Try The Next Level of Economical Outdoor Metal Corrosion Protection
So, you want to make something out of metal, put it outside, and make sure it lasts a long time. Easy, right? Engineers have been doing that for centuries and having success. As you ponder your task you ask, “What are my choices?”
You need strength to maximize cost. In other words, you want to buy the least amount of metal possible, yet still create a strong design. You need the metal to be ductile enough so your manufacturer can form it. You want metal corrosion protection during all four seasons and along the coast.
Outdoor Metal Corrosion Protection: Your Standard Choices Considered
(Photo courtesy Archiproducts)
How about you use gold? It is highly corrosion resistant. In fact, it is the base for which all corrosion is measured in the Anodic Index. Unfortunately, for gold to be a good option, you’d need to A) win the lottery B) magically give gold the rigid strength you need for your project.
You could also try bronze or copper. They are beautiful and last for centuries in any environment. Copper and bronze alloys are also highly formable. But, again, they’re too expensive and don’t offer the strength you need.
“Stainless steel! That’s it!” you exclaim. Stainless steel is highly (very highly) resistant to the effects of all environments, including coastal applications and even caustic chemicals. But that darn cost again. … You won't need to win the Powerball, but you would need a few big payouts from scratch-off tickets!
Maybe you should go back to basics and explore galvanized steel. It has reasonable cost, strength, and a host of options to galvanize your finished product. It’s used everywhere today for outdoor steel construction:
- Highway guardrails
- Sign posts
- Chain link fencing
- Flat roof panels
- Roof solar panel racking
- Utility scale solar panel racking
- Outdoor bleacher framing
- Commercial building framing
Why recreate the wheel?
Next-Generation Galvanized Steels
Galvanized steel has come a long way in the last 25 years. As a refresher, galvanizing of steel is the process of coating steel surfaces with an anodic material that protects the steel’s qualities by sacrificing itself to the environment through an electrolyte solution (usually moist air). This electrical reaction protects the base steel. The better this combination is designed, the longer outdoor components will last.
Common galvanized steel uses zinc as protective coating.
1. Hot Dipped Galvanized Steel
The most common hot dipped grades are G30, G60, and G90. The G”xx” refers to the amount of zinc present per square foot. of surface (G60 = 0.60 oz/sq.ft.). They work well for most common applications where a secondary coating like paint is not used.
2. Galvannealed Steel
The most common galvannealed steel grades are A40 and A60. Galvannealed steel uses heat to help combine the coating with the base metal, which creates an etched matte finish that is ideal for painting.
3. Application-Specific Zinc Coating
Less frequent in the past but becoming more popular now is application-specific zinc coating. Specifying more zinc per square foot than available as a standard allows companies to design galvanized steel with the additional protection they need at a reasonable cost. Coatings as high as G120, G180, and G235 are available as special orders depending on the base metal’s thickness.
4. Galvalume
Galvalume is a type of galvanized steel that uses a combination of 45% zinc and 55% aluminum, both highly anodic, as the protection layer. Galvalume is more corrosion resistant than galvanized steel because the aluminum provides barrier protection in addition to galvanic protection from the zinc. Aluminum forms a natural oxide barrier which effectively protects the underlying metal.
Galvalume is another economical outdoor material that still retains the strength of steel and is commonly used for metal roofing.
5. Aluminized Steel
Aluminized steel is similar to Galvalume, but does not contain any zinc. It offers more favored qualities for food and kitchen products because it does not contain lead. (Though the lead content in zinc alloys is still considerably lower than even Restriction of Hazardous Substances limits).
Aluminized steel is also used heavily for heat exchangers since the heat conducting qualities of aluminum are excellent. Corrosion protection is similar to Galvalume. The cost is slightly high due to aluminum being more expensive than zinc.
6. ZAM
For the ultimate in cost-effective steel component protection, try ZAM. This product’s combination of Zinc, Aluminum, and Magnesium provides the ultimate in affordable protection. Their close proximity in the anodic index and their highly anodic properties provide superior protection for your steel surfaces.
Although ZAM may require higher order volumes and involve some replenishment barriers due to its scarcity, well thought-out supply chain methods will pay off with high product performance. The cost for ZAM is very reasonable considering the level of performance gained to protect your steel.
Understand Your Options
It’s OK if you’re still not sure what material you’re going to use -- but hopefully you understand your options a lot better. Cold rolled steel with a protective coating is likely your choice for the ideal combination of cost-effectiveness, strength, and durability.
If you need more information on these types of coatings, contact your steel fabricator of choice. They should be able to point you in the right direction.

You May Also Like
These Related Stories
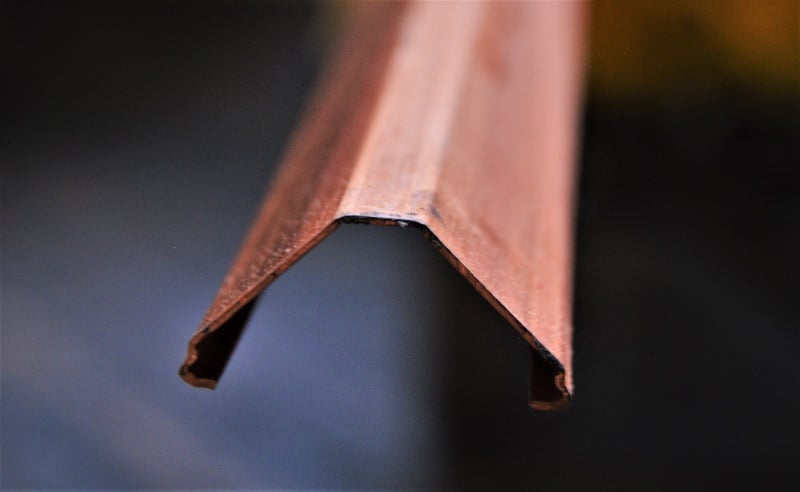
Metal Mouldings: Care and Maintenance

VIDEO: Wood Vs. Architectural Metal Mouldings Part 3 - Fire Test
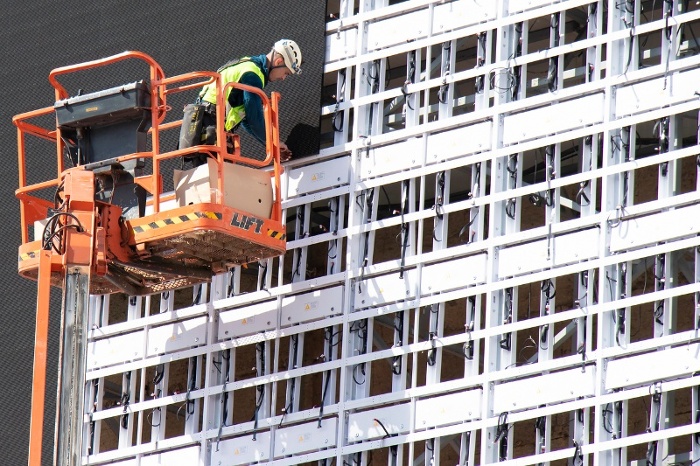