Sheet Metal Components: 7 Roll Forming Design Flaws to Avoid
Ever dreamt of creating the perfect sheet metal components, only to have your design go off the rails during roll forming?
As with any manufacturing process, careful design of your sheet metal components directly impacts your bottom line, production speed, and overall quality.
It's crucial to avoid common design flaws such as small bend radii, excessively short flanges, and wide curves. These elements challenge the manufacturing consistency and functionality of parts. By proactively addressing these design issues, custom metal component manufacturers can streamline production and achieve better outcomes and cost effectiveness.
This approach not only saves money but also enhances the manufacturability and integrity of the final product.
Here are 7 flaws you'll want to avoid:
ROLL FORMING DESIGN: 7 FLAWS TO AVOID FOR SHEET METAL COMPONENTS
Roll forming design can go off the tracks quickly and lead to many costly mistakes. The most common design flaws to be on the lookout for include:
- Small bend radii
- Extremely short flanges
- Wide, curved shapes
- Blind corners
- Narrow openings
- Deep, vertical sections
- Shapes with high anti-symmetry or a long, flat un-formed side.
Need Help Designing a Great Roll Formed Part?
To learn more about designing great roll formed parts, check out our free e-book below:
1. Small Bend Radii
The Problem: Tight corners can cause cracking in heavy-gauge, galvanized, or pre-painted materials due to stresses generated on the outer fibers of the bend. They also increase tool wear and breakage and require a mill with greater horsepower (all of which affect your costs).
The Fix: Allow for a minimum radius of 1.5 to 2x the material thickness for best results. Or, consider whether a more ductile material can be used to produce your component.
Watch Dahlstrom Roll Form president Robert White explain roll forming metal using a roll form mill to shape material.
2. Extremely Short Flanges
The Problem: If your flanges, or legs, are too short, they will not form properly and the roll forming process will be more difficult.
The Fix: Allow for at least 3x the material gauge as a minimum flange length. Longer legs provide more leverage to bend heavier materials.
3. Wide, Curved Features
The Problem: Since a sweeping bend (think half-pipe) may not stress the material beyond its yield point, it can be a difficult shape to control and is more prone to springback.
The Fix: Design for flat sections with discrete bends to reduce roll forming tool design costs and initial setup scrap. Or, consider a material with lower yield strength to ensure that curve holds.
4. Blind Corners
The Problem: Also called “air bends,” blind corners occur when the roll forming dies cannot contact both the inside and the outside of a formed corner. These bends are less accurate and more difficult to control throughout the forming process.
The Fix: Design your component to avoid this situation completely -- make sure the part will be in contact with inside and outside rollers at all times.
5. Narrow Openings
The Problem: Narrow openings (in relation to the overall size of shape) make designing cutoff tooling extremely difficult. They can also result in frequent roll die maintenance and cutoff die breakage.
The Fix: When designing your roll formed part, allow for more than half of the section width for your opening.
6. Deep, Vertical Sections
The Problem: These designs require large-diameter forming dies, which increases the cost of tooling. These components might also be "partially" formed via roll forming, then finished in a brake-press as a secondary operation.
The Fix: Make the flat section wider, or open the sidewalls at an angle. If you absolutely require a deep, narrow channel, ask about MeshTrim.
7. Wide Shapes with an Un-formed Edge
The Problem: Sheet metal components with high anti-symmetry or a long, flat un-formed side are unbalanced and incredibly difficult to keep from twisting or rippling.
The Fix: Add a small leg on the un-formed edge or introduce a stiffening rib for greater overall strength and consistent formability.
What else WILL make your Sheet metal components design better?
A great design also includes tolerances that are tight enough to meet the expected quality range and part function, but broad enough to allow the manufacturer to succeed. As with all part designs, tighter tolerances usually lead to higher costs associated with the tools needed to control them.
While we've provided guidelines on what to avoid, all of these features CAN be overcome through:
- Smart roll forming tool design
- Collaboration with your roll form partner
- Appropriate metal specification control
- The proper roll forming equipment
WhY Collaborate With a Roll Forming Partner Early in the Design Process?
Collaborating with a roll forming partner early in the design phase of your sheet metal components offers several benefits:
- Identify potential issues: An experienced manufacturer can identify design flaws early on, saving you time and money on revisions later.
- Optimize for roll forming: They can suggest design modifications to improve manufacturability and potentially reduce production costs.
- Material selection: They can advise on the most suitable material for your design and roll forming process.
- Cost considerations: Early collaboration allows for discussions about potential cost implications of design choices.
Ready to Work With A Sheet Metal Manufacturer?
By avoiding the design flaws outlined above, you've taken a great step towards roll forming success. However, collaborating with an experienced custom sheet metal parts manufacturer is key to achieving optimal results.
A qualified partner can offer valuable insights during the design phase, helping you refine your concept for efficient roll forming. They can also advise on material selection, tolerances, and potential cost-saving opportunities.
Contact Dahlstrom Roll Form today to discuss your project and explore the possibilities of roll forming for your sheet metal components.
(Editor's note: This article was originally published in January 2016 and was recently updated.)
