6 Important Factors in Manufacturing a Solar Racking System
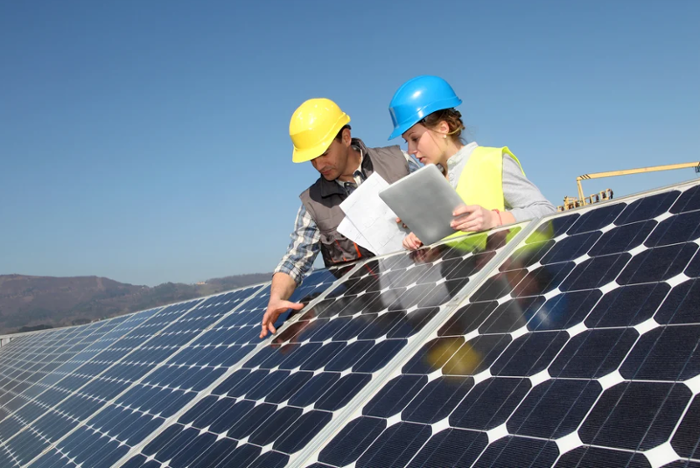
Solar energy is thriving in the United States, fueled by an impressive 24% average annual growth rate over the past decade.
Experts anticipate this upward trajectory to persist in the coming years, solidifying solar power's position as a mainstream energy source. Roll forming technology has played a pivotal role in this transformation, enabling solar installers to construct expansive solar panel arrays efficiently.
To further propel the growth of solar energy, cost-effectiveness remains a crucial factor. One key strategy involves developing solar panel mounting rack systems that balance affordability and durability, ensuring reliable support for these green energy generators for years.
Essential factors in manufacturing a successful solar racking system include:
- Raw material control and availability
- Ability to scale from small to large projects quickly
- Variable fastener punching patterns to accommodate different solar panel designs
- Component design in anticipation of new solar panel types and sizes
- Pre-kitting fasteners and components to consolidate the number of various parts on-site
- Packaging that allows easy handling and component access on-site
WHY ROLL FORMING FOR SOLAR RACKING SYSTEMS?
A roll forming company can maintain standard or customized systems by producing a variety of solar panel mounting hardware, like:
- Robust hat channels
- C-channels
- Z-purlins for utility-scale solar farms
- Lightweight ballast trays
- Ground mounted solar kits
- Solar panel roof mounting systems
Roll forming gives you:
- Proprietary designs
- Large volumes
- Specialized materials
- Critical hole placements for field assembly
Solar products are typically made from stainless steel, galvanized steel, aluminized (hot-dipped) steel, or nearly any other type of metal.
Resource: Need to get a handle on roll forming costs for solar racking systems? Download our comprehensive guide:
1. RAW MATERIAL CONTROL & AVAILABILITY
Solar is a project-based industry and requires a replenishment system that can handle variations in customer demand. A customer may need a lot of metal in just days’ notice, then not need any further orders for months.
Suppose you request 500,000 pounds of steel, and the roll form company purchases and holds this in stock. You use and purchase 50,000 pounds at once, and the vendor stores the rest of the steel. Who’s on the hook for the 450,000 pounds left over? To avoid disputes, it’s best to employ:
- Supply agreements
- Regular communication
Supply Agreements
Don’t wait until vendor or supply problems arise to find solutions. There are parameters you and your roll forming company should anticipate and agree to ahead of time. A supply agreement can save you a lot of headaches in the long run. The contract should cover:
- All operating steps
- Responsibilities for both parties
- Purchasing and inventory agreements
- Payment terms
- Freight terms
- Actions on quality problems
- Necessary legal protections
Communicate Regularly
Project-based supply systems require constant communication between the customer and roll forming company. Alongside a well-crafted supply agreement, regular meetings will help both parties handle the ebbs and flows of solar panel mounting rack manufacturing.
It can be difficult to project how many pieces you may need your roll former to produce due to the unpredictability of the solar market. Companies wishing to cash in on solar tax credits may demand more at certain times than others. You may go from needing 5,000 pieces to 300,000 pieces.
Constant communication allows you and your roll former to adapt quickly and smoothly. Create an agreed-upon communication schedule and be prepared with well-thought-out questions.
2. ABILITY TO SCALE FROM SMALL TO LARGE SOLAR PROJECTS QUICKLY
The unpredictability of the solar industry means that installation companies and roll formers need to be able to adjust, which may require:
- Roll formers adding shifts
- Customers buying an extra set of tools
- Working with one vendor vs. multiple
Roll Formers Adding Extra Shifts
Shift work allows roll formers to scale quickly from small to large projects. Adding a second shift means production doubles. A third shift would have production running around the clock.
Ensure your roll forming supplier can take on your work, even during demand spikes.
Customer Buys an Extra Set of Tools
Buying an extra set of tooling means you’d be able to run two production sets concurrently. Combined with added shifts on the roll forming side, this drastically decreases production time.
Buying an extra set of tooling can be expensive, but the long-term savings may outweigh up-front costs. It may be worth your investment if you regularly deal with high volume and a single roll forming vendor.
Working With One Vendor vs. Multiple
There are disadvantages and advantages to working with multiple roll formers. Working with more than one vendor can allow for more creative thinking, storage, and production capacity.
However, using more vendors means more oversight on your part. This can get especially tricky when production needs are high and time is short. Communication tends to get twisted as you approach “too many cooks” status.
