Dahlstrom Roll Form Company Turns 115 Years Old
Normally this space is all about you -- the engineer, the architect, the purchasing agent. Allow us to humbly brag about Dahlstrom Roll Form just this once.
It seemed like everyone’s grandfather or great-grandfather worked at Dahlstrom back in the day. “Back in the day” has turned into 115 years of world-class metal manufacturing.
If you walk around our home area -- Jamestown, N.Y. -- most of the people you talk to will be familiar with the Dahlstrom name.
“My uncle worked at Dahlstrom, and ever since I was a young boy I wanted to be part of that elite group in our town,” says Moe Loucks, who will hit his own 40-year anniversary at Dahlstrom on Feb. 5, 2019. “It’s how I grew up. I have met many interesting people over the years and developed many friendships.
“I have really enjoyed working for Dahlstrom.”
While the end products have changed over time, Dahlstrom’s innovative and reliable touch to manufacturing components and architectural metal products still remains. Keep reading to see how our little roll form company (now not so little) thrived (or, in the case of the Great Depression, survived) all this time:
Dahlstrom Roll Forming Company: 1904-Today
Invention of the First Fireproof Steel Door
In the beginning, there was Charles P. Dahlstrom. You might call him a man with an idea and the drive to develop it.
The idea took the form of the world’s first hollow metal swing door, and the drive resulted in Mr. Dahlstrom founding Dahlstrom Metallic Door Co. on Feb. 8, 1904. This hollow metal door was a game-changing contribution to the fireproofing and reduction of safety hazards in the skyscraper, a type of building starting to change the skylines throughout the nation.
The concept of the metal door coincided with the invention of the elevator, which paved the way for the construction of taller buildings. In addition, disastrous fires in New York and Chicago in the old, 10- and 12-story wooden buildings created a demand for fireproof entrances. New laws required all openings in these buildings be made with fireproof materials.
This need brought immediate success.
Dahlstrom Metallic Door’s first location was in the Gokey Building, located in downtown Jamestown. Just 2 years later, the business moved to its present location, a site which was then called Dexterville after early settlers of the area.
The location was a good one for the business because the adjacent Chadakoin River furnished water power, from which the plant manufactured its own electricity for a time. There was a railroad at hand for shipping, and land for expansion when needed.
To finance the new company, Mr. Dahlstrom obtained a certificate of incorporation from the Chautauqua County seat in Mayville and bought stock certificates, which he sold to friends in the area.
Dahlstrom was in business.
Architects and Manufacturers Catch On
The Dahlstrom door saw instant popularity with builders and architects. It was a logical step for the company to apply the same metal door concept to elevator entrances and cabs, and soon a major part of Dahlstrom’s contract business was for elevator doors. Its biggest customers were Otis Elevator, Westinghouse, Haughton, and Warner.
Because of its prime importance in modern buildings, the elevator lobby began to receive careful design attention from architects. Dahlstrom, with its highly skilled workers and craftsmen, answered the need for both a safe, fireproof door and an aesthetic flair. The design and craft work of Dahlstrom popped up in many prominent buildings through the United States, some of which stand today. Older famous buildings featuring Dahlstrom products include:
-
U.S. Express Building
-
Singer Building
-
Empire State Building
-
Department of Commerce and Interior in Washington, D.C.
-
Union Trust in Cleveland
In addition to the architectural line, specialty products evolved from the roll formed moldings and shapes and early on became a part of the Dahlstrom line. These rolled forms were originally developed to supply architectural trim for the metal doors, but the shapes and mouldings were soon being applied by manufacturers to their various products.
The auto industry took notice of Dahlstrom mouldings and trim, applying them to their dashboards and frames -- Packard was one of the biggest customers. However, because faster and lighter machines were developed that would churn out mouldings for autos with less expense, Dahlstrom dropped out of market because its heavier shapes could not compete. Yet, several decades later, local enthusiasts were still borrowing the old wood dies to do their own roll forming for the antique auto market.
Originally, forming was done with wooden dies using a draw bench, then steel rollers, and, in the 1920s with the advent of hardened steel, production efficiency and quality increased tremendously. With hardened steel, beautiful decorator trim could be made from harder stainless steels to be used on:
-
Doors
-
Buses
-
Cars
-
Cabinets
-
Frames
Dies for special shapes as well as stock dies for mouldings and shapes -- 1,000s of them -- were produced in the company’s own tool department to cut tooling costs. Almost any kind of shape that can be rolled or pressed can be fabricated by Dahlstrom.
The company continued to expand its product line as other technical advancements and new products were developed. The railway car trim sheets were another application of metal work pioneered by Dahlstrom, along with the sheet metal equipment for the first all-steel sleeping cars.
