Factors of Corrosion: 7 Ways You're Begging for Trouble
When you invest in metal materials, you expect them to last. But it’s a mistake to assume metal is immune to degradation from environmental and other factors. Corrosion can wreak havoc on the structural integrity and aesthetics of your parts. That’s why it’s important to know the factors of corrosion -- where it occurs most and what promotes it.
Armed with this knowledge, you can account for corrosion when planning your next project.
Factors of Corrosion: What Promotes It & Where to Find IT
1. Welding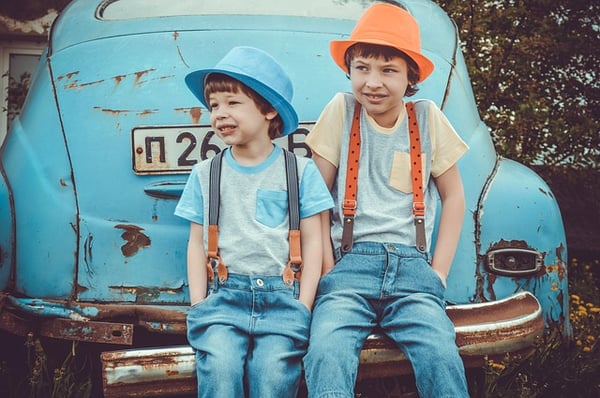
Welding is the best and most popular way to permanently attach two pieces of metal. But it also creates an environment where corrosion can set up shop and go wild.
Every weld creates stress -- we mean in the metal, not the welder. Stress disrupts the structure of metal in ways that allow corrosion to occur.
You can see examples of welds leading to corrosion in old chrome bumpers. They always rust where the deepest part of the draw is.
Fortunately, you can often achieve the structural changes you need with shorter, intermittent welds. Instead of welding continuously, weld a bit, skip a bit, and then weld a bit more. You will not only provide fewer footholds for corrosion, but also save on consumables like rods and wire.
2. Edges
Cutting also stresses metal, even when cuts are perfect. The stress lets corrosion seep in, which is why you often see rust seeping in from the edges of cut steel.
Holes are susceptible to this as well. After all, they’re just circular edges.
3. Metals That Don’t Play Nice Together
When you build a product using two different metals, one metal will always corrode before another. It’s always wise to consider corrosion when choosing which materials you use together, otherwise you may get results that aren’t pretty.
Say you were going to build a shed using steel with aluminum rivets. The rivets would corrode and fail after a few years and cause the shed to collapse. Not good.
Some things to think about:
- You can use the anodic table to research which metals corrode faster than others.
- The biggest problems come from two totally different metals touching one another. But even the same metal’s various grades can be at odds with each other.
- You can actually use a fast-corroding metal to “take the bullet” for a more slowly corroding metal. This is put into practice on boat motors, where magnesium or zinc “pucks” are placed as a protective barrier.
4. Bends
Bending also creates stress in metal materials. The surface near the radius of the bend will start to corrode first. Stress disrupts the matrix structure of metals down to the molecular level. Processes like bending open up that structure, which allows corrosion to rear its ugly head.
Dents in cars are a good example of this -- yes, part of the rust is due to the loss of paint during a collision, but part is also due to the newfound stress in the metal caused on impact.
5. Heat
As pointed out by the Department of Physics at the University of Illinois, heat typically increases the rate of chemical reactions. That’s why hot iron rusts more rapidly than cold iron.
You can see an example of this when looking at car mufflers. Unless they are made out of non-rusting or coated materials, they tend to oxidize more quickly than other parts of the car.
6. Salt
Salt is a big problem for metals, which is why building in marine environments requires extra care and attention.
Electrolytes in humid air carry ions released from the metal. The more corrosive the electrolytes, the faster your corrosion. Salt accelerates the process.
In the worst environments it can take as few as three years for galvanized steel to begin rusting.
7. Other Airborne Stuff
Aerosol particles like dust can cause corrosion, but there are harsher pollutants out there that can cause more damage.
Sulphur dioxide, which comes from fuel combustion, can wear down metals. Nitrogen oxide is another pollutant that accelerates corrosion.
Consult with an Expert Manufacturer
With so many material options and corrosion factors to consider, it can help to consult with someone who knows the ins and outs of metal manufacturing. If you have questions, don’t hesitate to contact your metal manufacturer to discuss how corrosion may affect your next project.
