Architectural Building Materials: Does Brass Rust?
Brass is one of the great luxury metals, alongside copper and bronze. It’s considered to be an architectural building material that is classy and timeless -- or is it? Online, it seems everyone from 11th-grade science fair contestants to five-star hotel architects are stumbling on the same question: “Does brass rust?”
First off, know that brass is an alloy of copper and zinc. It’s bright, fairly hard metal, and shiny as heck. No wonder it’s beloved for its decorative potential and architectural metal design capabilities. (Plus it’s cheaper than gold.)
We mentioned brass is hard, but it’s still softer than bronze (an alloy of copper and tin). This comparative softness makes brass easier to cut, shape, and file..
With the basics of brass out of the way, let’s end the “rust" debate for good.
does brass rust, or is it a timeless architectural building material?
Well, depending on how you define “rust,” the answer is yes and no.
- Merriam-Webster defines rust as “the reddish, brittle coating formed on iron, especially when chemically attacked by moist, and composed essentially of hydrated ferric oxide.”
- However … Merriam accepts a second definition as well: “a comparable coating produced on a metal other than iron by corrosion.”
For another clue, turn to the elemental symbol for iron -- “Fe,” which is where you get the words “ferrous” and “ferric.” If a metal doesn’t contain iron, it can’t produce iron oxide (aka rust). So, brass can’t "rust" by the standards of Definition #1 above.
(Steel, on the other hand, does rust because it contains iron.)
This doesn’t mean metals besides steel and straight-up iron can’t corrode, too. Brass does in fact corrode -- it’s just not typically referred to as “rust” in conversation. That said, one could argue brass fits the criteria of Definition #2. Just know that corrosion doesn’t necessarily = rust.
One thing everyone can agree on: Brass will undergo a “patina” color-changing effect as it oxidizes over a prolonged period of time. This process accelerates the more your brass is exposed to the elements.
This naturally occurring film layer isn’t always a bad thing -- the blue-green hue is actually hugely attractive to many architects. The color of fresh brass can vary depending on the grade you select, meaning the patina color can vary a bit too.
Note that brass (and bronze) are a bit more resistant to the oxidation than copper, another frequently requested “red metal.”
Factors That Affect 'Rust' … or, Corrosion in This Case
Is your project going to live inside or outside? This makes a big difference for corrosion-resistant building materials, and a brass item sitting in a dry building is going to keep its luster for ages.
Is it going to be near water or roads that are frequently salted in cold weather? Brass living at freshwater lakes and rivers will break down at a much lower rate than brass residing near marine or otherwise salty environments.
Overall, brass loses its zinc component relatively quickly when submerged in water, causing the metal to weaken and putting its structural integrity at risk.
Outside of situations where it’s submerged in water, brass is a great metal for outdoor applications due to its amazing endurance. That rapid change to blue-green isn’t a sign of decay -- in the right conditions brass can last more than 1,000 years!
If you want the aged look of oxidized brass immediately, the process can be accelerated by applying commercially available solutions. For smaller, hobby projects, a mixture of 50% white vinegar and 50% salt water can do a nice job!
Learn About Other Architectural building Materials
You’ve learned a lot about brass and a little about its cousins, copper and bronze, but don’t stop there. There are tons of other options out there for improving your corrosion-proof project -- especially if you’re looking to spend a little less.
For more on other architectural metals (stainless steel, galvanized steel, etc.) and their ability to survive outdoors, grab the free e-book below:
(Editor's Note: This article was originally published in June 2018 and has recently been updated.)
You May Also Like
These Related Stories
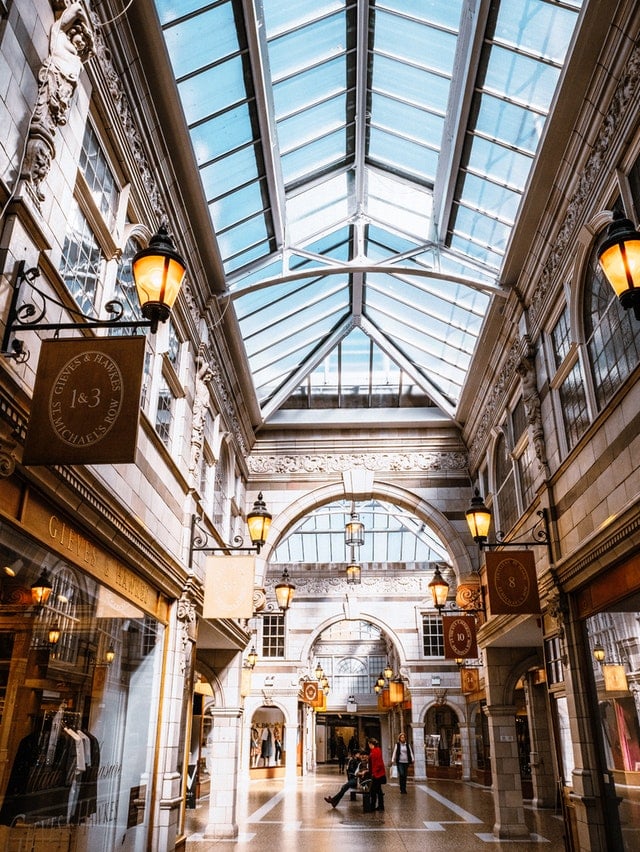
What’s the Environmental Impact of Brass Architecture?
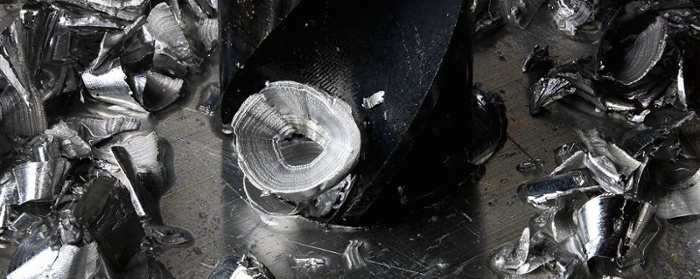
Choosing Your Aesthetic for Architectural Metal Mouldings
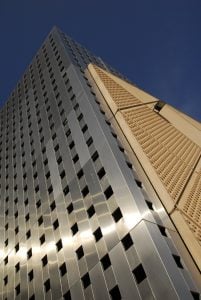