3. VARIABLE FASTENER PUNCHING PATTERNS TO ACCOMMODATE DIFFERENT TYPES OF SOLAR PANELS
As the solar industry continues to evolve, so do the types of fasteners needed for solar panel frames. The design of solar panels will determine the type of fastener you need. Choosing the best one made from the correct metal will uphold the structural integrity of your solar mounting rack system for years.
The production method of solar fasteners may change per job as your vendor needs to account for different types and sizes of fasteners. Your roll former should build its process to support that.
Using roll forming to punch patterns into metal is an efficient and cost-effective way to create the variable patterns your job requires. Other metal-forming processes require multiple steps at different machines.
If the metal is going through the roll forming line, you might as well realize the time and money savings of adding features in-line!
4. COMPONENT DESIGN IN ANTICIPATION OF NEW SOLAR PANEL TYPES & SIZES
It’s necessary to anticipate industry trends. New solar panel sizes and types continue to come into the market. These changes will require differently sized components for each solar-power system.
Communicate with your roll former and ask what changes can be made to parts. This will allow you to stay on top of any tooling changes you may need to make.
Perhaps the solar panel mounting brackets need to be wider or narrower. Maybe you need different punch patterns. Talking with your roll forming company will help both sides respond to changing needs in your solar power mounting systems as they happen, ensuring there’s no lag in production.
5. PRE-KITTING FASTENERS & COMPONENTS
The solar industry seeks not only to be profitable but to provide as much or more power as conventional energy sources.
Solar panel rack mount kits come designed with all the parts you need to install rooftop or ground-mounted solar panels for residential and commercial projects.
Pre-kitting fasteners and components compress cost and time, making solar installation more efficient and affordable. This happens through:
- Eliminating the number of pieces needed for installation, making the process easier to control and erect
- Creating easy-to-assemble kits that involve few to no tools
- Preassembling components at the factory before shipment
6. PACKAGING THAT ALLOWS EASY HANDLING & COMPONENT ACCESS ON-SITE
Packaging may not be at the forefront of your mind, but it’s vital to efficiency. Improper packaging leads to tedious unpackaging and broken components, which drives up project time and costs.
The best packaging provides safety for components and allows the installer to open the box to easily find the first item they need. No one wants to open a package and dig around to find the first piece they need. Simplifying installation steps saves solar installers time and money.
ROLL FORMING SUPPLIERS CAN KEEP PRODUCTION COSTS LOW FOR SOLAR RACKING SYSTEMS
The demand for green energy continues to grow, and so does innovation in designing solar panels and mounting products. Work closely with your roll forming partner to produce solar racking systems that keep up with industry trends and will last for years.
Your roll forming supplier can keep production costs low by working with you on inventory management, scaling up projects, creating custom designs, and more.
Are you curious about how roll forming can help your solar racking projects? See our services and capabilities:
(Editor's note: This article was originally published in December 2021 and was recently updated.)
You May Also Like
These Related Stories
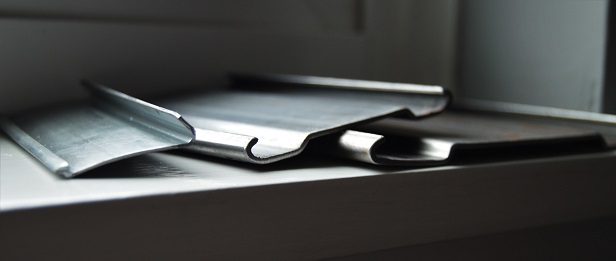
So You're Installing Commercial Metal Trim Moulding ... Now What?
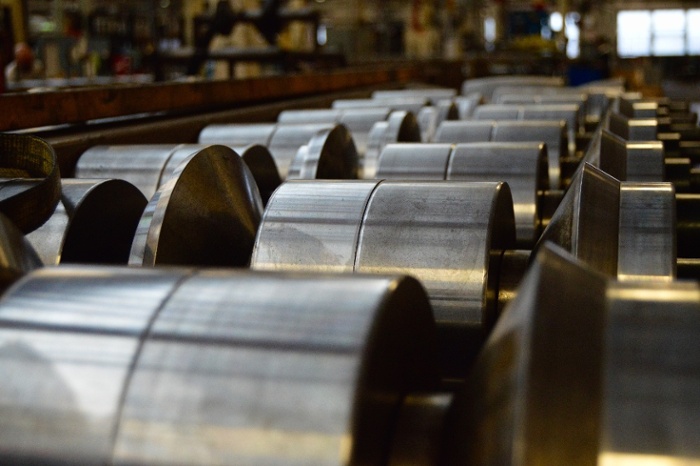
The 4 Most Common Myths of Roll Forming Metal
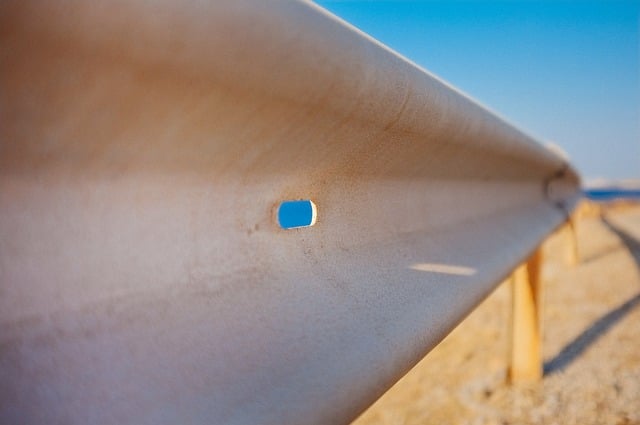