Roll Forming Design Guide for Sheet Metal Components
People not familiar with roll forming usually need some education regarding the machines’ capabilities and limitations – even people who regularly work in sheet metal roll forming. There’s a reason skilled roll form engineers are a coveted resource – this is complicated stuff.
If you want to get your project off to a good start, you should probably know… what can a metal roll forming machine handle? Most folks understand material thickness is an important factor, but that’s only the beginning.
Roll Forming Design Guide: What Can a Machine Handle?
In the roll forming process, a strip of metal is fed through a series of mated roll dies that are installed onto the shafts of a mill’s forming stands. If component pre-forming is required (holes, slots, cutouts, tabs, etc.), your manufacturer needs a punch press or other equipment. Some features are better introduced prior to forming, while others can be handled after forming.
If the component is being produced from coiled strips (as opposed to blanks, or pre-cut strips), the roll form line will typically include a cut-off press or saw. The ability of the roll form line – the coil feeder and pre-punch equipment, roll form machine, and cut-off equipment – to handle your component design depends upon many factors. If we look simply at the profile (cross-section) of the component design only, the key factors include:
- Material thickness
- Material type
- Profile size
- Profile complexity
Let’s look at some of the typical design characteristics of a roll form machine. The fit between the component design and the ability of a roll form machine (or mill) to form your component are linked to these characteristics:
- Roll shaft diameter
- Roll shaft space
- Roll shaft spacing (vertical, in particular)
- Number of forming stations
- Cut-off equipment
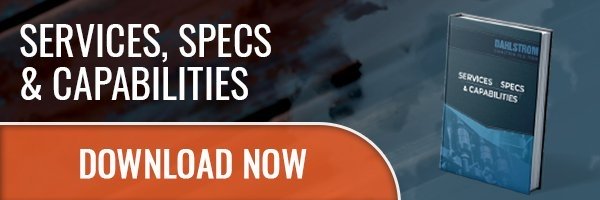
1. Material Thickness
Typically speaking, as material thickness increases, you’ll need a larger roll shaft diameter for the mill. As an example, Dahlstrom can form material thicknesses ranging from 0.012” to 0.200”, using mills with roll shaft diameters that range from 1.500” to 2.563”.
That being said, if sheet metal parts have few bends or are particularly narrow, the shaft diameter won’t need to be as large as is typically required.
2. Material Type
Does the metal alloy factor into your roll forming thickness limits? You bet.
Roll form equipment capabilities are typically measured by their performance on mild steel, which has a relatively low yield strength. So in general, as the yield strength of the material increases, the level of profile complexity a particular machine can handle decreases.
Materials with higher yield strengths and more springback (stainless steel, structural steels, HSLA steels, etc.) require more work to be formed. Materials with low yield strengths and less springback (metals including aluminum, red metals like bronze, brass, and copper, etc.) tend to require less work.
Not only that, but it’s also critical that the forming machine has the tonnage (force) required to cut your part off at the end of the line. To ensure success, you’ll need to know the range of the material’s yield strength. A strip of stainless steel might take twice as much force as the same length of mild steel, so don’t overlook this when talking with potential suppliers.
3. Component Size
The size of a component also plays a role in determining if it can be run on a given roll form line. This will vary by contractor, so don’t assume your component is one-size-fits-all.
Prior to forming, the strip width of the metal required to produce your profile is a significant factor. If the strip width is narrower than the roll space of the shafts, the profile is a candidate to be run on the line.
During and up until the profile is formed, the profile’s final height needs to be somewhat less than the vertical roll shaft spacing. Otherwise, the mill can’t successfully run your profile. And don’t forget that as the profile shape gets taller, the number of forming stations needed to produce that component increases.
4. How Complex is the Profile?
More bends dictate more force.
The complexity of the component’s cross-section is another consideration in pairing a roll form mill’s capability with the production of a particular component.
In general, the more bends a profile has, and the more dramatic those bend angles are, the more forming stations you’ll need. One extreme example would be an angle profile with relatively short legs (a single 90° bend angle) requiring only a few passes of tooling. On the other end of the spectrum would be a complex profile with 12 or more bends, including hem (180°) bends, requiring at least 20 passes of tooling and forming stations.
The number of bends in your component will ultimately determine your roll forming tooling design -- and the associated costs.
Results May Vary
Rolling sheet metal effectively comes down to the amount of work required per station, as a function of material thickness + metal type + part shape + part size vs. the physical make-up of the roll form machine.
Of course, it’s not on the customer to know every shred of detail of how sheet metal rolling companies do metal fabricating. But it is important to make sure your roll forming partner has the machine capability to do what you need it to.