Cabinets built to specification for housing manufacturers’ mechanical equipment and products presented a wide range of problems to be resolved by Dahlstrom engineers and craftsmen. Through the years, Eastman Kodak, IBM, and Xerox were among the manufacturers in the computer and electronics industry who looked to Dahlstrom for the precision fabrication they require in their cabinets. The Super “C” steel floor joist eventually became another addition to the Dahlstrom product line and was welcomed by the building industry because of rapidly depleting lumber resources at the time. It also didn’t hurt that steel doesn’t warp, shrink, or rot.
Bankruptcy
During the 1930s, Dahlstrom experienced financial hardship and bankruptcy. Like many businesses, the company was overextended because of the booming 1920s. When the crash came, the tremendously depressed construction and building industry caused the market loss of Dahlstrom’s main product.
At the height of the Great Depression, only five out of 50 draftsmen still had a job. Desk and typewriters we were sold to meet the payroll.
In New York City, however, construction and building were still going on and the Rockefeller Center, then under construction, kept Dahlstrom’s doors open thanks to orders for 1,000 of doors. Paneling was also furnished by Dahlstrom for Radio City Music Hall. Dahlstom also got into the big housing projects in the New York City area at the same time. Metropolitan Life Insurance Co. began investing in housing, and Dahlstrom supplied the elevator doors for these projects.
In 1934, after a series of bank-appointed managers, Paul Anderson -- whose family owned a local furniture factory -- was elected president of Dahlstrom. He quickly set about the task of putting Dahlstrom back on its feet The company was refinanced. All outstanding stock was exchanged for a new stock issue on a 10-to-1 basis. Creditors settled for pennies on the dollar. As the economy recovered, the company managed to increase its working capital 3 years later by 10%.
World War II
The country’s recovery from a deep depression accelerated in 1939 when the war in Europe erupted with the march of the German Army into Poland. It was not long before the nation was again involved in “a war to end all wars.” Along with the rest of the country, Dahlstrom “joined up” and converted its facilities and turned the skill of its workers to the fabrication of war products.
Many items requiring close tolerances came off the production line, including:
-
Specialized aircraft parts
-
Marine doors
-
Waterproof boxes
In May 1943, the company received the Army-Navy E award, followed by “Star” awards in successive years, for its efforts.
After the war, Dahlstrom went back to the production of doors. But a few years later, when Otis Elevator started making its own doors and Westinghouse followed suite, Dahlstrom lost its largest market for elevator doors. Although the company continued to produce elevator entrances and cars, it became a costly product.
In addition, the ornate and beautiful inlay work of wood graining, etching, striping, and marbling by skilled craftsmen lost popularity due to increasing costs in labor and supplies. The market trended away from the finishes and went to prime coating, a much cheaper process. Thus the company phased out the product line which had made the Dahlstrom name known the world over.
A Company By Any Other Name
Through the years the company name has changed -- a lot.
-
Dahlstrom Metallic Door reflected the company’s early emphasis.
-
Dahlstrom Manufacturing Co. came next when the door product was gradually phased out.
-
Dahlstrom Corp. followed as the company began a period of acquisition.
-
Dahlstrom Manufacturing Company, Inc. was formed in June 1973 when the Jamestown Division of Dahlstrom Corp. was purchased by a group of local business owners and became a separate entity.
This mid-1970s period is when business began to take off again for Dahlstrom, according to company archives.
“In spite of supply shortages and (inflation), the results of an alert management team along with a good fiscal policy, plus good union relations and just plain hard work, have generated (greater) business than was first anticipated in so short a time,” an internal document from March 1974 reads.
“It is interesting to note the difference in financing a company in 1973 and one in 1904, when all one had to do was purchase stock certificates and sell them to whoever would buy. .... Organizations exist today (that) did not exist a few short years ago, which provide financial aid and capital to business.”
The business eventually settled in its current spot at 402 Chandler St. in Jamestown.
“Things have really changed since I started at Dahlstrom over 30 years ago,” says Phil Hall, director of product engineering & quality management systems. “I was originally hired as a quality manager within the sheet metal side of the business. An opportunity to work in corporate became available, which I accepted and allowed me to travel to our facilities in Florida and Ireland. We have moved from the original location to a more accommodating facility.
“So much as changed over the years, but care for the customer and their needs has remained a top priority, a key to our continued success.”
Several decades of flourishing have taken us to today -- and the name Dahlstrom Roll Form. Or does that name not sound familiar? Those who’ve visited our website or done business with us recently on the architectural side may have noticed a second logo and brand -- Dahlstrom Metal Mouldings.
Whether you’re familiar with Dahlstrom’s history in components for original equipment manufacturers (OEM) or architectural products, you can’t deny the fascinating history. Which leads us to ...
The Spirit of Innovation Still Lives Today!
The creator of the first fireproof steel door continues to innovate today.
