Intentional Corrosion Makes Old Architectural Finishes New Again
Being ahead of the hottest trends is what makes an already qualified and experienced designer stand above the competition. As many modern upscale home and business owners seek to revamp their spaces with materials beyond wood, they are considering the use of strategically placed metal to create impressive architectural touches. An up-and-coming trend with architectural finishes involves a process called intentional corrosion (or forced corrosion).
What Is Forced or Intentional Metal Corrosion?
Intentional corrosion of metal allows designers to take certain types of metal and transform them into vintage-looking pieces quickly.
Want to get that orange-brown rusty finish or enjoy a lovely blue-green patina on your metal accents? There’s no need to stretch the design budget buying true antique pieces or waiting for nature to take its course if you are knowledgeable about the process of intentional corrosion. As a newer innovation in design techniques, requesting this rising trend can put you at the top of many high-end residential and commercial customers’ consultation list.
Corroded Metal: Aesthetic Applications in Architectural Finishes
Those looking to add uniqueness and contrast by embracing a few touches with a vintage look will appreciate the ease of corroding metal for use in architectural designs. Because these implements are attractive and unusual -- and fire-retardant -- their use is ideal for:
- Hotels
- Retail spaces
- Restaurants
- Other public and commercial spaces
- Houses and apartment buildings
Depending on the client and the location’s primary purposes, corroded metal applications and mouldings can be employed in a variety of places, including:
- Decorative metal trim applications, such as baseboards and crown mouldings
- Door knobs, knockers, and door casings and frames
- Window casings and rails
- Picture rail mouldings
- Accent pieces for interior and exterior use
The vast possibilities using intentional corrosion amid architectural finishes are only limited by one’s imagination. With such a wide array of functional and aesthetic uses and benefits, you might be wondering which metals work best for intentional corrosion ...
Choosing the Right Metals for Forced Corrosion
Several metals are ideal for intentional corrosion:
- Red metals like copper, brass, and bronze
- Iron
- Zinc or zinc coated steel
- Carbon steel
Options to avoid in general are those such as stainless steel or aluminum, which might not take as well to the process as affordable carbon steel will. Why would you pay all that money for stainless steel only to tarnish it, anyway?
The bullet list of metals above give you plenty of options for color. Now let’s look at the process itself.
Intentional Corrosion Process: DIY or Hire a Pro
With a basic combination of household chemicals or specialty all-in-one solutions available from certain suppliers, your contractor can follow these tips and DIY directions for forcing the corrosion process:
- Clean the metal thoroughly to remove debris and oil.
- Heat the metal before application for faster results (room temperature also works).
- Simply apply the material solution of your choice and watch it work its magic.
- Rinse the chemicals off.
- Apply a matte clear polyurethane solution to seal the finish.
This technique is still evolving as a trend, so very few companies can do the process for you. Dahlstrom isn’t finished with an internal corrosion finishing process quite yet, but we have relationships with experts who are already mastering this practice. So, get in touch with us and we can start you on the right track. You can also look forward to some really cool additions to our offering in the near future!
You May Also Like
These Related Stories
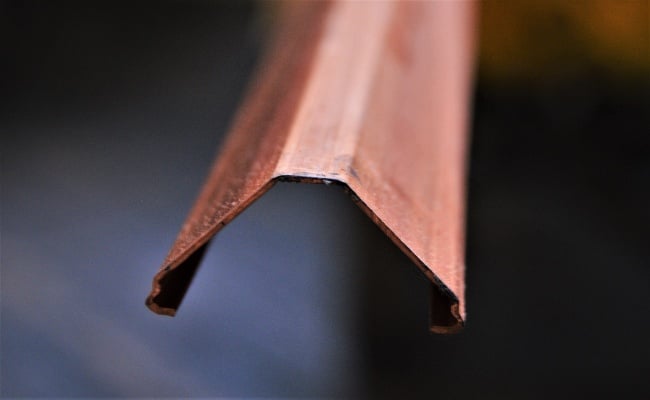
A Vendor Can Take Your Architectural Metal Mouldings to Another Level
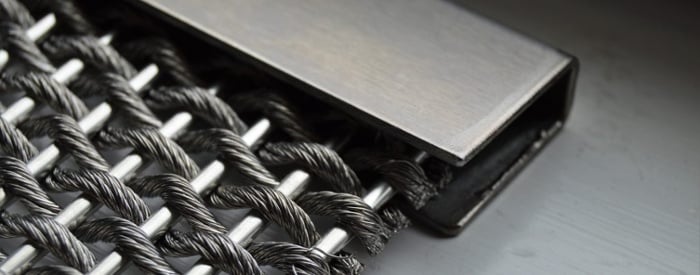
Architectural Wire Mesh & Perforated Metal Panels: 3 Benefits, 10 Uses
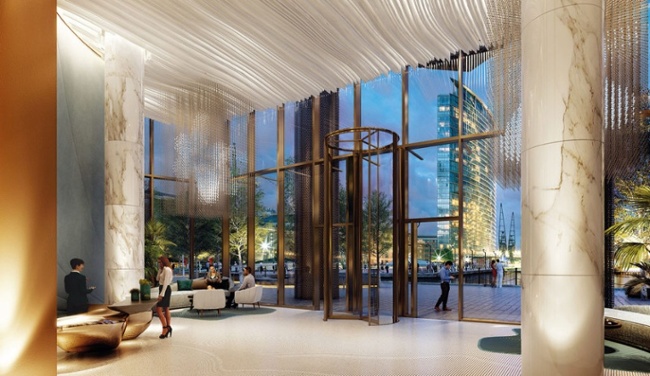