A smarter decision in the design stage can add years to your components’ lives!
You May Also Like
These Related Stories
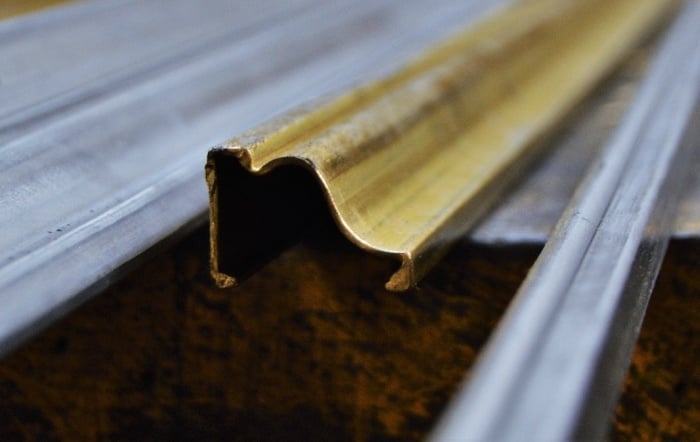
The Very Most Corrosion-Resistant Metals
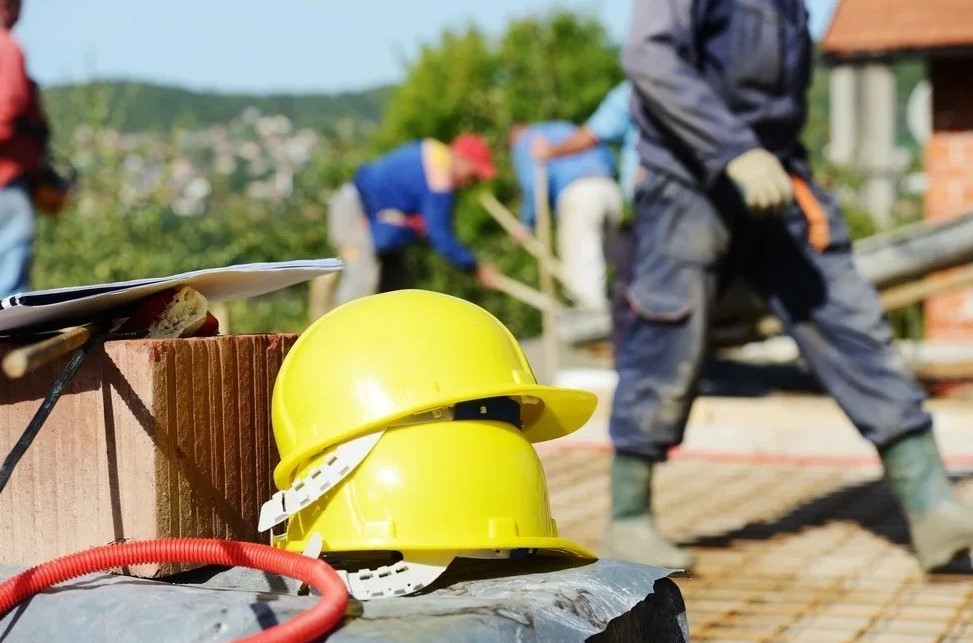
5 Corrosion-Resistant Building Materials | Architectural Metal Design
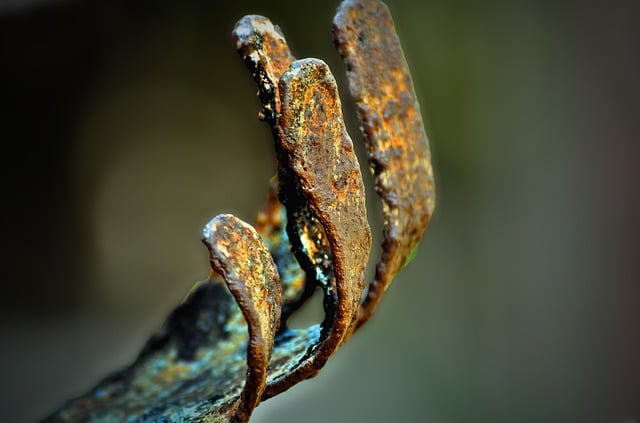