5 Types of Corrosion You (Probably) Don’t Know About
As a design engineer, corrosion is something you’re always watching out for when working with metal. And while you’re likely already familiar with several types of corrosion -- pitting, edge creep, exposure due to damage/scratches, etc. -- there are a lot of lesser-known variations you’d be wise to brush up on.
For instance, are you familiar with fretting? (No, not the kind your kids do.) What about flow-assisted corrosion? High-temperature corrosion?
There are others that you should definitely be aware of, too. Have a look:
(If want a helpful shortcut, click the button below to download a chart featuring key properties of several popular metals.)
5 Little-Known Types of Corrosion
Think you know corrosion? Here's a look at some that might impact your next metal project:
1. Fretting
When two metal surfaces make contact, usually either through rubbing or gnawing, fretting occurs. Fretting, also commonly referred to as “chafing erosion,” is essentially the gradual wearing down of two surfaces that regularly come into contact.
Over time, fretting can lead to vulnerable areas where protective or aesthetic coatings wear off or the metal piece itself wears down. If you’ve specifically requested a zinc-coated galvanized metal in an assembly for protection reasons, you can see how fretting would, well, make you fret.
Sometimes fretting happens due to a design flaw; other times there’s no choice but to have two parts rubbing together in an assembly.
2. Flow-assisted
Sometimes called “FAC” for short, this corrosion type occurs when a metal surface’s protective oxide layer dissolves in water.
For FAC to occur, the water must be very fast-flowing. This type of corrosion is common in pipes and tubing, and leads to accelerated metal loss when any underlying metal corrodes in an attempt to recreate the lost oxide layer.
3. De-alloying
Also known as “parting,” “selective leaching” and “selective attack,” de-alloying occurs when parts of a solid solution alloy corrode.
There are several things that can be done to prevent de-alloying, such as:
- Using metals resistant to it
- Controlling the environment in which the metals exist
- Using cathodic protection -- this turns active elements of a metal’s surface to passive through the magic of electricity
4. High-temperature:
As the name implies, high-temperature corrosion is corrosion that occurs at elevated temperatures, usually in situations where some sort of contaminant is also present, like fuel or gas.
This sort of corrosion is common in:
- Gas turbines
- Diesel engines
- Furnaces
Familiar types of high-temperature corrosion include oxidation, sulfidation, and carbonization.
5. Environmental stress cracking:
Though environmental stress cracking, or ESC, may be most often associated with thermoplastics, it can affect metal as well. Specifically, such cracks occur when both stress and some sort of corrosive liquid come into play.
ESC is largely unpredictable, despite being a challenge to developers for several decades. However, analyzing stress cracking resistance using the likes of the Bergen jig and Bell Telephone tests (named for its original use in Bell laboratories) can help better assess the potential for cracks.
Are Your Materials Up to the Challenge?
Are any of your applications particularly prone to these types of corrosion? This material properties chart shows the corrosion resistance levels of many of the most popular roll forming materials.
If you need more design assistance specific to roll forming or corrosion resistance, it’s best to speak with the vendor ahead of time. Creating a great roll formed part is about more than just getting it out the door -- it’s also about making sure it stands the test of time.
You May Also Like
These Related Stories
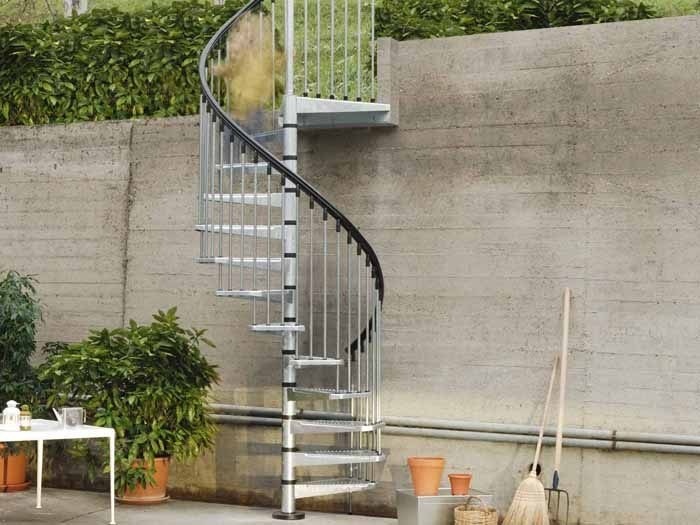
Try The Next Level of Economical Outdoor Metal Corrosion Protection
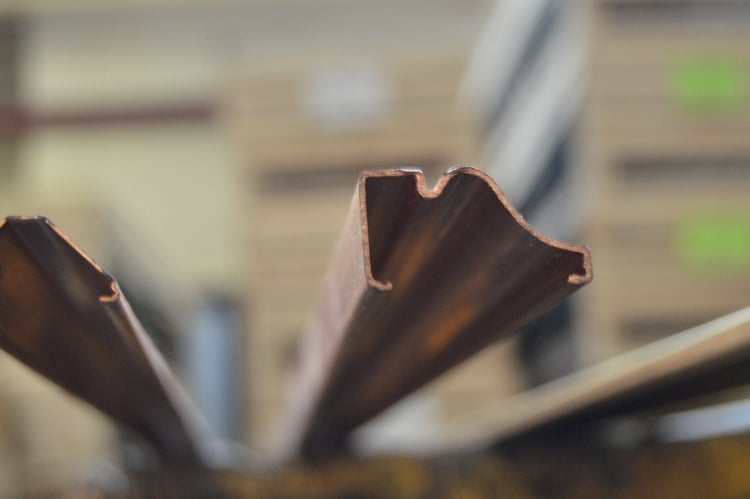
Top 10 Metal Standard Moulding Profiles Loved by Architects/Designers
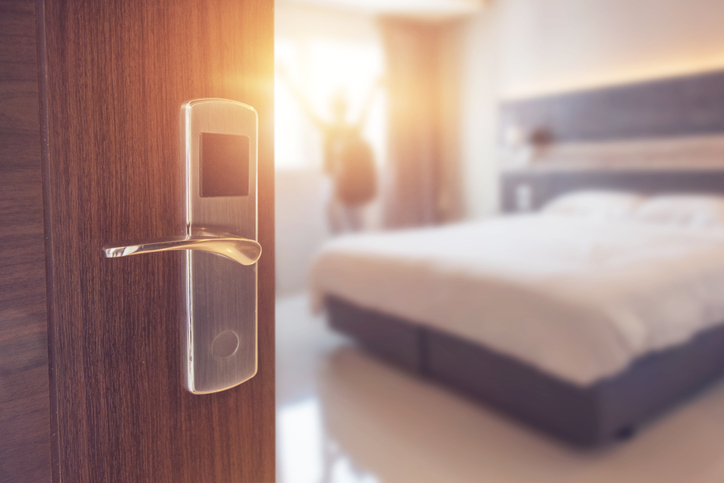