and steel, making it a durable and cost-effective option for HVAC ductwork.
Advantages:
-
Excellent corrosion resistance
-
High strength-to-weight ratio
-
Cost-effective solution for large-scale projects
Stainless Steel
Stainless steel is another popular choice, particularly in environments where hygiene is paramount, such as hospitals and food processing facilities. Known for its non-porous surface and high resistance to both corrosion and staining, stainless steel ensures clean air delivery.
Advantages:
- Superior durability and strength
- Excellent resistance to corrosion and staining
- Easier to clean and disinfect
- Suitable for critical environments
Aluminum
Aluminum is a lightweight alternative to steel, making it easier and faster to install. Despite its lower density, aluminum offers significant strength and effectively reduces vibration and noise within the duct system.
Advantages:
- Lightweight yet strong
- Good resistance to corrosion
- Lower installation costs due to ease of handling
- High thermal conductivity
Copper
Although more expensive, copper is prized for its antimicrobial properties, making it an excellent choice for health-sensitive environments. Copper ductwork can significantly reduce the likelihood of microbial growth, contributing to healthier indoor air quality.
Advantages:
- Antimicrobial properties
- Superior heat transfer
- Highly durable and corrosion-resistant
- Low maintenance requirements
Comparison of Sheet Metal Options for HVAC Ductwork
Material |
Advantages |
Disadvantages |
Galvanized Steel |
|
|
Galvalume Steel |
|
|
Stainless Steel |
|
|
Aluminum |
|
|
Copper |
|
|
HVAC Noise Reduction
Noise reduction is crucial in HVAC system design, particularly in residential areas and sensitive commercial settings. Using sound-dampening materials within HVAC components can significantly decrease operational noise, fostering a more comfortable environment.
Sound-dampening materials are specialized substances designed to absorb and reduce noise within HVAC systems, thereby enhancing the overall comfort of indoor environments. These materials work by minimizing the transmission of sound waves through ductwork and other HVAC components. Popular types of sound-dampening materials include:
- Fiberglass: Fiberglass is a widely used acoustic insulation material due to its low cost, versatility, and ease of installation. It can be applied as a lining on the inside of ducts or used to wrap HVAC equipment.
- Polyethylene Terephthalate (PET) Foam: PET foam is a lightweight and flexible material that offers excellent sound-absorbing properties. It can be used as a duct liner or applied to the inside of equipment housings.
- Acoustic Metal Panels: These specially designed panels consist of perforated metal sheets with an acoustical lining attached to the back. They are highly effective at reducing noise levels and can be customized for specific applications.
How Do These Sound-Dampening Materials Fit into the Roll Forming Process?
Integrating sound-dampening materials within the roll forming process enhances the functional performance of HVAC ductwork without compromising efficiency. As sheet metal is passed through the series of roller dies, sound-dampening materials can be incorporated at various stages to create a composite ductwork structure. This approach ensures a seamless integration of noise reduction benefits into the manufacturing process.
During roll forming, sound-dampening materials such as fiberglass linings or PET foam can be laminated onto the sheet metal before it reaches the final roller die stage. This method allows for the noise-dampening layers to bond tightly with the metal, forming a unified structure that maintains the desired shape and specifications. Additionally, acoustic metal panels can be customized and added to specific sections of the ducts, where noise reduction is most essential.
Using sound-dampening materials in tandem with roll forming not only enhances the acoustical properties of the ductwork but also streamlines the production process. It allows manufacturers to create tailored solutions that meet both airflow efficiency and noise control requirements, all in a single, cost-effective production line. This integration ensures that HVAC systems offer a quieter and more comfortable indoor environment, addressing both performance and acoustic concerns.
Finding the Right HVAC Material Partner
Selecting the right HVAC material goes hand-in-hand with partnering with a reliable metal roll forming company. Look for a provider with extensive experience in the HVAC industry, offering a wide range of sheet metal options and value-added services like custom design and fabrication.
While selecting the right manufacturing partner can be daunting, we have a guide to help you choose.
Contact Us to Discuss Your Next Commercial HVAC Project
Ready to make the best material choice for your HVAC system? Contact Dahlstrom today to learn more about our products, and services, and how we can help you achieve superior HVAC performance.
You May Also Like
These Related Stories
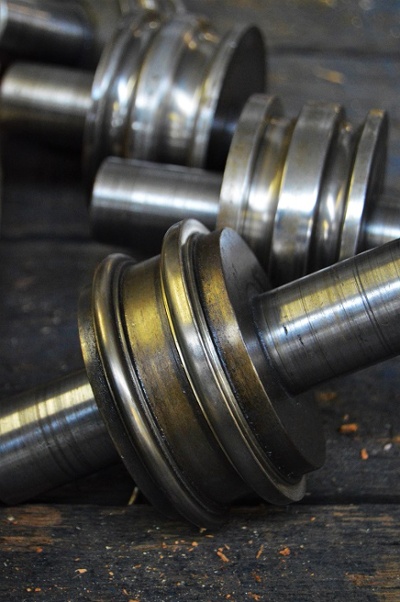
Sheet Metal Roll Forming: Assessing Cost, Ability, & Quality
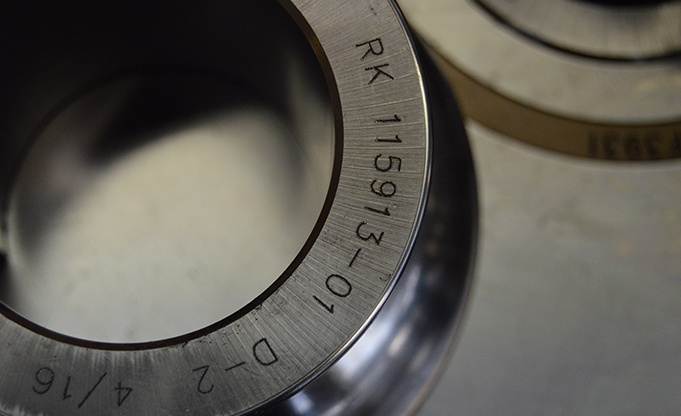
Want to Lower Sheet Metal Forming Costs? 5 Ways Roll Forming Can Help
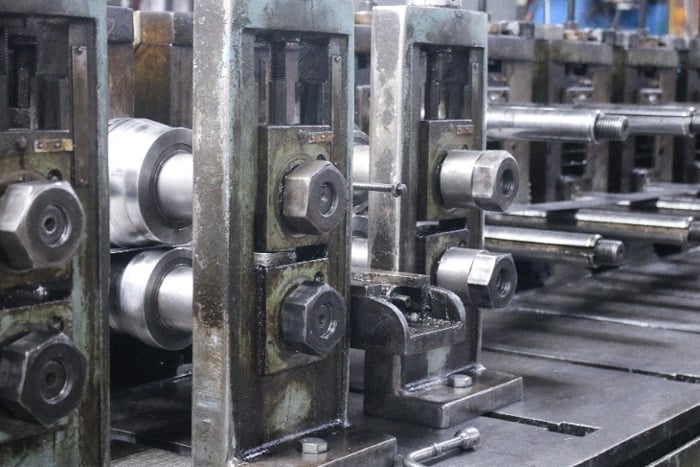