The 4 Most Common Myths of Roll Forming Metal
There are a lot of common misconceptions about roll forming metal. Four of the most common myths about the roll forming process include:
|
Metal roll forming is a process that uses pressure and heat to shape metal into specific shapes. It is often used to form steel profiles, and is considered a niche process because of the limited situations in which it can be used. Consequently, many people do not understand how it works and how to use it. This leads to misconceptions about the process and its capabilities.
Let's clear the air and address those misconceptions directly.
Dispelling the 4 Most Common Myths of Roll Forming Metal
Below are four of the most common myths about the roll forming process:
- Roll forming tools are "too expensive"
- The cost "isn't worth it" unless you have super-high volumes
- Roll forming "can't produce" high-precision parts
- Roll forming is primarily "just for" steel products
1. Roll Forming Tools Are Too Expensive
Tooling for any kind of metal fabrication can be costly. If you buy smart, roll forming tools are no more expensive than any other type of tooling. Here are a few ways to mitigate high tooling costs:
- If your manufacturer participates in part design, they may be able to save you money on tooling by optimizing the part for roll forming processes.
- Payments can be amortized over a period of time to avoid high up-front costs.
- Your manufacturer can discount or rebate the cost of tooling, in exchange for a commitment to buy a certain amount of parts over time.
At Dahlstrom Roll Form, our 100 years of experience comes with an archive of over 1,400 existing tool sets. We may already have tooling that will work for you, so you may not need to pay additional tooling costs at all.
2. The Cost Isn’t Worth It Unless You Have Super-High Volumes
Although high volumes are certainly the most cost-effective way to utilize roll forming, small and medium runs don’t have to break your bank.
First off, depending on your part design, volumes as low as 10,000 to 20,000 linear feet per year can be cost-effective.
Your manufacturer can also provide economic order quantity runs. These allow for inventory to be held by the manufacturer and distributed to you as needed. Economic runs maximize volume and reduce setup time, and you receive small as-needed deliveries.
Similar to offering discounted tooling in exchange for a long-term purchase commitment, your manufacturer may also be willing to discount your small roll forming orders in exchange for a longer-term contract.
Finally, roll forming may be the only realistic option for producing your part. In that case, it may not matter the cost - you’ll need to produce it anyway.
In any case, be sure to talk to your manufacturer about accommodations for your needs.
3. Roll Forming Cannot Produce Precision Parts
On the contrary, roll forming is quite precise as long as the manufacturer understands the quirks of the process.
Roll forming machines do produce end flare, and the metal will experience some springback. Your manufacturer should understand how these distortions can be controlled by part design, and the number of forming stations in the line.
Done correctly, roll forming can hold tolerances up to +/- 0.005” on certain profile segments. Overall part lengths can be accurate up to +/- 0.020”.
4. Roll Forming Is Primarily Used for Steel Products
While steel is the most commonly roll formed material, any ductile metal (or non-metal!) can be formed with this process. This includes:
- Copper
- Bronze
- Brass
- Aluminum
- Galvanized steel (G30 - G235)
- Galvannealed steel (A25 - A40)
- Pre-painted steel*
- Perforated metals
*Forming pre-painted steel will save you a secondary painting step. This helps to save on overall costs.
Pre-punched sheets that have gone through a turret punch press or a laser cutting center can be roll formed via hand-feeding of each sheet.
Roll forming is a cost-effective, flexible metal fabrication process
Roll forming can require a bit more maneuvering, but you don't need high volumes or loose tolerances to get your money's worth out of roll forming services. On the contrary, companies who use roll forming are usually very satisfied with the value and quality of roll formed parts.
How to Design a Great Roll Formed Part
Want to know more about designing great roll formed components? Download our free e-book below to learn more:
Editor's Note: This article was originally published in January 2016, and has recently been updated.
You May Also Like
These Related Stories
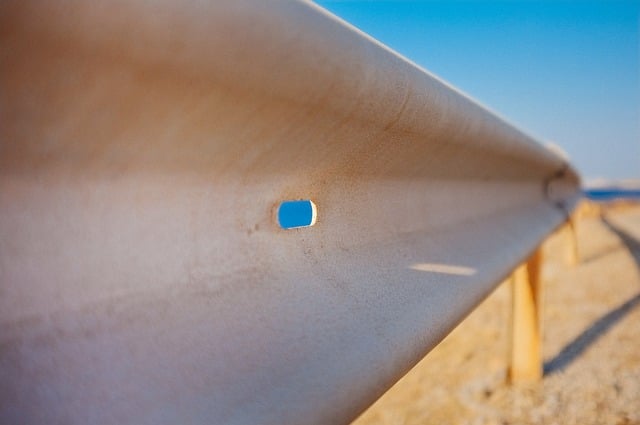
7 Roll Forming Products You (Probably) See Daily
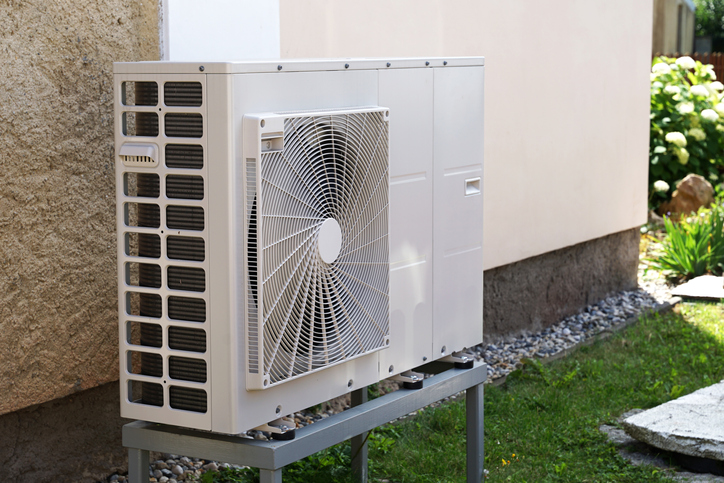
High-Quality Heat Pump Parts: Try Metal Roll Forming
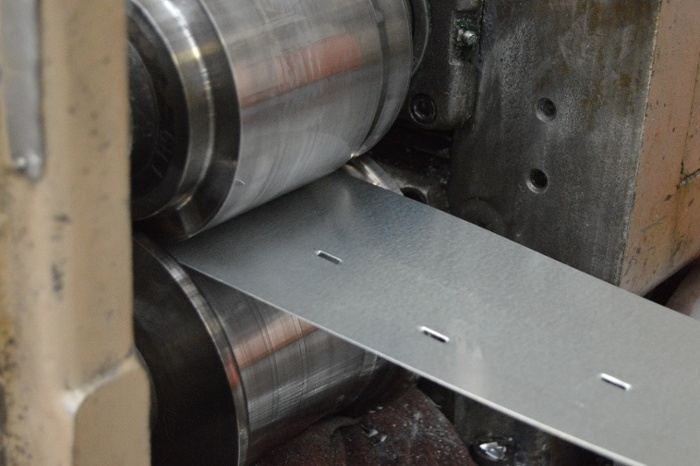