Galvannealed vs Galvanized Steel for Architectural Design
Galvannealed and galvanized steels start out similarly. They are both dipped into a hot zinc bath (approximately 850° F), so the zinc bonds to the metal's surface. This coating increases the steel's durability and protects against corrosion.
It's the introduction of a secondary process that determines how they differ after the roll forming process.
Galvannealed vs. Galvanized Steel
In order to know which steel you will want to use for your architectural metal design, you'll first want to know the differences between the two.
Galvannealed Steel
Galvannealed steel goes through an extra processing step. Once the raw steel is coated in zinc, it's then heated to a higher temperature (over 1000° F). This process pulls the iron from the steel, causing it to mix with the zinc coating. Consequently, the coating becomes harder, more scratch-resistant, and more uniform in appearance.
Galvannealed steel does not have a spangled appearance. The finish of galvannealed steel is flat grey with a matte texture.
Galvannealed steel bonds better with paint, and it’s better for welding.
- Architecture typically uses A40 galvannealed - .40 oz coating per square foot.
A40 is a thin galvannealed coating, providing surface protection while also retaining formability. If further protection is required, A60 galvannealed steel is available, but may be tough to obtain in smaller quantities.
Galvanized Steel
Galvanized steel receives the benefits mentioned above, as well as a unique appearance. The visual result of galvanization is a shiny, spangled surface, characterized by mottled light and dark gray patches.
The size and shape of the spangle-pattern can be controlled by the choice of zinc alloy, bath temperature, and cooling rate.
The most common galvanized steel variations seen in architecture are:
- G30 - .30 oz coating per square foot
- G60 - .60 oz coating per square foot
- G90 - .90 oz coating per square foot
Thicker coatings generally last longer, because they take longer to corrode. However, that means they also have decreased workability.
Which one is best for your project?
Consider two things: location and appearance.
If the metal will be used in exterior design, or in a damp or salty environment, you’ll want to consider using a tougher coating like G90. If it’s likely to be scratched or impacted, the harder A40 galvannealed finish is preferable. But if your application is mild, a thinner coating will suffice.
As for appearance, galvanized steel can certainly be painted, finished, or coated. However, their natural aesthetic is quite appealing for many designers. Spangle-patterns are unique to galvanization, and no two pieces will be the same.
The surface of galvannealed steel has a very slight, matte texturing. It is perfect for painting, because paint bonds well mechanically with this type of surface. If you prefer a painted metal, galvannealed steel will be more appropriate.
Architectural Metals
The metals used in interior design may differ from those used for exterior design. If you want additional information on architectural metals, their different finishes, and their role in architectural design, then download our free pocket guide:
Editor's note: This article was originally published in March 2017 and has recently been updated.
You May Also Like
These Related Stories
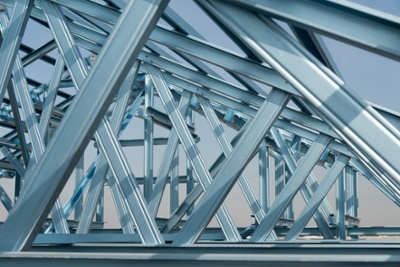
Galvanized Steel Vs. Stainless Steel in Architecture & Interior Design
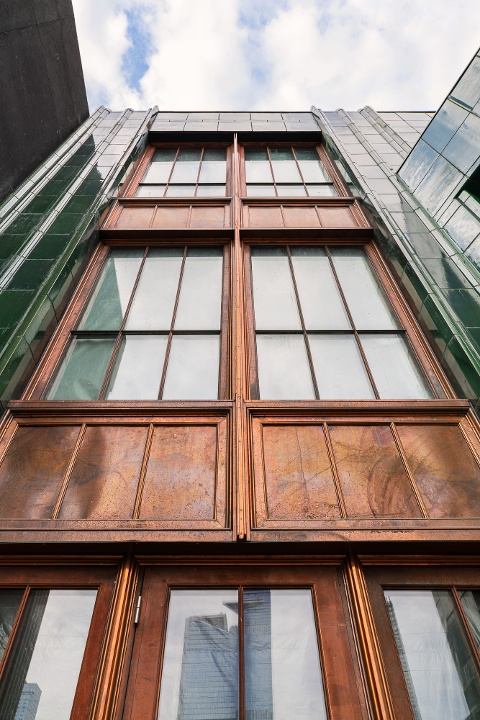
4 Surefire Decorative Metal Trim Buys That Are Timeless & Tough
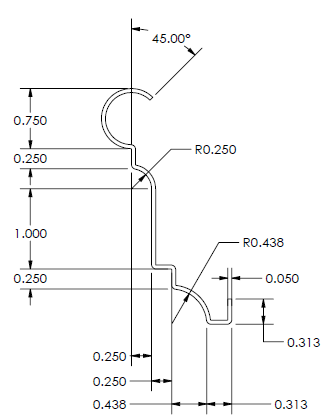