You May Also Like
These Related Stories
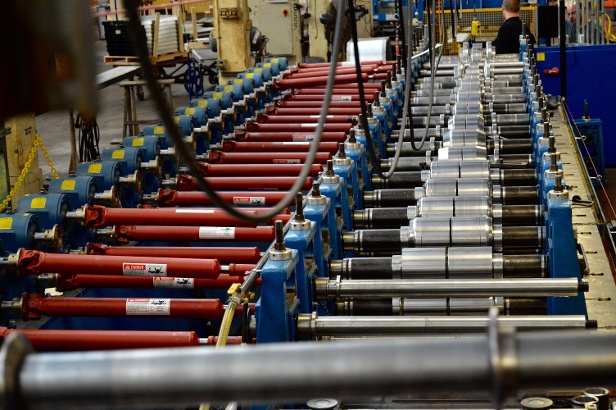
A Metal Roll Forming Partner Mustn't Be Big to Boost Your Business
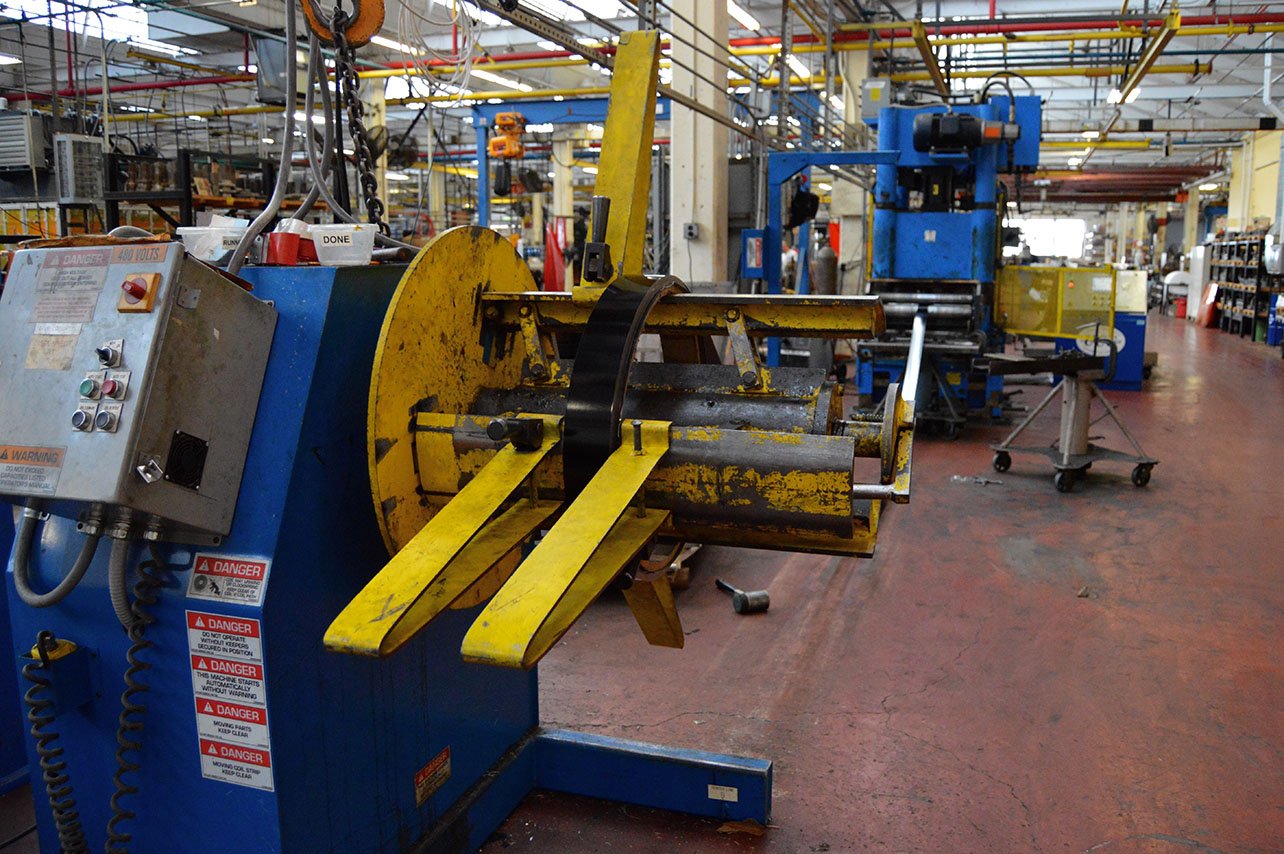
Supply System/Manufacturing Process Improvement Example: Roll Forming
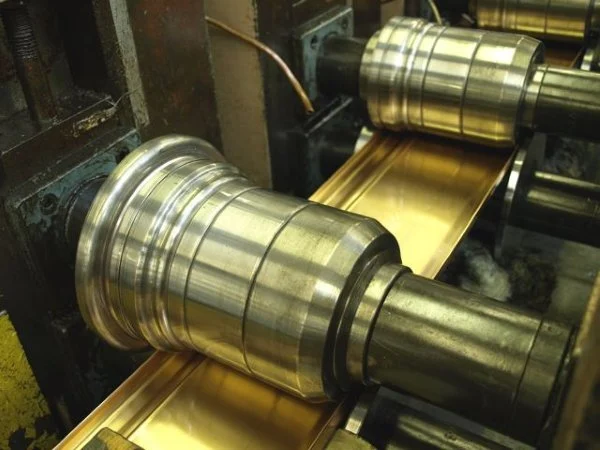