How Does a Corrosion Test Work?
Engineers seek out corrosion testing as a way to scope out a problem before shooting with live rounds, so to speak. A corrosion test helps you understand how long a fabricated metal item will hold up under tough conditions.
Those conditions include:
- High temperature
- High humidity
- Presence of salt (whether in coastal waters or on roads in cold-weather regions)
There are plenty of reasons to conduct a corrosion test and plenty of ways to do it. Let’s investigate.
Why Bother With a Corrosion Test?
You should use corrosion testing to qualify which material (or chemical, if your heart’s already set on a specific metal) makes sense for your intended use. The real point of the test is to save yourself a buttload of trouble later.
Corrosion can render your metal damaged beyond repair. Beyond bruising your ego, this failure could result in:
- High repair costs
- Safety risks
- Production downtime
- Damage to your professional reputation
If you’re creating a product that’ll sustain heavy environmental abuse, it’s comforting to pre-emptively factor the impact of corrosion into your design process. It’s also cost- and time-efficient. Why wait years to see if your product will corrode when a corrosion test can tell you in days?
Additional uses of corrosion testing:
- Evaluate protective treatments
- Evaluate whether the metal can endure your intended use for it
- Figuring out what’s causing or potentially causing corrosion
- Identifying why a product failed
Now, some popular examples of test methods:
Types of Corrosion Testing
Salt Spray Test
This is the most common form of corrosion testing. You may better know it as a salt fog test.
This process involves consistently covering your test subject with salt in a controlled spray chamber. The tester can adjust temperatures inside the chamber.
Temperature Test
This one is great for testing electronic products, which tend to overheat. Temperature testing is available in varying ranges, depending on the provider. Tests are available for both extreme heat and extreme cold.
Humidity Test
Also great for testing electronics, this one simulates a damp environment. Corrosion testing companies offer varying ranges of relative humidity for simulation.
Some companies build models specifically to test small components.
Passivation Test
Passivation testing checks the surface of corrosion-resistant steel by examining passivity. (Passivity = Unreactiveness thanks to an outer layer of oxide.)
The passivation process can remove rust-causing surface contamination and maximize stainless steel’s natural potential to resist corrosion. A properly passivated steel should be virtually rust-free
This test may also tell you whether you need a treatment or protective coating on your roll formed parts.
Cracking Test
Sometimes tests only look at a specific type of corrosion. This one determines what it takes for your material to crack under stress and in a rough environment. Naturally, to test a material for cracking susceptibility, you put it under a controlled amount of stress.
Cracking can be one of the most dangerous forms of corrosion. Cracking can lead to catastrophic failure of your component and put human life at risk. To make matters worse, unlike general corrosion, it’s difficult to detect without performing a little surgery on your product.
Our point: If your application is structural, this one’s a biggie.
Crevice Corrosion Test
This one helps predict your metal’s talents in resisting corrosion from trapped fluid.
To test for crevice corrosion, the tester clamps plastic washers to your samples, then throws them into the corrosive environment for a predetermined time. This creates artificial crevices. In a bad case, the crevices may penetrate your metal, causing it to fail.
Your tester can check the severity of localized corrosion by measuring the size and depth of these pits.
Your Roll Former As a Resource
An experienced roll forming company is going to know all about corrosion. It’s the #1 cause of headaches for many design engineers. The best roll forming companies can aid you in the design phase and make sure you’re not wasting time, money, or worse, someone’s well-being.
Need more info on the characteristics of certain metals? Check out this chart. Or, for exterior projects, read up on the new big thing in corrosion protection.
You May Also Like
These Related Stories
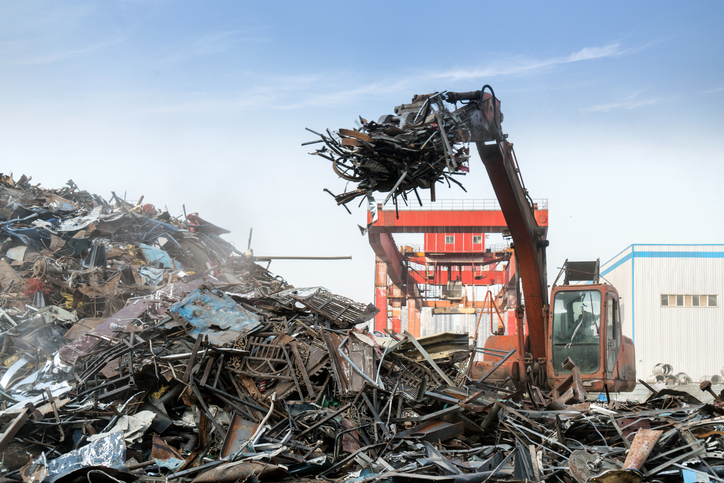
ECO-FRIENDLY INTERIOR DESIGN MATERIALS: IS STEEL SUSTAINABLE?
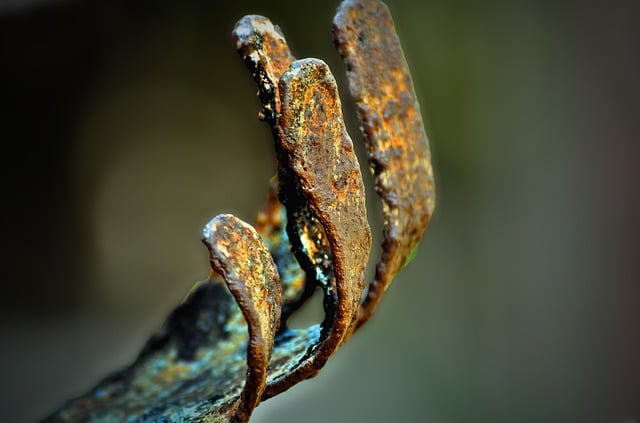
Intentional Corrosion Makes Old Architectural Finishes New Again
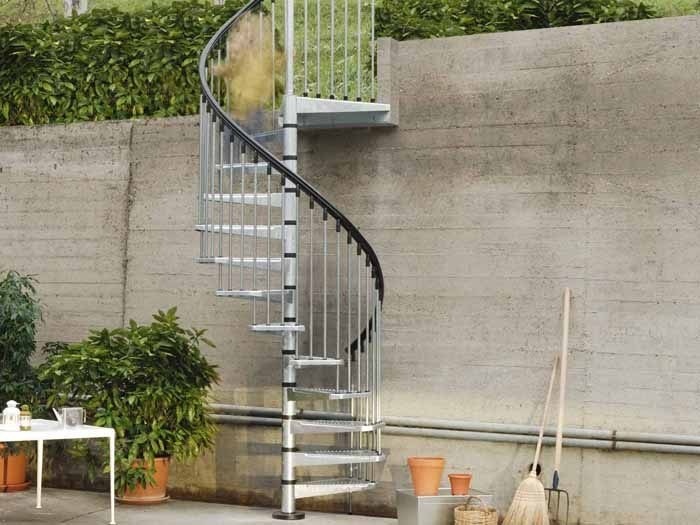