“Working at Dahlstrom has given me the opportunity to see a tremendous advancement in automation and controls,” says Lynn Milliman, who will hit the 40-year mark. “When I started here, we rarely had roll forming jobs that needed pre-punching, and if we did do it, we made up manual triggering systems ourselves. They were kind of ‘hodgepodge,’ but they worked.
“Today, we have servo-controlled hole positioning and length control, machine memory for past jobs, and more computer interfaces. It’s been fun to watch all of that evolve.”
As Dahlstrom continues to evolve, new patents are coming. (Shhh -- we can’t tell yet.) Our ever-evolving catalog of 1,400+ mouldings is being updated.
The architectural side of our business -- Dahlstrom Metal Mouldings -- is growing steadily. Recent years have seen many more famous U.S. buildings use Dahlstrom architectural mouldings to add a touch of class, including U.S. Bank Stadium, the new home of the Minnesota Vikings.
On the OEM side, Dahlstrom has boasted uninterrupted ISO certification since 1995. We were one of the first in New York state to earn this seal of approval. And our self-imposed demand for continuous improvement has led to many other manufacturing floor updates to further streamline customers’ supply chains.
“I remember when I announced to the team at my prior employer that I was leaving to go to work with Dahlstrom,” Hall says. “Some thought that once I learned to do a take-off (flat to formed “development”), that I would be bored and would want to return. They were not even close.
“Since joining Dahlstrom in 1988, I have been very challenged and very pleased to be a part of such an interesting and dynamic industry, as well as such a wonderful company and team of professionals.”
Happy Birthday to You, Too!
While we’re pretty proud of this milestone, our 115th birthday is not a just celebration of the Dahlstrom name. It’s a big thanks to all the skilled workers past and present -- many of them and their kids and grandkids still sprinkled around Jamestown -- who’ve made the product world-class. And it’s a nod to the engineers and architects who dare to dream up new solutions right alongside us.
“I am proud to be part of a team that touches 115 years of history every day,” says Dahlstrom President Rob White. “Our growth and success has come from dedicated employees, relentless customer service, and great products. We look forward to a prosperous future.”
Here’s to another 115 years!
You May Also Like
These Related Stories
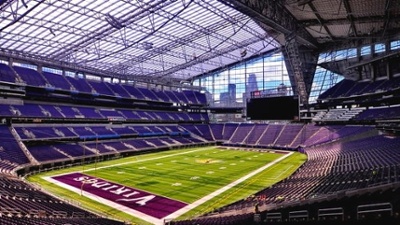
Famous Buildings With Dahlstrom’s Architectural Roll Forming: Part II
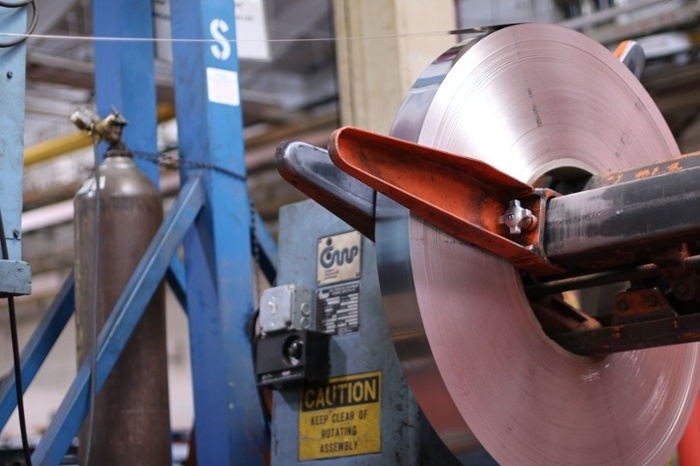
Roll Forming Design Guide for Sheet Metal Components
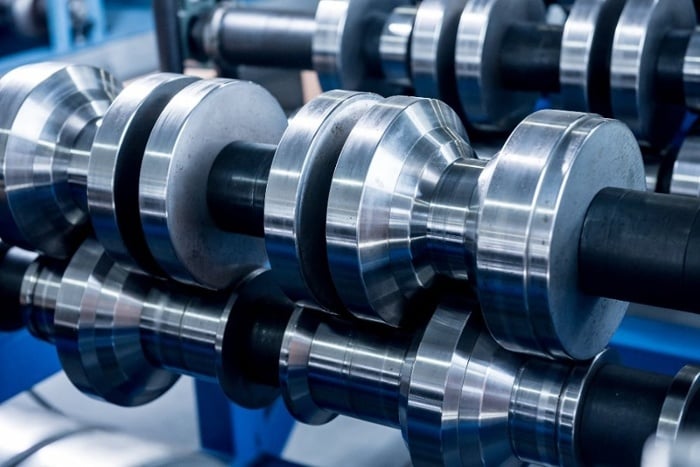