Certain roll forming companies specialize in thick, heavy metal products. Then there are companies that only work on smaller, lighter, and faster stuff. Others dabble in both ends of the spectrum and everything in between.
Some machines are set up only to produce a very specific profile. Some companies limit themselves to structural roll forming with half-inch-thick roll form steel plate. Some companies stick to roof paneling with ultra-thin and extra-wide profiles.
So when you are selecting a roll form partner, it all comes down to your goals and its available machinery.
Setting up for Success With Roll Forming Services
If you’ve specified a tight-tolerance part, a wise roll former will configure the line so there's less work per station. If it’s an easy structural part, we’ll do more work per station.
If you have 20+ passes, you have the opportunity to create more complex parts.
Check with your roll formed parts supplier to learn:
- The types of lines they have
- The number of passes (forming stations) each line has
- The tolerance limitations for each line
- Their ability to pre-punch holes and other features on your part in-line
When it comes to roll forming design, more information you supply to your manufacturer, the more capable their machines are. The more experienced the manufacturer's engineers are, the happier you’ll be.
But that doesn't mean you should rely totally on your vendor – the free e-book below will help you design parts for manufacturability and cost-effectiveness:
(Editor's note: This blog was originally published in July 2020 and was recently updated.)
You May Also Like
These Related Stories
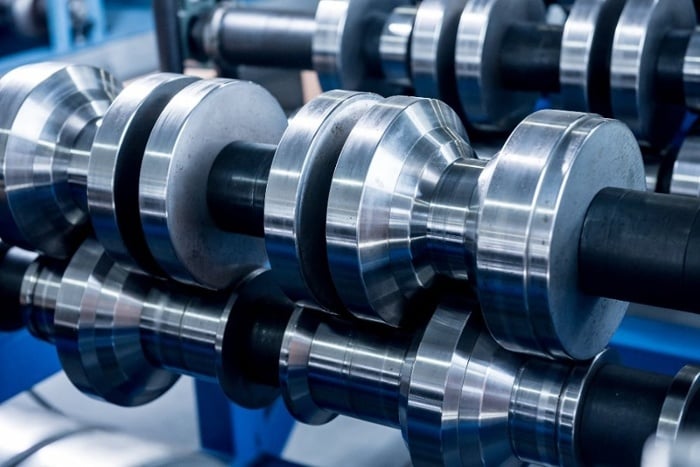
Custom Roll Forming Processes: Cold Roll Forming Steel
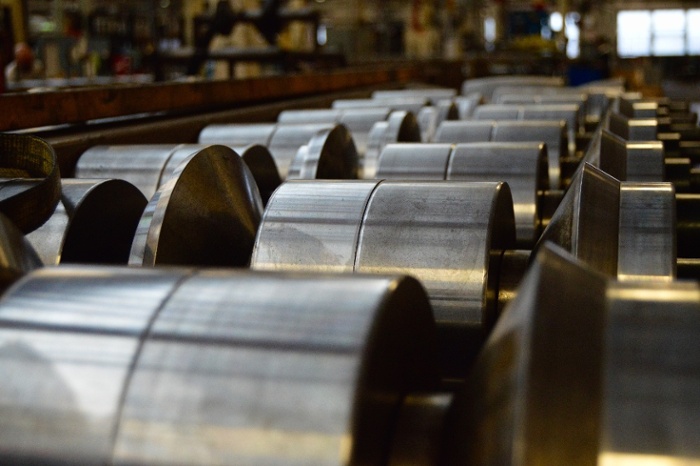
The 4 Most Common Myths of Roll Forming Metal
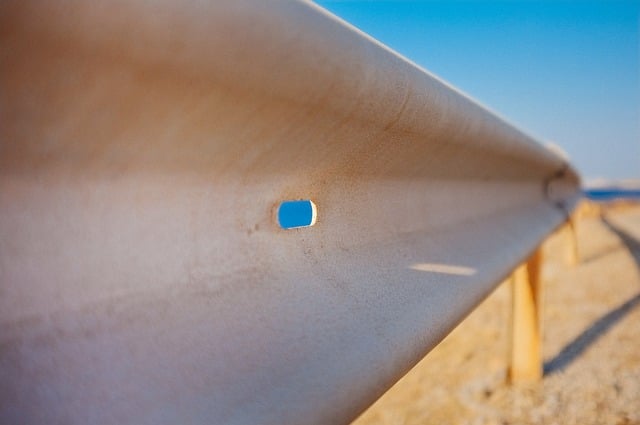