Career Advancement: See Yourself Growing at Dahlstrom
Are you always seeking to improve yourself and learn new things?
Are you looking for an employer who recognizes and rewards your knowledge?
You should consider a career at Dahlstrom.
Our 5 Year Plan
– Rob White, President |
The career path and advancement opportunities at Dahlstrom are a new take on the traditional shop floor system.
Dahlstrom’s 5-year training program is based on skill, not the number of years you’ve been with the company. If you can prove you know what you’re doing, you get paid like it.
Our trainings are broken up into 6-month modules. Every time you complete one you get a raise. And you don’t have to take the full 5 years to finish training. If you’re committed, you can advance quickly.
At Dahlstrom, we invest in you because we see you as an important part of our business. We are committed to delivering the best customer service possible, so we practice lean manufacturing. That starts with skilled professionals on the shop floor producing high-quality parts.
What Is Lean Manufacturing?
Lean manufacturing is broadly defined as “maximizing productivity while minimizing waste” (anything not providing value to customers). Waste in lean manufacturing is:
- Unnecessary movement of people, equipment, or machinery
- Excess inventory
- Waiting – either people or idle equipment
- Over-production of a product
- Over-processing or adding unnecessary features to a product
- Defects that require costly correction
- Unused talent and ingenuity
That “unused talent and ingenuity” is key – we don’t want employees’ talents going to waste. Continuous improvement is one of our priorities, and part of that is employee training and advancement.
Single-Minute Exchange of Dies
Single-Minute Exchange of Dies (SMED) is another piece of the lean manufacturing puzzle. To be lean, you have to be highly efficient in your processes. Every minute saved is savings for us and our customers.
SMED helps us shave off those precious minutes to improve lead time, reduce wasted manpower, and offer higher-quality service to clients.
5S Techniques
We practice the 5S techniques, which increase our company’s profitability by improving performance, morale, and quality of work. The 5S are:
- Sort, or simplify
- Straighten, or set in order
- Shine
- Standardize
- Sustain
These techniques make our shop floor safer by removing hazards and unnecessary items. They improve our communication and movement across work areas by decreasing clutter. And they increase our efficiency by reducing the amount of time spent looking for tools.
We’re also Safety and Health Acknowledgement and Recognition Program (SHARP) certified, meaning we’re recognized by OSHA for our exceptional safety practices.
Learn more about our shop:
Are You Ready for More?
We value our employees as an essential part of our business. Our employee benefits include:
- 5-year training program to get to top rate
- Biannual performance-based wage increases
- Boot and safety glasses allowance
- 401K contributions
- Healthcare, vision, and dental insurance
- Group profit bonuses
At Dahlstrom, we:
- Find a Way – We are resourceful.
- Deliver Legendary Customer Service – We go above and beyond to better serve our customers.
- Are Relentless About Improvement – We consistently identify areas for improvement.
- Keep Things Fun – We take our jobs seriously, but also have a little fun along the way.
Check out our Careers page for available positions.
You May Also Like
These Related Stories
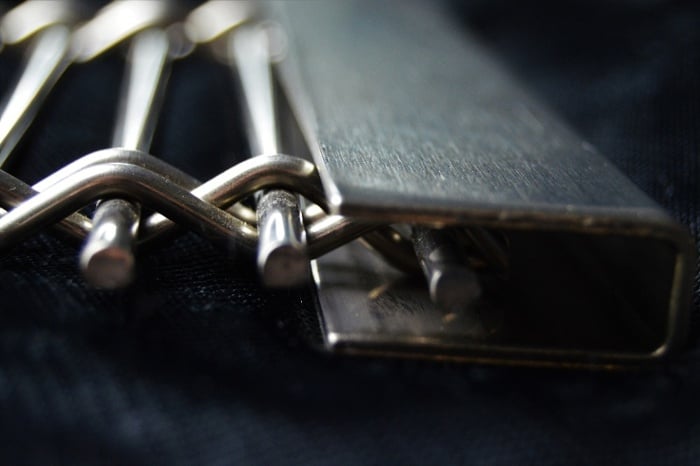
Create a Streamlined Supply Chain for Wire Mesh Frame
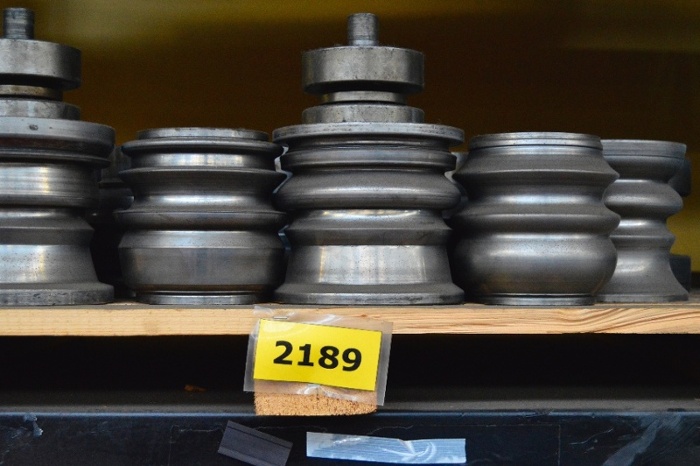
5S Lean Manufacturing Helps Roll Formers Produce High Quality Parts
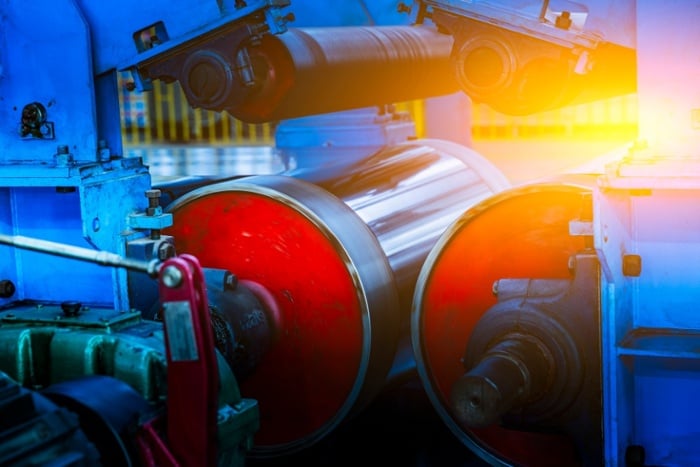